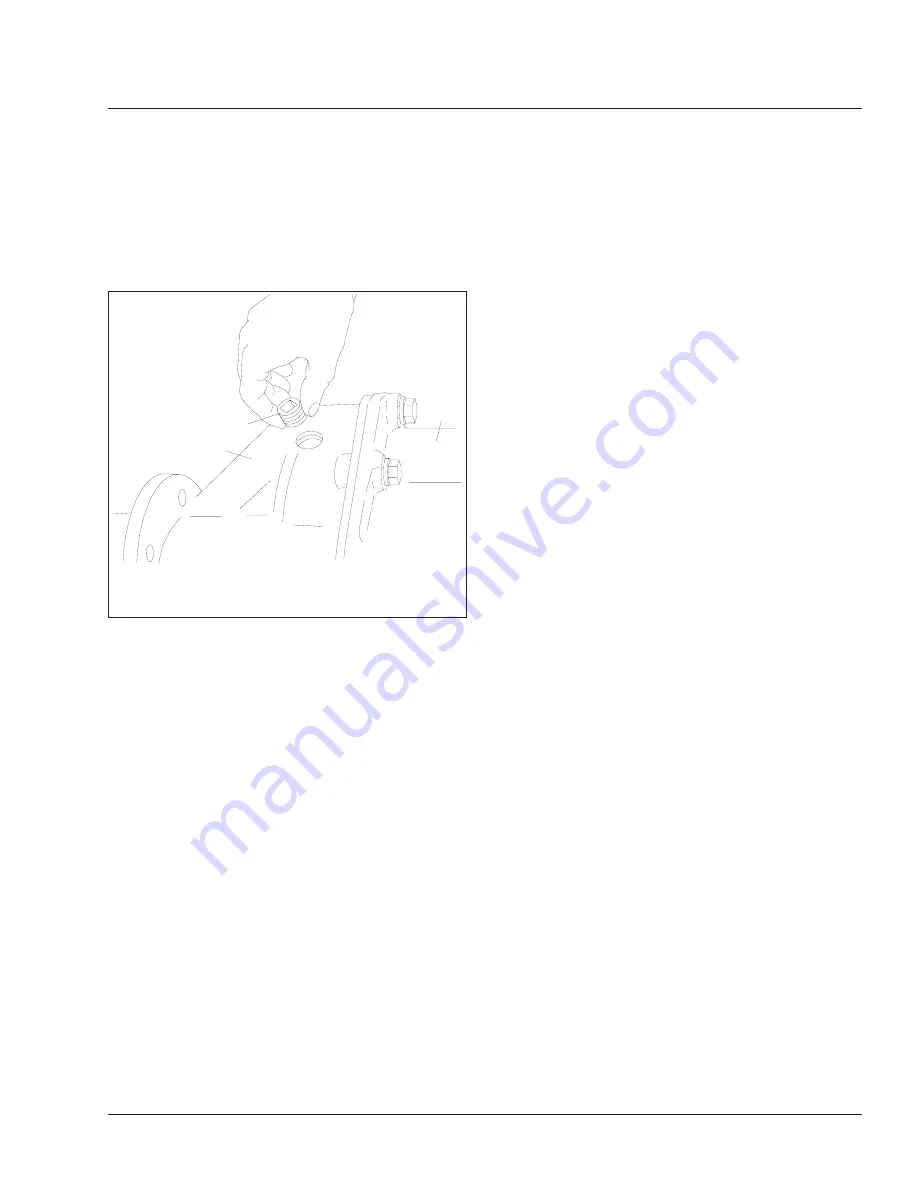
Add two pints (1 L) of lubricant through
this fill hole. Do not use the hole at the
top
of the differential carrier as a fill hole.
Install and tighten the fill plug 40 to 60
lbf·ft (54 to 81 N·m).
9.
For a two-speed axle with a shift unit, change
the shift unit lubricant; see elsewhere in this
maintenance operation for the shift unit lubricant
changing procedure.
Meritor
Single drive axles equipped with traction equalizers
may require a "limited-slip friction modifier" to correct
a slip-stick condition, as described in the vehicle driv-
er’s manual. Meritor’s experience shows that the fol-
lowing additives (friction modifiers) perform ad-
equately:
A. For all synthetic gear oils other than Mobil, add
1.6 ounces (35 mL) of additive for each pint (0.5
L) of lube capacity:
•
Elco No. 2 Friction Modifier (Elco Corpora-
tion).
•
Lubrizol No. 6178 (Lubrizol Corporation).
•
Hi-Tec E-336 (Edwin Cooper, Inc.).
•
Equa-Torque No. 2411 (Sta-Lube Corpora-
tion).
•
Equa-Torque No. 2414 (Sta-Lube Corpora-
tion).
B. For Mobilube SHC (synthetic) use Mobil No. 204
(Mobil Oil Corporation). Add 1.1 ounces (23 mL)
of additive for each pint (0.5 L) of lube capacity.
IMPORTANT: These friction modifiers generally
deteriorate faster than conventional extreme-
pressure additives, so the lubricant change
schedule must be shortened when using these
additives. The traction equalizer additive (and
recommended drive axle lubricant) must be
changed at the Maintenance 2 (M2) interval,
instead of the Maintenance 3 (M3) interval rec-
ommended in the Maintenance Operation Chart
for axles that require only those lubricants rec-
ommended in
1.
Park the vehicle on level ground, apply the park-
ing brakes, and chock the tires.
2.
Remove the axle carrier fill plug (see
then remove the drain plug from the bottom of
the housing and completely drain the lubricant
while the unit is warm. Allow sufficient time for all
old lubricant to drain. On dual drive axles, it is
also necessary to remove the plug at the bottom
of the interaxle differential housing to drain the
lubricant.
3.
If so equipped, replace the axle oil filter. Remove
the oil filter, using a suitable filter strap wrench.
See
. Discard the filter.
NOTE: There may be about one pint (0.5 L) of
lubricant remaining in the filter. Be careful not to
spill it when removing the filter.
4.
Using the specified drive axle lubricant, coat the
face of the gasket on a new oil filter. Install the
filter over the adapter, and tighten the filter one
full turn after the gasket contacts the base; do
not overtighten the filter.
5.
For a new or reconditioned axle, flush the axle
with clean flushing oil, then drain it thoroughly. It
is necessary to flush the axle the first time (only)
that the axle lubricant is changed.
f350019a
1
05/27/93
2
3
1.
Fill Plug
2.
Power Divider
3.
Forward Differential
Carrier
Fig. 4, Power Divider Fill Plug
Rear Axle
35
Century Class Trucks Maintenance Manual, April 2005
35/3
Summary of Contents for Argosy COE
Page 41: ......