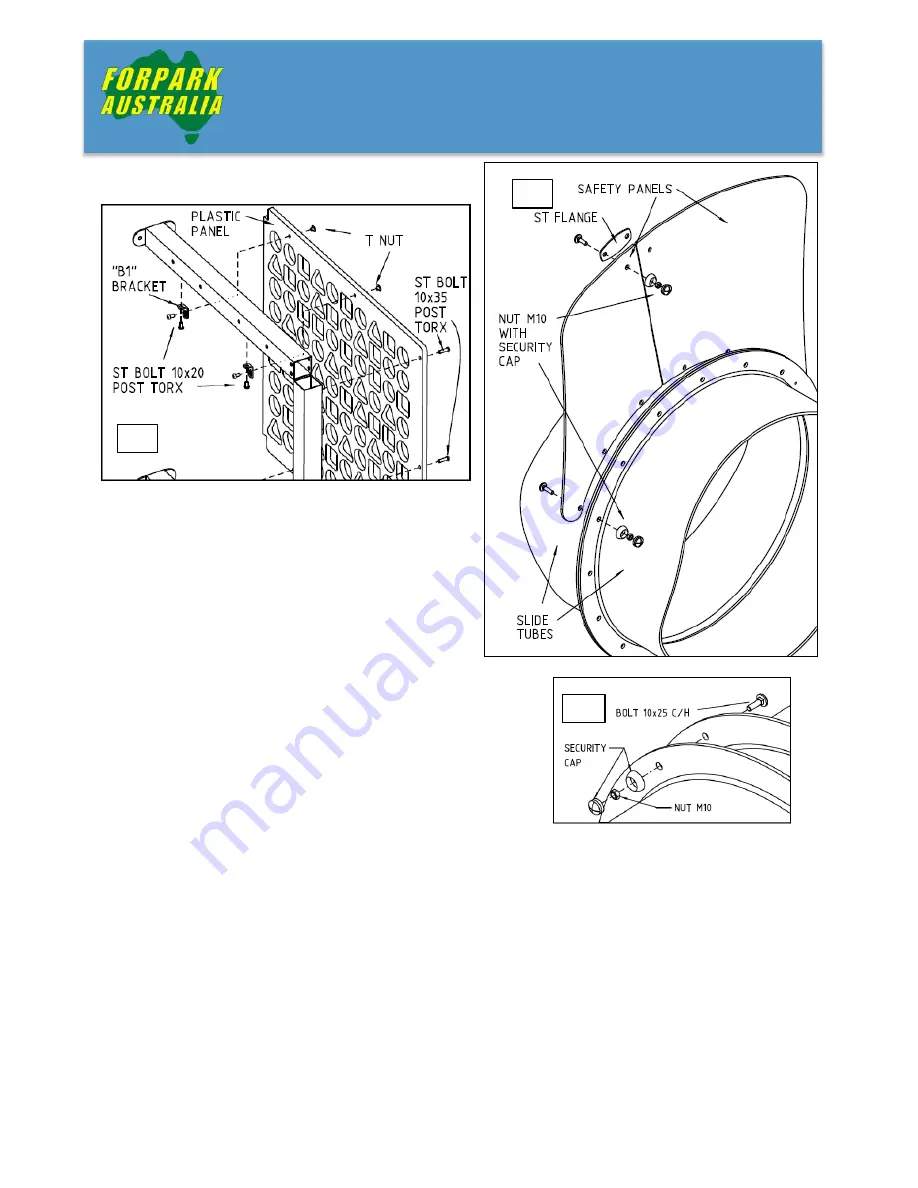
9
FORPARK AUSTRALIA | www.forparkaust.com.au
14.
Use the holes on roof to remove crane ropes.
15.
Climb to the first level and assemble according
to the plan the access to level 2. Do the same for
level 3. Platform frames need drilling and
tapping for rope end flanges and plastic panels.
16.
Build all slides using standard Tunnel slide
assembly and according to the plan.
The orientation of each tunnel section is
determined using a process referred to as
“cranking”. Cranking consists of placing the
flanges of both sections together with the seams
of the section to be attached aligned to the
seams of the previous section, and rotating it either
clockwise or anti-clockwise by the required number of bolt
holes in the flanges. (For example, 3 cranking steps would
involve rotating the section by 3 bolt holes.) Note:
Clockwise is determined while standing on the ground,
facing the slide up.
16
16
15