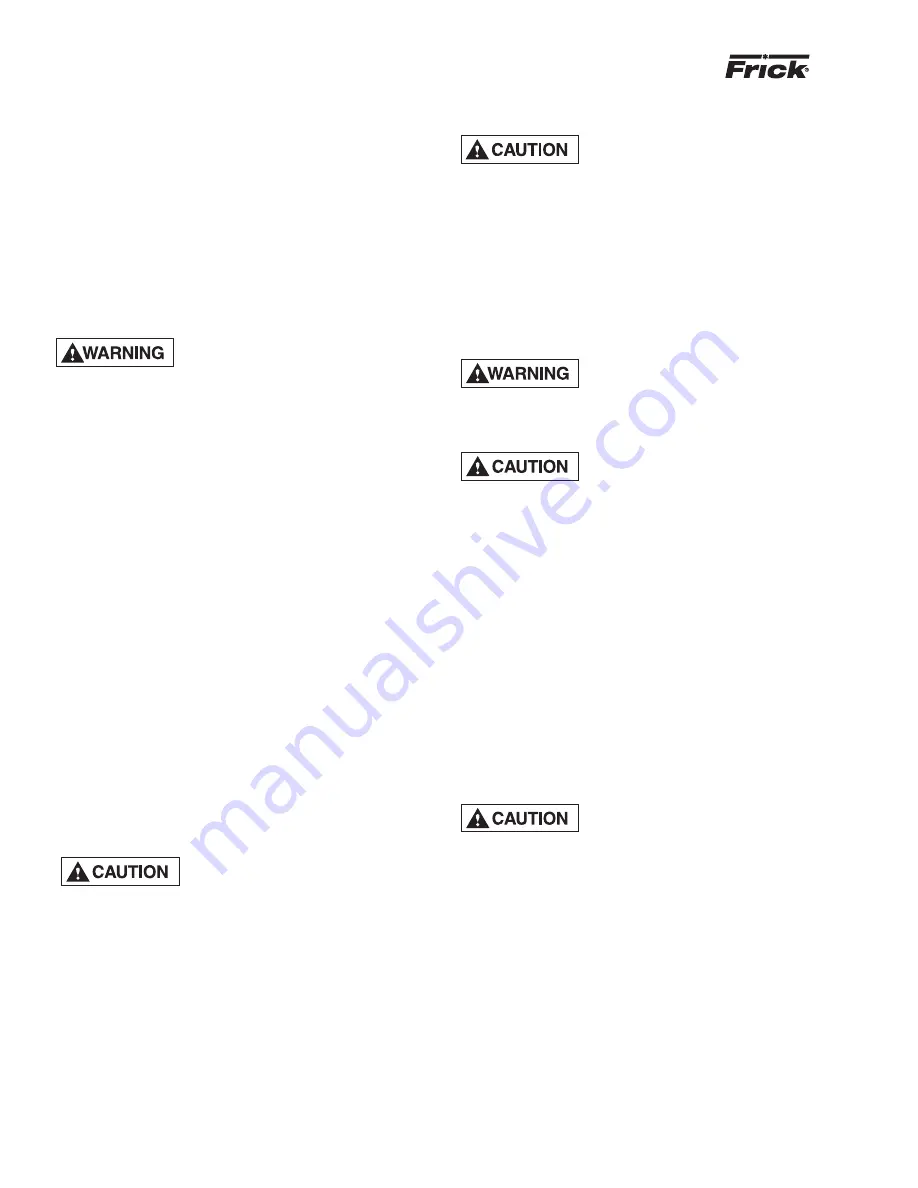
RWB II ROTARY SCREW COMPRESSOR UNITS
MAINTENANCE
S70-200 IOM
Page 24
down. The procedure is as follows:
1. Push [STOP] key on microprocessor panel to shutdown
unit, then open disconnect switches for compressor and oil
pump motor starters.
2. Close liquid supply service valve located before liquid so-
lenoid.
