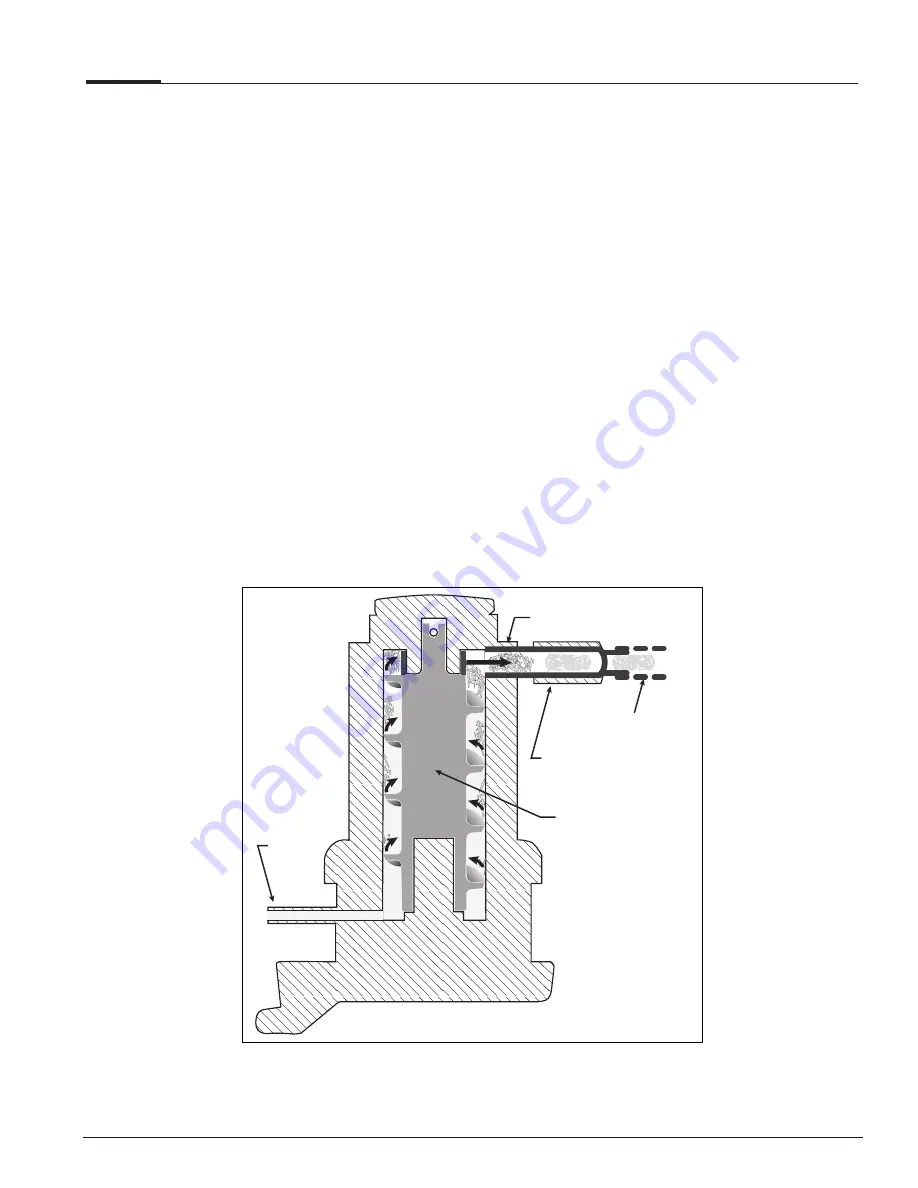
25CI425A/W, 25HI425A, 50CI425A/W, 50HI425A
15
Service
Ice machine Operation (all models)
Follett’s ice machine consists of four distinct functional systems:
§
Harvesting system
§
Water system
§
Electrical control system
§
Refrigeration system
These four systems work together to accomplish the production and harvesting of ice . A problem in any one of
these systems will result in improper operation of the entire ice production cycle . When troubleshooting the ice
machine, it is important to analyze the entire system operation to determine which system is not functioning
properly, then pinpoint the component within that system that is malfunctioning . Determine what corrective action
must be taken before making any adjustments or replacing any components .
The icemaking process
The Maestro Plus ice machine uses a stainless steel jacketed evaporator and operates on a continuous freezing
cycle . Water is supplied to the evaporator from the water reservoir where the water level is controlled by conductivity
probes .
When the ice machine is running, a layer of ice forms on the interior surface of the evaporator . This ice is
continuously removed by a slowly rotating (12 RPM) auger . The auger carries the ice upward into the cavity
formed by the top bearing housing and the compression loop, where it is compressed to remove excess water .
When the ice reaches the desired hardness it rotates within the cavity and is forced through a discharge port
and compression nozzle and into the ice transport tube . The discharge tube and compression nozzle are slightly
restricted to further compress the ice and produce the desired hardness .
A solid state control board located in the electrical box of the ice machine controls the normal operation of the ice
machine and monitors gearmotor torque . This control board will shut down the ice machine should an over-torque
condition occur . It is very important that you familiarize yourself with the operational sequences detailed in this
manual before attempting to service the ice machine .
water
inlet
auger
compression nozzle
ice transport tube
evaporator
port