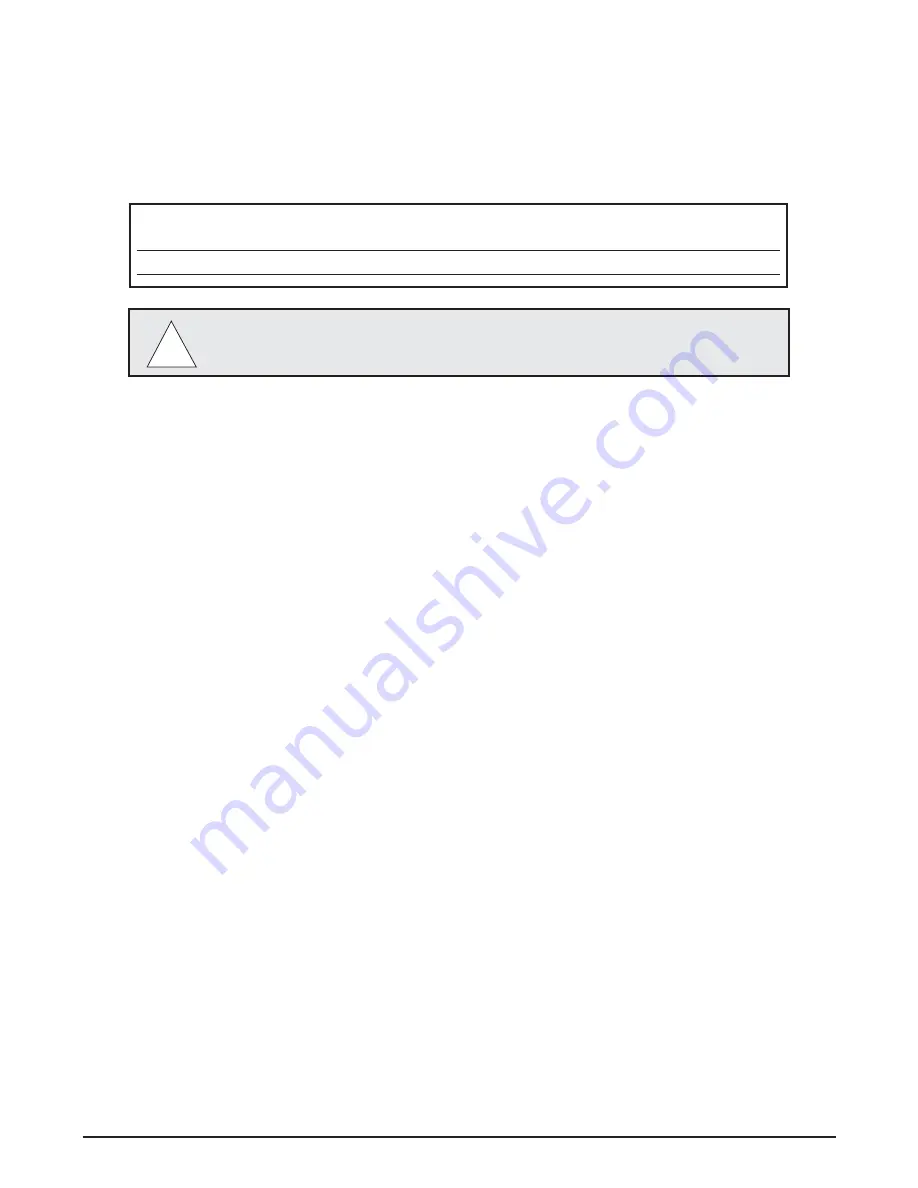
24
12CI400A • 12HI400A
Refrigerant replacement requirements
1. Non-contaminated refrigerant removed from any Follett refrigeration system can be recycled and
returned to the same system after completing repairs. Recycled refrigerant must be stored in a clean,
approved storage container. If additional refrigerant is required, virgin or reclaimed refrigerant that
meets ARI standard 700-88 must be used.
2. In the event of system contamination (for example, a compressor burn out, refrigerant leak, presence
of non-condensibles or moisture), the system must be repaired, evacuated and recharged using virgin
or reclaimed refrigerant that meets ARI standard 700-88.
3. Follett Corporation does not approve of recovered refrigerants. Improper refrigeration servicing
procedures will void the factory warranty.
Evacuation
Evacuate the system to a level of 500 microns. When the 500 micron level is reached, close valves and both
manifold and shut down the vacuum pump. Allow the system to sit for approximately 20 minutes. During this
period the system pressure should not rise. If the system pressure rises and stabilizes there is moisture in the
system and further evacuation is needed. If the pressure continues to rise check the system for leaks.
Ambients
Minimum Maximum
Air temperature
1
50 F/10 C
100 F/37.8 C
Water temperature
2
40 F/4.4 C
90 F/32.2 C
1
Ambient air temperature is measured at the air-cooled condenser coil inlet.
2
Ambient water temperature is measured in the ice machine float reservoir.
R400 ice machine charge specifications
Model
Charge
Refrigerant type
12CI400A, 12HI400A (air-cooled) 19 oz
R404A
Recharging of unit at other than factory specifications will void ice machine
warranty.
!
Refrigeration system
Important: All service on refrigeration system must be performed in accordance with all federal, state and
local laws that pertain to the use of refrigerants. It is the responsibility of the technician to ensure that these
requirements are met.