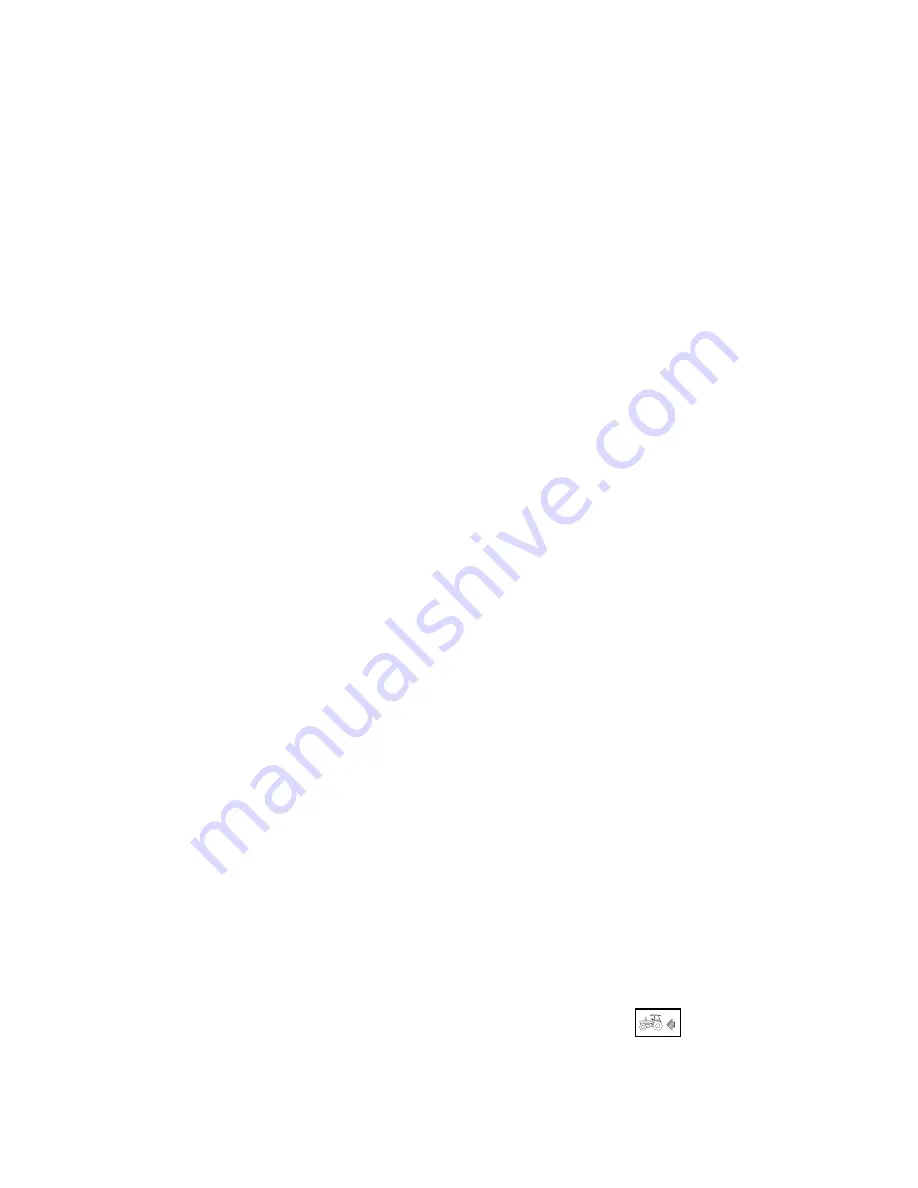
AERA-vator to tilt backwards when lifting allowing gravity to assist the swing chains in align-
ing the unit with the tractor. DO NOT ADD ADDITIONAL WEIGHT TO THE AERA-vator
OR APPLY DOWN PRESSURE TO THE TRACTOR LIFT LINKS DURING OPERATION.
•
The geometry of tractor lift linkages varies, and a trial run over uneven ground is recom-
mended. Ideally the swing lock will not engage when aerating over the crown of a hill and
the tractor hitch is always free to float upward at all times. The tines should clear curbs
etc., when lifted.
•
When lowering for operation, lower slowly until the tines touch the ground. Then swiftly
push the lift control lever on the tractor to the completely lowered position to instantly
unlock the hitch. This is especially true when lowering the unit in a sharp turn. Failure to
do this may cause the swing hitch not to disengage, resulting in damage to the machine
and/or turf damage. In the event the unit should fail to unlock for trail mode, stop the trac-
tor and repeat the lowering procedure.
DO NOT TURN THE TRACTOR WITH THE AERA-vator IN THE GROUND AND THE
SWING LOCK ENGAGED. DAMAGE TO EQUIPMENT MAY OCCUR!
•
When operating diagonally downhill or transversely (sideways) on a hillside slope above
5
°
the mast chains will not swing the unit uphill to center and lock on the tractor when the
unit is lifted. Occasionally the unit will swing farther to the downhill side of the tractor
creating the hazard of tractor roll over. If the tractor ever seems unstable, immediately
lower the hitch and steer the tractor uphill or on a more level surface where it will center
and lock when lifted.
•
Do not back the unit up with the AERA-vator touching the ground. Always disengage the
PTO, raise the unit, back to desired location and then lower the machine and engage the
PTO.
•
The operating ground speed of the tractor will depend on the amount of soil agitation re-
quired. Slower tractor ground speed (lower gears) will be used for renovating in extremely
hard dry ground. Faster tractor ground speeds (higher gears) will be used for aeration work
in normal conditions. To reduce the amount of soil agitation simply reduce the engine
RPM. Three to four miles per hour is the most common speed range.
PRE-OPERATION CHECK LIST
(With the AERA-vator lowered and the tractor engine switched off...)
•
Be sure that the implement is hitched to the tractor properly with all pins in place.
•
Pin the swing stand in the up position.
•
Be sure the driveline is correctly assembled.
(The end stenciled as the tractor end is con-
nected to the tractor and not to the AERA-vator). Check to see that the end yokes are
8