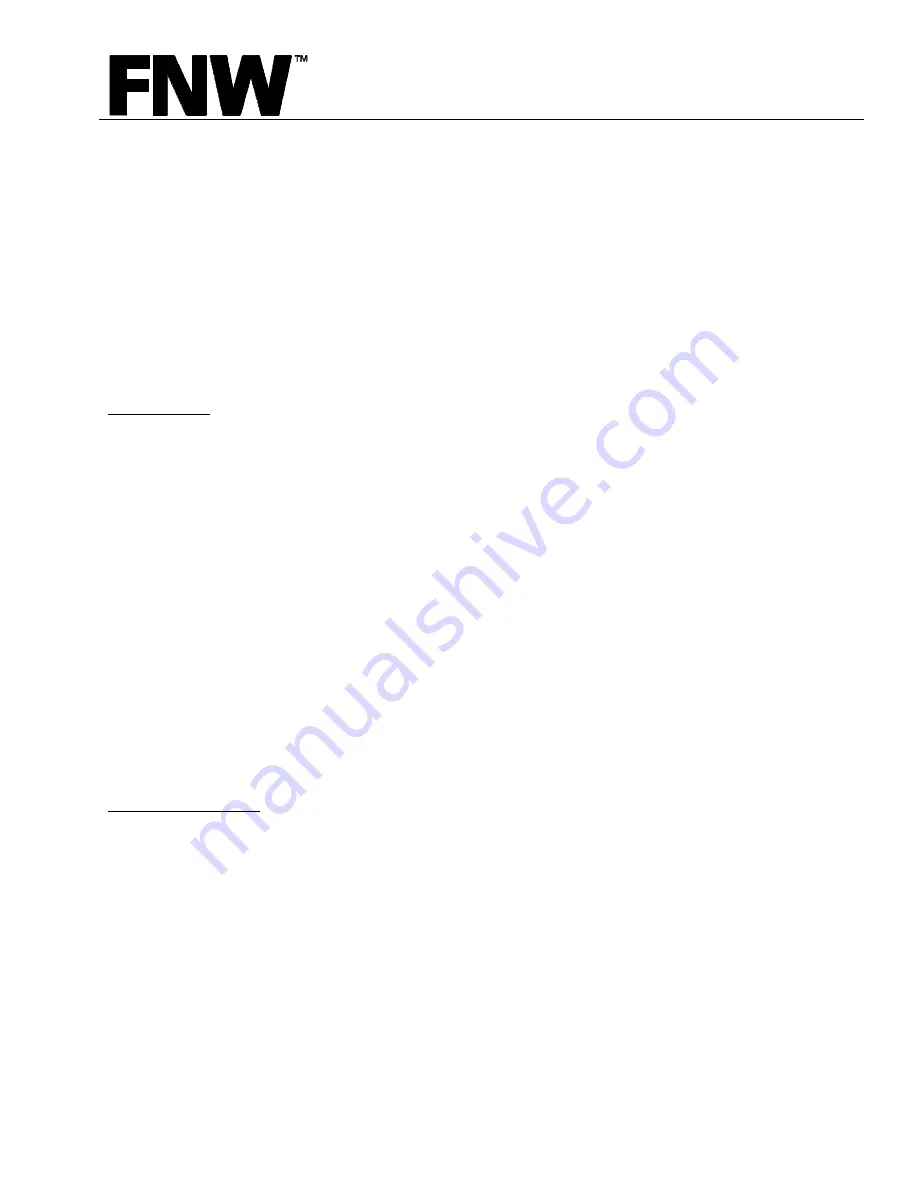
INSTALLATION, OPERATION & MAINTENANCE INSTRUCTIONS
3-Piece Threaded, Socket, Tube & Clamp End Ball Valves
DOC: IOM_FNW3PCBV_ ver_12-2007
Page 2 of 6
9.
The valve should be installed in the open position.
10. Valves vary in size, temperature capacity chemical resistance, and pressure capacity. Make sure the valve is
adequate for the application.
11. Standard valves are bi-directional and can be installed in either flow direction.
12. To provide optimum service, the valve should be operated only in the fully open or fully closed position (on/off
service). Throttling service is not recommended.
13. Use only FNW recommended spare parts for maintenance.
14. To ensure safety and to maintain warranty, never modify the valve in any way without prior approval from
FNW.
Threaded Ends
1.
Check the valve’s threads and the threads of the connecting parts for compatibility.
2.
It is not necessary to disassemble threaded end valves prior to installation.
3.
Unless otherwise specified, pipe threads are American National Standard Taper Pipe Threads (NPT) per
ANSI B1.20.1. This standard requires that a pipe sealant be used. Use an anti-seize thread sealant to seal
and prevent galling. Use pipe sealants compatible with valve materials and process fluid. The correct
lubricating sealant used on stainless steel pipe threads is especially important to prevent galling.
4.
Do not use excessive amounts of pipe sealant. An excess of pipe sealant can obstruct the pipe or valve or
otherwise hinder the operation of the valve.
5.
To prevent distortion or damage to the valve, do not apply torque through the valve. When tightening the
valve, always use a wrench on the end nearest the pipe being tightened. It is preferred that the pipe be
screwed into the valve, holding the valve stationary at the end being connected.
6.
Do not over tighten tapered thread ends.
7.
Test the operation of the valve, checking for binding or misalignment. Always leak test the system before
using.
Socket and Tube Ends
1.
Check fit of pipe to socket end or tube end to pipe prior to welding. Clean and de-burr as needed.
2.
With the valve in the open position, tack weld both ends in four equally spaced spots.
3.
Loosen all body nuts and remove the body bolts, supporting the body assembly in the process. Carefully lift
out the body assembly and make sure no seats or seals remain on the end caps.
4.
Complete the welding of the end caps.
Make sure the end caps do not shift during welding.
Allow
appropriate time for the welds to cool, and then clean the end caps.
5.
Carefully reinsert the body assembly making sure seats and seals are properly located. While supporting the
body assembly, reinstall the body bolts and nuts and hand tighten.
6.
Tighten all body bolts according to the information presented in the maintenance section (Table 1).