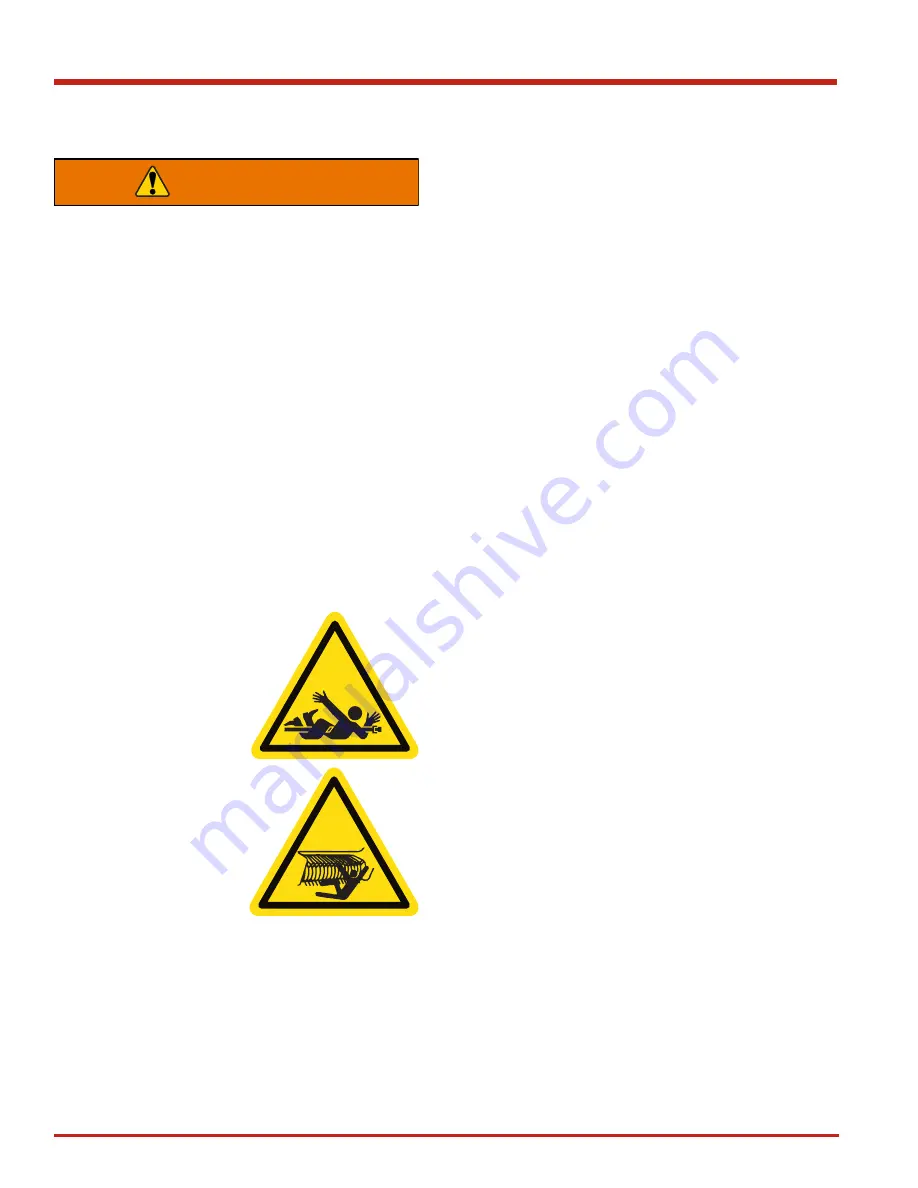
4
89-052
Rev: 1/2020
Operation Warnings
WARNING
Warning: Failure to observe the following safe-
ty rules may result in extreme personal injury,
dismemberment or death. It is the operator’s
responsibility to understand the proper and
safe use of this baler.
•
Make sure that you read, understand, and obey
all of the safety precautions and operating instruc-
tions in this Operator’s Manual.
•
Keep this Operator’s Manual and the Safety Card
(Allied form #89-028) with the baler at all times.
•
Do not operate the baler unless you are authorized
and trained to do so. If it has been some time
since you last operated the baler, re-familiarize
yourself with the baler before starting, then pro-
ceed slowly.
•
Do not operate the baler if you are aware of any
malfunctions, needed maintenance or repairs.
•
Stop the baler immediately if any problems arise.
•
Never allow others to ride on the baler.
•
Never allow anyone
within 10 ft of the baler
while the baler is in
operation.
•
Never operate the baler
without all safety shield-
ing in place.
•
Keep hands, feet, hair,
jewelry and clothing
away from moving
parts, including but not
limited to the pickup,
knotter, and PTO shaft.
•
Avoid wearing loose
clothing which can eas-
ily be caught in moving
parts.
•
Use appropriate signs (i.e., Slow Moving Vehicle
sign), signals or warning lights when transporting
on highways.
•
Always use lights when working at night or in low
light conditions.
•
Know your job-site rules. Some have site specific
directions and procedures. The methods outlined
in this manual provide a basis for safe operation
of the baler. Because of special conditions, your
company’s baling procedures may be somewhat
different from those shown in this manual.
•
Do not start the tractor if the key had been marked
with a “DO NOT START” or “RED” tag.
•
Never operate any of the tractor’s controls from
anywhere other than the operator’s seat.
•
Alert personnel in the area before starting the
engine, and make sure everyone is clear. Be sure
that all controls are in neutral and the baler is dis-
engaged before starting the engine.
•
Each country has its own safety legislation. It is in
the operator’s own interest to be conversant with
these regulations and to comply with them in full.
This also applies to local bylaws and regulations in
force on a particular worksite.
•
Should the recommendations in this manual devi-
ate from those in the user’ country, the national
regulations should be followed.
•
Never attempt to disconnect any of the safety
devices built into the baler or tractor.
•
Maintain proper clearance from energized equip-
ment, energized power lines or other power
sources. High voltage electricity can discharge to
ground without direct contact with the baler’s or
tractor’s structure. If the baler or tractor contacts
energized equipment, or if electrical energy does
discharge through the machine—stay clear, and
prevent anyone else from coming in contact with
the baler or tractor. If you are on the tractor, stand
fast, avoid contact with metal surfaces, and do not
permit anyone to come into contact with the tractor
or baler. Finally,
Do not jump off
.