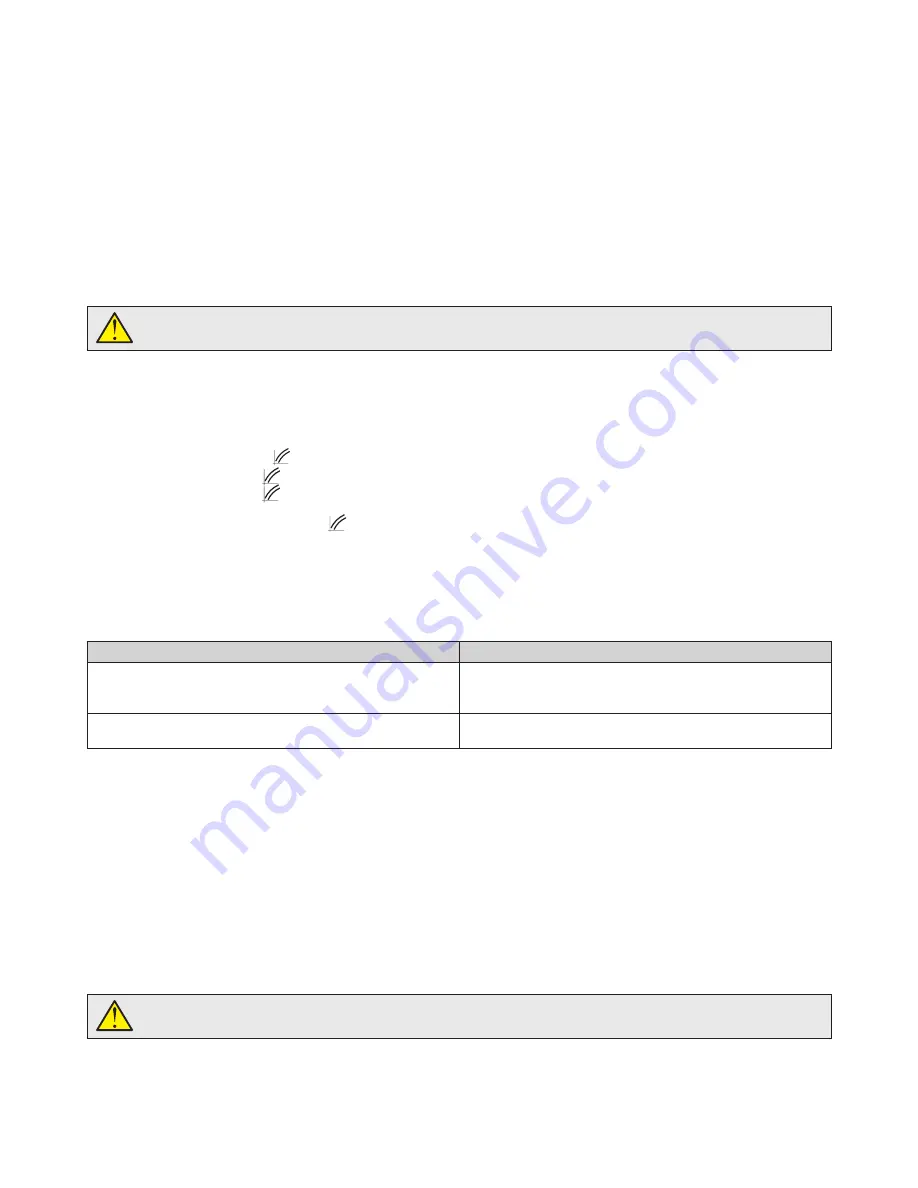
29
3.2.10. Power mains connection
The boiler is supplied with a three-pole power cable, already connected to the electronic board and protected by a cable clamp.
The boiler must be connected to a 230 V ~ 50 Hz mains supply.
When connecting the boiler to the power mains, keep to the phase/neutral system.
Installation must be carried out in compliance with the applicable standards, which are considered an integral part of this manual.
An easily accessible two-pole switch must be installed outside the boiler. The minimum distance between contacts must be 3 mm. The switch
must allow the power supply to be switched off, so that maintenance and servicing can be performed in complete safety.
The power supply to the boiler must be fitted with a differential magnetothermal switch with an appropriate shutdown capacity.
The power supply must be adequately earthed.
This fundamental safety measure must be verified. If in doubt, ask a qualified electrician to check the system thoroughly.
The manufacturer declines all liability for damage resulting from failure to earth the system properly.
Gas, water and CH pipes are NOT suitable for earthing a power network.
3.2.11. Selecting central heating output range
CH water temperature adjusting choice depends on selected operation range:
- standard range: from 20°C to 78°C (from full counter-clockwise position to full clockwise position);
- reduced range: from 20°C to 45°C (from full counter-clockwise position to full clockwise position).
Act on thermoregulation trimmer (
in fig. 21) in order to choose the operation range, as per the following instruction:
- standard range: turn trimmer
fully clockwise;
- reduced range: turn trimmer
fully counter-clockwise.
When the external probe is installed, trimmer
function varies (see subsection 3.2.14.).
Central heating output range selection also alters the waiting time between ignition sequences (thus preventing frequent ignition and
switching off of the boiler), when in CH mode.
- standard range: 4 minutes;
- reduced range: 2 minutes.
Should water temperature in the system fall below a determined value (table 8), waiting time procedure is aborted and the boiler re-ignited.
Selected range
Re-ignition temperature
Standard range
Set-point > 55 °C
Set-point ≤ 55 °C
< 40 °C
Tset-point - Tflow > 15 °C
Reduced range
Regardless of set-point
< 20 °C
Table 8
Operation range selection is to be implemented by a fitter or an authorized Service Centre.
3.2.12. Connection to the room thermostat (optional)
The boiler can be connected to a room thermostat (not supplied with the boiler).
The contacts must be properly sized in relation to a 5 mA 24 VDC load.
The wires must be connected to terminal M9 on the circuit board (fig. 23), after removing the jumper supplied standard with the boiler.
Room thermostat wires must NOT be grouped together with the power supply cables.
3.2.13. Connection to an OpenTherm remote control (optional)
The boiler can be connected to an OpenTherm remote control (optional).
The remote control must be installed by a suitably qualified person.
Only original remote controls supplied by the manufacturer must be used.
If non-original remote controls are used, correct operation of the boiler cannot be guaranteed.
For installation instructions, refer to the booklet accompanying the remote control.