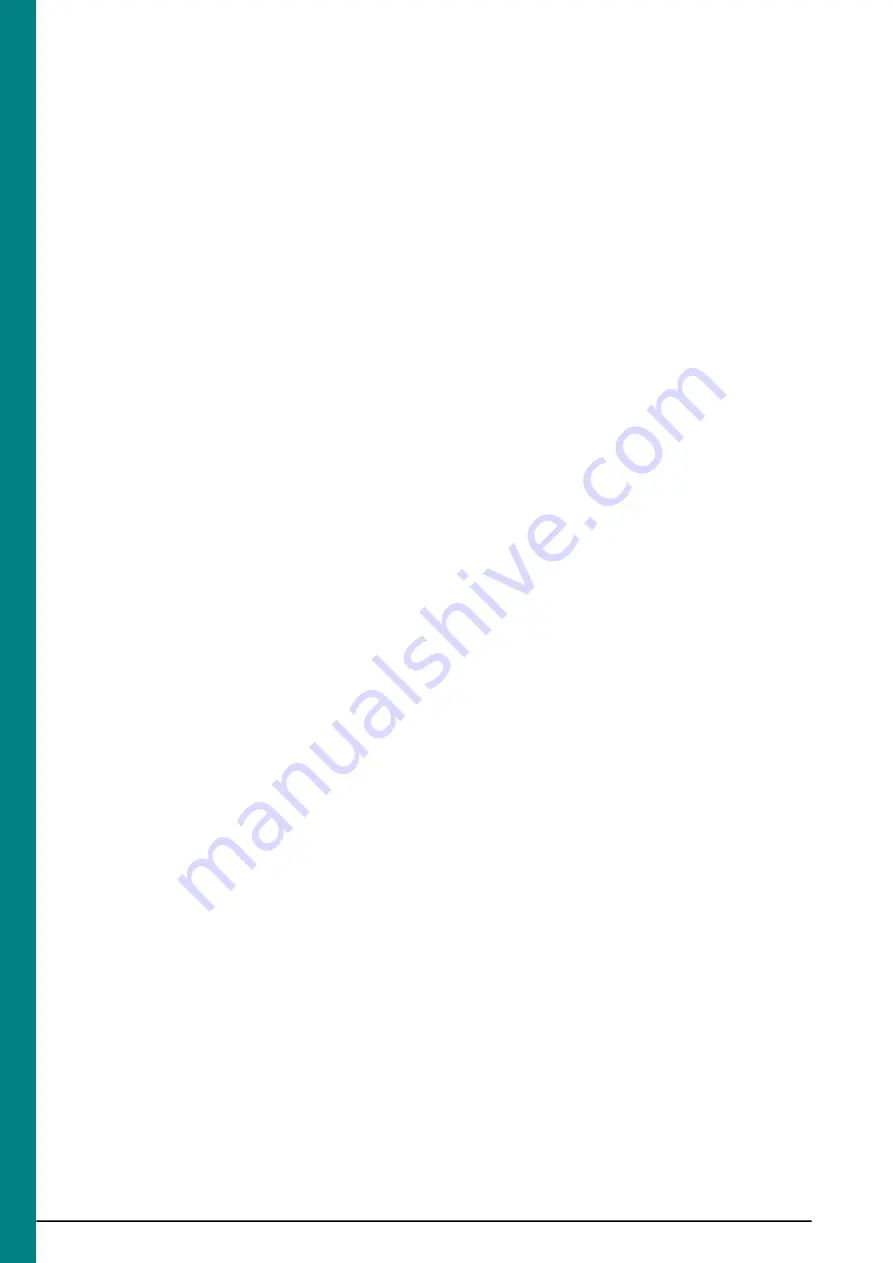
4.8.2 Engine RPM (Revs per Minute)
Speed Controller (A003)
System Overview
This feature enables the engine in the vehicle to
be run at elevated RPM speeds. The power from
the engine can then be used to drive ancillary
equipment. The ancillary equipment may be
powered via a Front End Accessory Drive (FEAD)
layout (in a similar fashion to the air conditioning
compressor).
The maximum power that is available for front end
accessory drive applications at any engine speed
is 6kW (in lieu of the 26Nm air conditioning
compressor). For additional information please
contact the Vehicle Converters Advisory Service,
[email protected]
The converter should consider any increased
engine cooling requirements due to the conversion
and running the vehicles engine under load for
extended periods while the vehicle is stationary.
3 Modes of Operation
There are 3 principle modes in which this feature
can operate, they are:
1.
3 Speed Mode
this provides the end user a
choice of up to 3 preset RPM values of 1100,
1600 and 2030rpm to select from. The end user
cannot easily override these values so there is
minimal risk of damage to ancillary equipment
due to it being run at speeds it was not designed
for. Very limited vehicle speed is allowable while
in this mode (up to 2.5mph approx)
2.
Variable Speed Mode
this provides the end
user with RPM speed ramp up and down
buttons. The end user is free to select RPM
values between 1300-3000rpm in 25rpm steps.
A single press results in a 25 rpm jump. If a ramp
button is held depressed by the end user then
the rate of change is 250rpm/sec. Very limited
vehicle speed is allowable while in this mode
(up to 2.5mph approx).
3.
Idle Up Speed
this mode allows the engines
normal idle to be increased (in 25 rpm steps)
in the range 900-1200rpm. There is not a
vehicle speed restriction in this mode as the
intended use is to raise the engine idle to reduce
the likelihood of engine stall when ancillary
equipment is being run from the engine during
normal drive operations. For example:
Refrigerator units used to keep the cargo bay
cool.
System Availability
This feature is built into the latest Powertrain
Control Module (PCM) software on all diesel
engine variants.
By default the feature is not enabled unless the
vehicle is specifically ordered with the feature from
the factory.
Vehicles which have not been ordered with this
feature, may have the feature enabled at a dealer
via the Integrated Diagnostic System (IDS) on
vehicles built before 2016.75MY or the Ford
Diagnostic Repair System (FDRS) on vehicles built
after 2016.75MY. There is a dealer charge for this
service.
Vehicles fitted with Start-Stop technology may
be converted to RPM speed control, however, the
customer should turn Start-Stop off prior to
starting RPM speed control. For more information
refer to 'Impacts from Start-Stop System' in this
section.
How to control this feature
A loop of wire (green/white) is provided in the
main electrical harness to permit control of the
RPM Speed Control software. Cutting this loop
will provide two wires to connect a control box to
the PCM.
The control box needs to switch resistors into the
circuit across the two green/white wires which
formed the loop prior to being cut. This sort of
circuit is known as a resistance ladder, see figure
E88295. The PCM software monitors the
green/white wire circuit and when certain
resistance's are detected they are interpreted as
various inputs which control the feature. The
switch box can be located where it is ideally
required for the vehicle conversion in question,
rather than having to be mounted on the
Instrument Panel (IP). If the converter chooses to
locate the switch box in a location which is subject
to an adverse environment then the converter
should design the switch box to withstand with
these conditions.
FORD
TRANSIT
2016.75
Date of Publication: 03/2018
EU
4 El
ec
tric
al
150