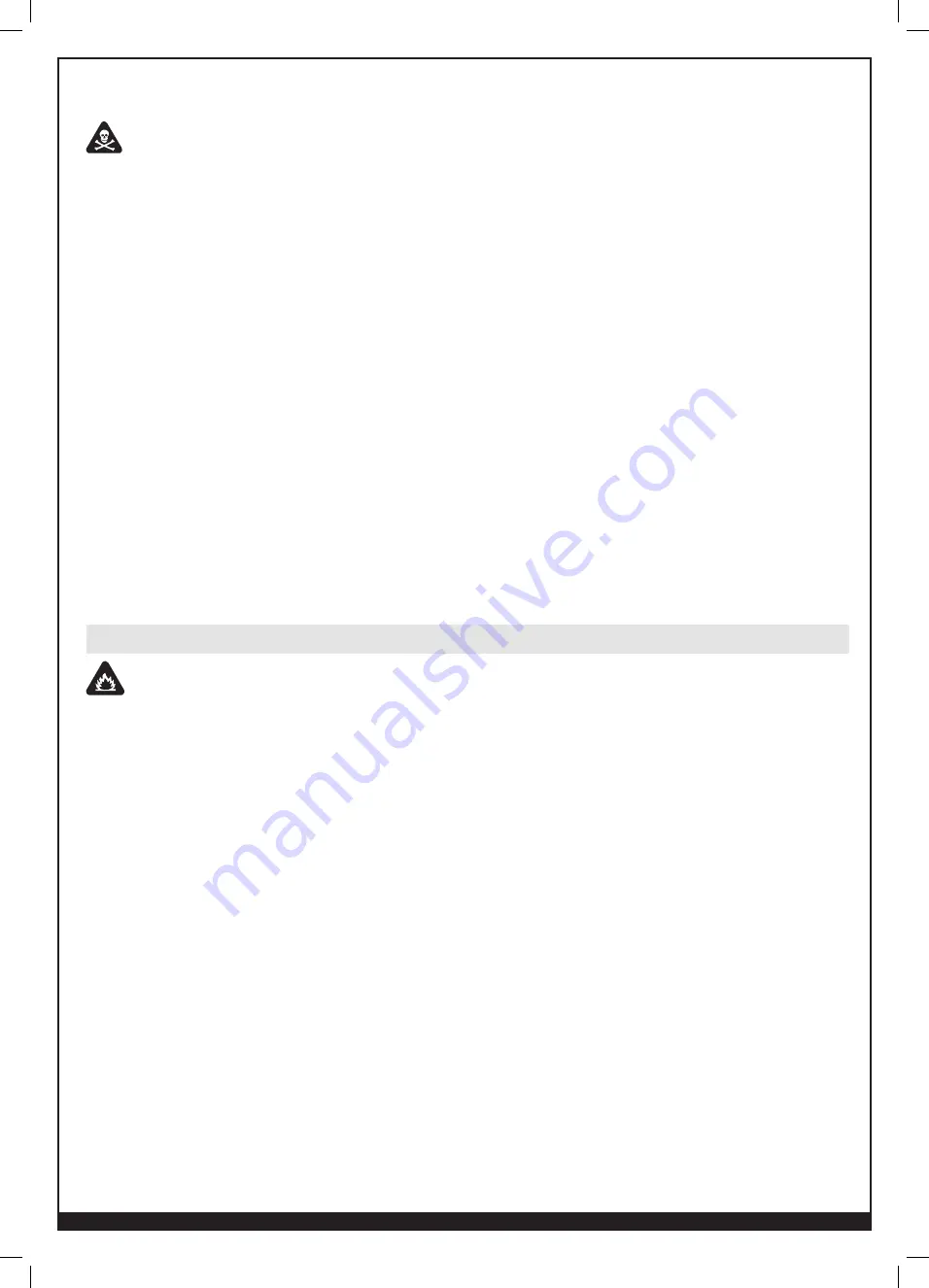
7
WWW.FORNEYIND.COM
• Flying sparks can injure. Wear proper safety equipment to protect eyes and face. Shape tungsten electrode on
grinder wearing proper protection and in a safe location. Keep flammables away and prevent fire from flying
sparks.
