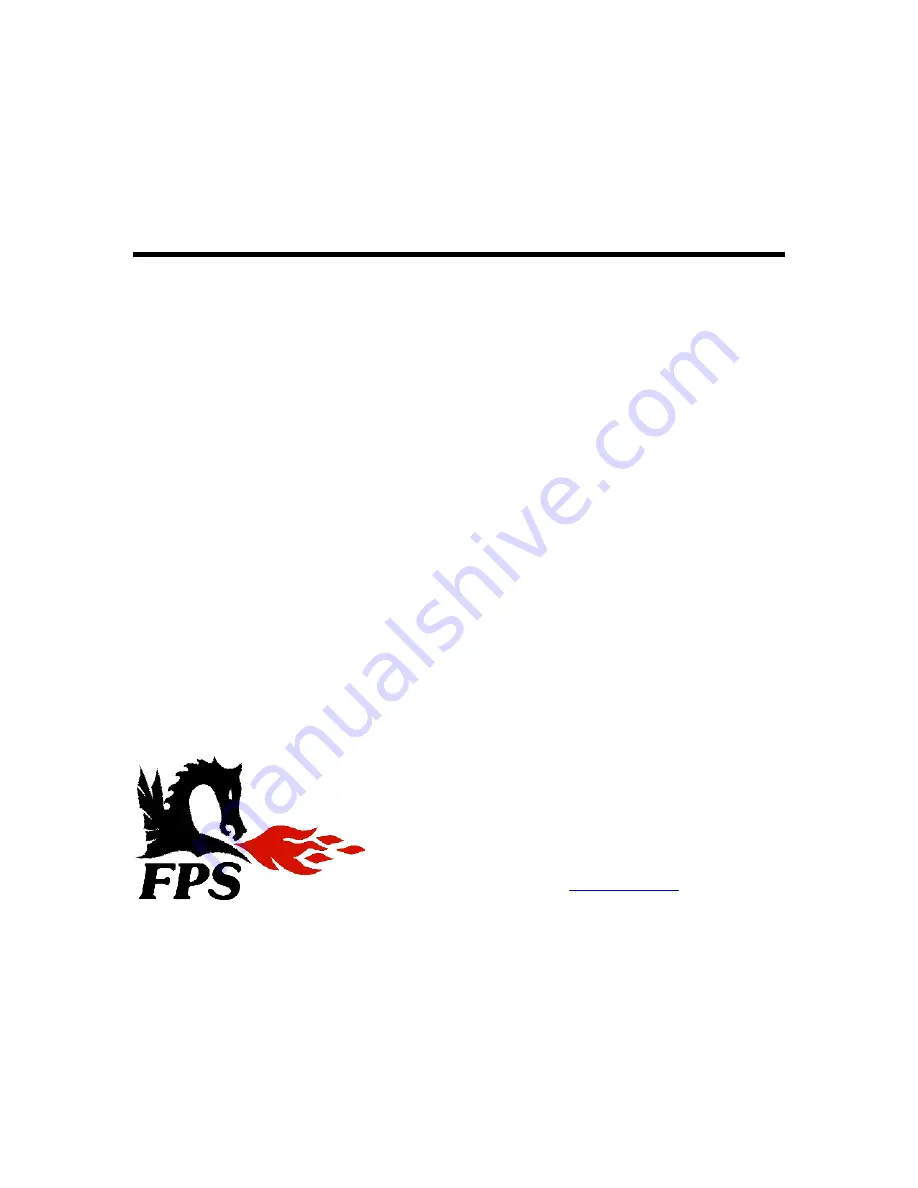
9650 Valve Series
Installation
And Maintenance Manual
July 2019
Fossil Power Systems Inc.
10 Mosher Drive
Dartmouth
Nova Scotia, Canada,
B3B 1N5
Tel: 1 902 468 2743
Fax: 1 902 468 2323
E-mail:
Web: wwww.fossil.ca