3. IMMEDIATELY SCREW IN THE MANUAL SOLENOID
VALVE STEM TO RELIEVE LIQUID REFRIGERANT PRES-
SURE TRAPPED BETWEEN THE SOLENOID AND THE
SERVICE VALVE.
Excessive pressure from expanding refrigerant trapped
between stop valve and solenoid may cause gasket and
O-ring failure and uncontrolled refrigerant release.
4. Close service valve located be-
tween the compressor and the liquid
injection thermovalve.
5. Carefully loosen capscrews securing the strainer cover to
the strainer. Allow pressure to relieve slowly.
6. When all entrapped refrigerant has been relieved, care-
fully remove loosened capscrews (as liquid refrigerant is
sometimes caught in the strainer), strainer cover and strainer
basket.
7. Wash the strainer basket and cover in solvent and blow
clean with air.
8. Reassemble strainer.
9. Open service valve between compressor and liquid injec-
tion thermovalve and check for leakage.
10. Screw out manual solenoid valve stem.
11. Carefully open liquid supply service valve.
12. Leak test.
13. Close disconnect switches for compressor and oil pump
motor starters.
14. Start unit.
COALESCER FILTER ELEMENT(S)
Use of filter elements other than Frick must be approved
in writing by Frick engineering or warranty claim may be
denied.
When changing the coalescer filter
element(s) it is recommended that the
oil be changed, cartridge(s) in oil fil-
ters OF-1, OF-2, and OF-3 if appli-
cable be changed and the following applicable strainer ele-
ments be removed and cleaned.
1. Refer to oil changing Steps 1 through 8.
2. Loosen manway cover retainer bolts, remove retainers,
manway cover and cover gasket. Discard cover gasket.
3. Remove and retain nut securing coalescer filter retainer.
4. Remove retainer, coalescer filter element and 2 O-rings.
Discard filter elements.
5. Install new coalescer filter element(s).
Seat element in center of locating tabs on separator bulk-
head.
6. Replace coalescer filter retainer and
nut. Torque nut to 21 ft-lb. DO NOT
OVERTIGHTEN NUT.
7. Install a new manway gasket and replace manway cover.
8. Tighten manway bolts. NOTE: RETIGHTEN AFTER THE
COMPRESSOR UNIT IS REPRESSURIZED, SINCE MAN-
WAY BOLTS WILL LOOSEN.
9. Refer to oil changing Steps 9 through 14.
CHANGING OIL
DO NOT MIX OILS of different
brands, manufacturers, or types.
Mixing of oils may cause excessive
oil foaming, nuisance oil level cutouts, oil pressure loss,
gas or oil leakage and catastrophic compressor failure.
Use of oils other than Frick Oil in
Frick compressors must be ap-
proved in writing by Frick engineer-
ing or warranty claim may be denied.
Shut down the unit when changing oil. At the same time all
oil filter cartridges must be changed and all oil strainer ele-
ments removed and cleaned. The procedure is as follows:
1. Press the [STOP] key on the microprocessor panel to stop
the compressor unit.
2. Open the disconnect switch for the compressor motor
starter.
3. Close the suction and discharge service valves; also close
the liquid-injection and economizer service valves, if appli-
cable.
4. SLOWLY vent separator to low-side system pressure us-
ing the bypass line on the suction trap. NOTE: Recover or
transfer all refrigerant vapor, in accordance with local
ordinances, before opening to atmosphere. The separa-
tor MUST be equalized to atmospheric pressure.
Oil entrained refrigerant may vapor-
ize, causing a separator pressure
increase. Repeat venting and recov-
ery procedure, if necessary.
5. Open the drain valve(s) located on the underside of the
separator and drain the oil.
6. Drain the oil filter(s) OF-1 and, if applicable, the oil coolers
and filter OF-2.
7. Remove the old filter cartridges, then install new ones (as
previously described in the section OIL FILTER (OF-1) MAIN
SINGLE/DUAL).
8. Remove, clean, and reinstall strainer elements in the
strainers.
9. Evacuate the unit to 28" Hg vacuum.
10. Open the suction service valve and pressurize the unit to
system suction pressure. Close the suction valve and leak
test.