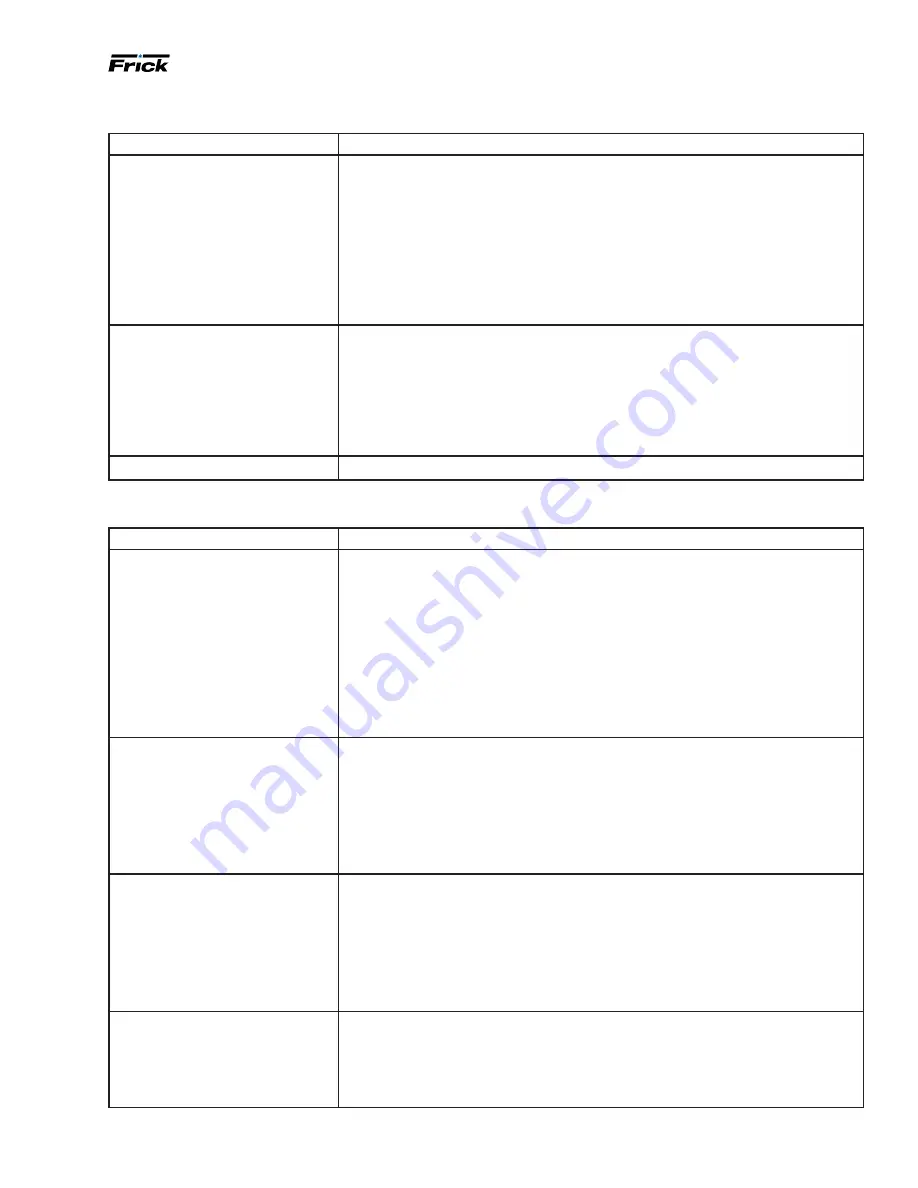
070.610-IOM (JUL 21)
Page 51
RWF II Rotary Screw Compressor Units
Maintenance
Troubleshooting the hydraulic system
Symptom
Probable causes and corrections
Slide valve will not load or
unload
Solenoid coils may be burned out. Test and replace if necessary.
Valve may be closed. Open hydraulic service valves.
Solenoid spool may be stuck or centering spring broken. Replace.
Check outputs 2 and 3 and fuses.
Check LED on coil. If lit, there is power to the coil. Check coil.
Solenoid may be actuated mechanically by inserting a piece of 3/16 in. rod
against armature pin and pushing spool to opposite end. Push A side to
confirm unload capability. If valve works, problem is electrical.
Slide valve will load but
will not unload
A side solenoid coil may be burned out. Test and replace if necessary.
Dirt inside solenoid valve preventing valve from operating both ways. Clean.
Check LED on coil. If lit, valve is functioning mechanically. Problem is electrical.
Solenoid may be actuated mechanically by inserting a piece of 3/16 in. rod
against armature pin and pushing spool to opposite end. Push A side to
confirm unload capability. If valve works, problem is electrical.
Slide valve will unload but
will not load
A side solenoid coil may be burned out. Test and replace if necessary.
Dirt inside solenoid valve preventing valve from operating both ways. Clean.
Check LED on coil. If lit, valve is functioning mechanically. Problem is electrical.
Solenoid may be actuated mechanically by inserting a piece of 3/16 in. rod
against armature pin and pushing spool to opposite end. Push A side to
confirm unload capability. If valve works, problem is electrical.
Slide stop will not function
either direction
Solenoid coils may be burned out. Test and replace if necessary.
Solenoid service valves may be closed. Open.
Manually actuate solenoid. If slide stop will not move mechanical problems
are indicated. Consult Frick factor or Frick service.
Troubleshooting the oil separation system
Symptom
Probable causes and corrections
Gradual oil loss with an oil
level in the coalescer
section sight glass
Maintaining too high an oil level, lower level.
Refrigerant carryover or liquid injection overfeed ing, correct operation.
Loss of suction superheat. Adjust evaporator feeds.
Contaminated oil, damaged or not seated coalescer filter elements. Replace
oil charge and coalescers.
Coalescer return valve closed. Open return valve.
Coalescing oil return line strainer blocked. Clean.
Rapid loss with no oil level
in the coalescer section
sight glass
On shutdown, compressor unit suction check valve did not close. Repair valve.
Suction check valve bypass valve open too far to meter flow. Close valve.
Coalescers loose or not seated properly. Correct or replace.
On economized unit: economizer check valve not working. Repair or replace.
Economizer check valve not in automatic position or manually opened. Place in auto position.
Shaft seal leakage
If leakage exceeds normal allowable rate of 7 drops per minute, replace seal.