FUMES, GASSES, AND VAPORS CAN CAUSE DISCOMFORT, ILLNESS, AND
DEATH!
To reduce the risk, read, understand, and follow the safety instructions. In addition, make certain that
anyone else that uses this welding equipment or is a bystander in the welding area, understands and follows these
safety instructions as well.
• Read and understand manufacturers Safety Data Sheets (SDS) and Material Safety Data Sheets (MSDS).
• Do not weld in an area until it is checked for adequate ventilation as described in ANSI standard Z49.1. If
ventilation is not adequate to exchange all fumes and gasses generated during the welding process with fresh
air, do not weld unless you (the welder) and all bystanders are wearing air-supplied respirators.
• Do not heat metals coated with, or that contain, materials that produce toxic fumes (such as galvanized steel),
unless the coating is removed. Make certain the area is well ventilated, and the operator and all bystanders are
wearing air-supplied respirators.
• Do not weld, cut or heat lead, zinc, cadmium, mercury, beryllium, antimony, cobalt, manganese, selenium,
arsenic, copper, silver, barium, chromium, vanadium, nickel, or similar metals without seeking professional
advice and inspection of the ventilation of the welding area. These metals produce extremely toxic fumes which
can cause discomfort, illness and death.
• Do not weld or cut in areas that are near chlorinated solvents. Vapors from chlorinated hydrocarbons, such
as trichloroethylene and perchloroethylene, can be decomposed by the heat of an electric arc or its ultraviolet
radiation. These actions can cause phosgene, a highly toxic gas to form, along with other lung and eye-
irritating gasses. Do not weld or cut where these solvent vapors can be drawn into the work area or where the
ultraviolet radiation can penetrate to areas containing even very small amounts of these vapors.
• Do not weld in a confined area unless it is being ventilated or the operator (and anyone else in the area) is
wearing an air-supplied respirator.
• Stop welding if you develop momentary eye, nose, or throat irritation as this indicates inadequate ventilation.
Stop work and take necessary steps to improve ventilation in the welding area. Do not resume welding if
physical discomfort persists.
Fire Prevention
FIRE OR EXPLOSION CAN CAUSE DEATH, INJURY, AND PROPERTY DAMAGE!
To reduce these risks, read, understand and follow the safety instructions. In addition, make certain that anyone
else that uses this welding equipment, or is a bystander in the welding area, understands and follows these safety
instructions as well. Remember: arc welding by nature produces sparks, hot spatter, molten metal drops, hot slag
and hot metal parts that can start fires, burn skin and damage eyes.
• Do not wear gloves or other clothing that contains oil, grease, or other flammable substances.
• Do not wear flammable hair preparations.
• Do not touch the hot weld bead or weld puddle until fully cooled.
• Do not weld in an area until it is checked and cleared of combustible and/or flammable materials. Be aware
that sparks and slag can fly 35 feet and can pass through small cracks and openings. If work and combustibles
cannot be separated by a minimum of 35 feet, protect against ignition with suitable, snug-fitting, fire resistant,
covers or shields.
• Do not weld on walls until checking for and removing combustibles touching the other side of the walls.
• Connect the ground cable to the workpiece as close as possible to the welding area. Do not connect ground
cables to building framing or other locations away from the welding area. This increases the possibility of
welding current passing through alternate circuits, creating fire hazards and other safety hazards.
• Do not weld, cut, or perform other such work on used barrels, drums, tanks, or other containers that had a
flammable or toxic substance. The techniques for removing flammable substance and vapors, to make a used
container safe for welding or cutting, are quite complex and require special education and training.
• Do not strike an arc on a compressed gas or air cylinder, and never allow any electrically “hot” parts to touch a
cylinder. Doing so will create a brittle area that can result in a violent rupture immediately or at a later time as a
result of rough handling.
• Ensure any compressed gas cylinders in the work area have properly operating regulators rated for the gas
and pressure used. All hoses, fittings, etc. should be in good condition.
• Do not stand in front of or put your head or face in front of a cylinder valve outlet when opening the valve.
• If a cylinder is not in use or connected for use, keep a valve protection cap in place to protect the valve.
• Keep cylinders upright and securely chain them to a fixed support to prevent tipping.