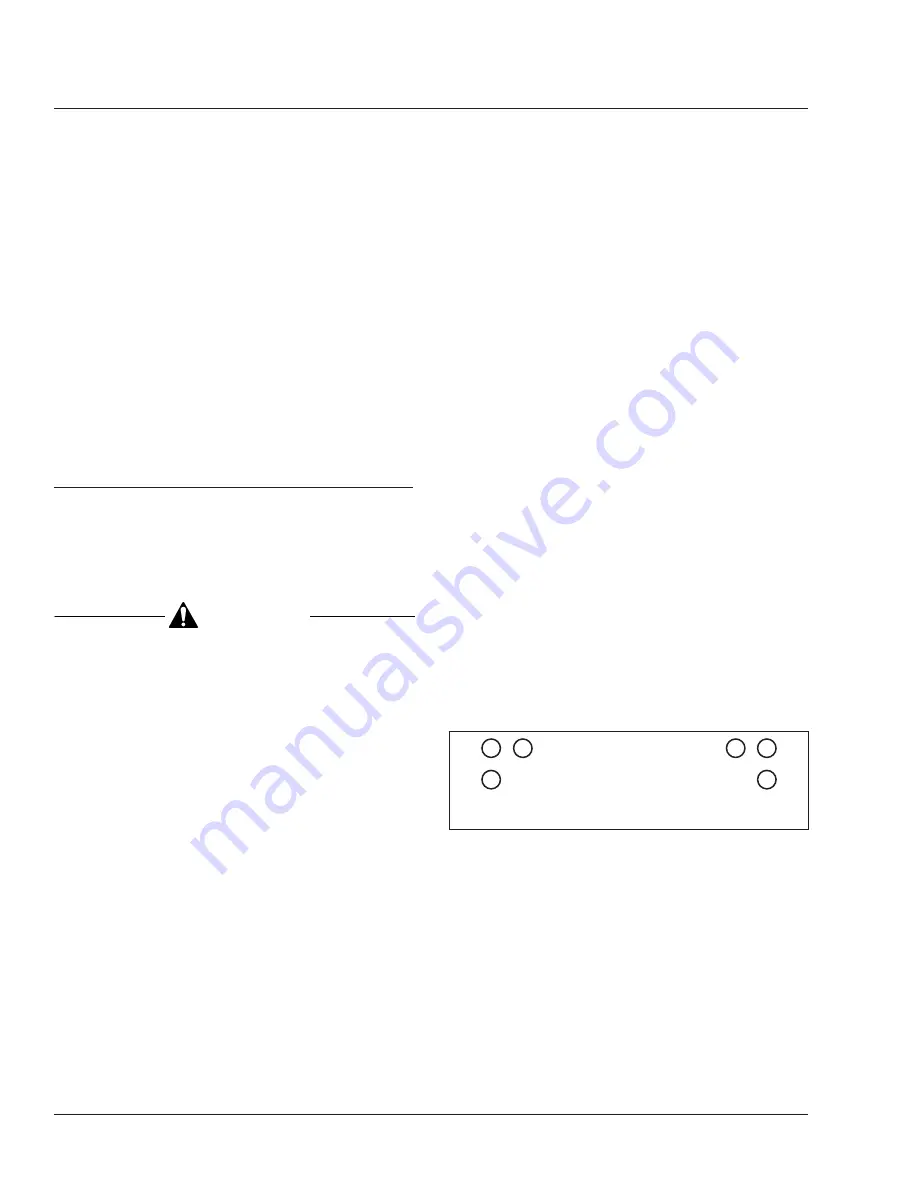
Check the plunger for signs of wear or cracks.
Replace it if necessary.
9.
Lubricate the plunger with barium grease (BW
246671).
10. Insert the plunger in the valve.
11. Install the brake pedal with the pivot pin.
12. Install a new roll pin and apply Torque Seal
(OPG F900 White) to the roll pin.
13. Install the brake valve assembly; see
Group 42
,
of the vehicle Workshop Manual.
14. Test the brakes before returning the vehicle to
service.
42–13 Brake Inspection
Parking Brake Operational Check
IMPORTANT: This procedure should be per-
formed prior to lubrication of the brake compo-
nents.
CAUTION
Perform the following check in a clear safe area. If
the parking brakes fail to hold the vehicle, per-
sonal injury or property damage may result.
1.
With the engine running, and air pressure at cut-
out pressure, set the parking brake.
2.
Put the vehicle in the lowest gear and gently at-
tempt to move it forward. The vehicle should not
move. If the vehicle moves, the parking brakes
are not operating correctly and must be repaired
before the vehicle is returned to service. See
Group 42
of the vehicle Workshop Manual for
repair procedures.
Brake Component Inspection
Air Disc Brakes
IMPORTANT: The following step to inspect the
caliper mounting bolts should only be performed
at the initial maintenance (IM) interval.
Vehicles may have both
axial and radial
mounted calipers. Follow the instructions based
on the type of calipers installed on the vehicle.
Axial Mounted Brakes
IMPORTANT: The following information applies
to all types of axial mounted brake applications.
1.
Park the vehicle on a level surface, shut down
the engine, and set the parking brake. Chock the
tires.
2.
Raise the vehicle and support it on jack stands.
3.
Remove all of the wheel assemblies. For instruc-
tions, see
Group 40
of the vehicle workshop
manual for repair procedures.
NOTE: In all steps that require a torque wrench,
use a Snap On torque wrench ATECH4RS600,
or an equivalent, with a center to handle length
of 47 inches (119 cm).
4.
Set a torque wrench to 350 lbf·ft (475 N·m) and
tighten the caliper mounting bolts following the
tightening pattern shown in
. If they do
not turn, no further work is needed. If they turn,
take the vehicle to an authorized Freightliner
dealer to have all of the caliper bolts on that
wheel end replaced. Due to limited caliper bolt
access, it may be necessary to use tool DDC
DSNCHA018005 referenced in tool letter
18TL18. If the tool is needed, use tool DDC
DSNCHA018005 only and no other tools. See
. If the tool is needed, see
for
torque specifications for a 47 in (119 cm) long
wrench.
f422665
10/02/2018
1
2
4 5
3
6
Fig. 10, Axial Bolt Tightening Pattern
Brakes
42
Business Class M2 Maintenance Manual, November 2019
42/12
Summary of Contents for BUSINESS CLASS M2 100
Page 2: ......
Page 10: ......
Page 30: ......
Page 34: ......
Page 36: ......
Page 38: ......
Page 40: ......
Page 42: ......
Page 46: ......
Page 52: ......
Page 60: ......
Page 62: ......
Page 76: ......
Page 82: ......
Page 84: ......
Page 94: ......
Page 104: ......
Page 110: ......
Page 112: ......
Page 114: ......
Page 116: ......
Page 120: ......
Page 122: ......
Page 144: ......
Page 146: ......
Page 150: ......
Page 152: ......
Page 166: ......
Page 168: ......
Page 178: ......
Page 180: ......
Page 184: ......
Page 186: ......
Page 188: ......
Page 190: ......
Page 192: ......
Page 196: ......
Page 198: ......