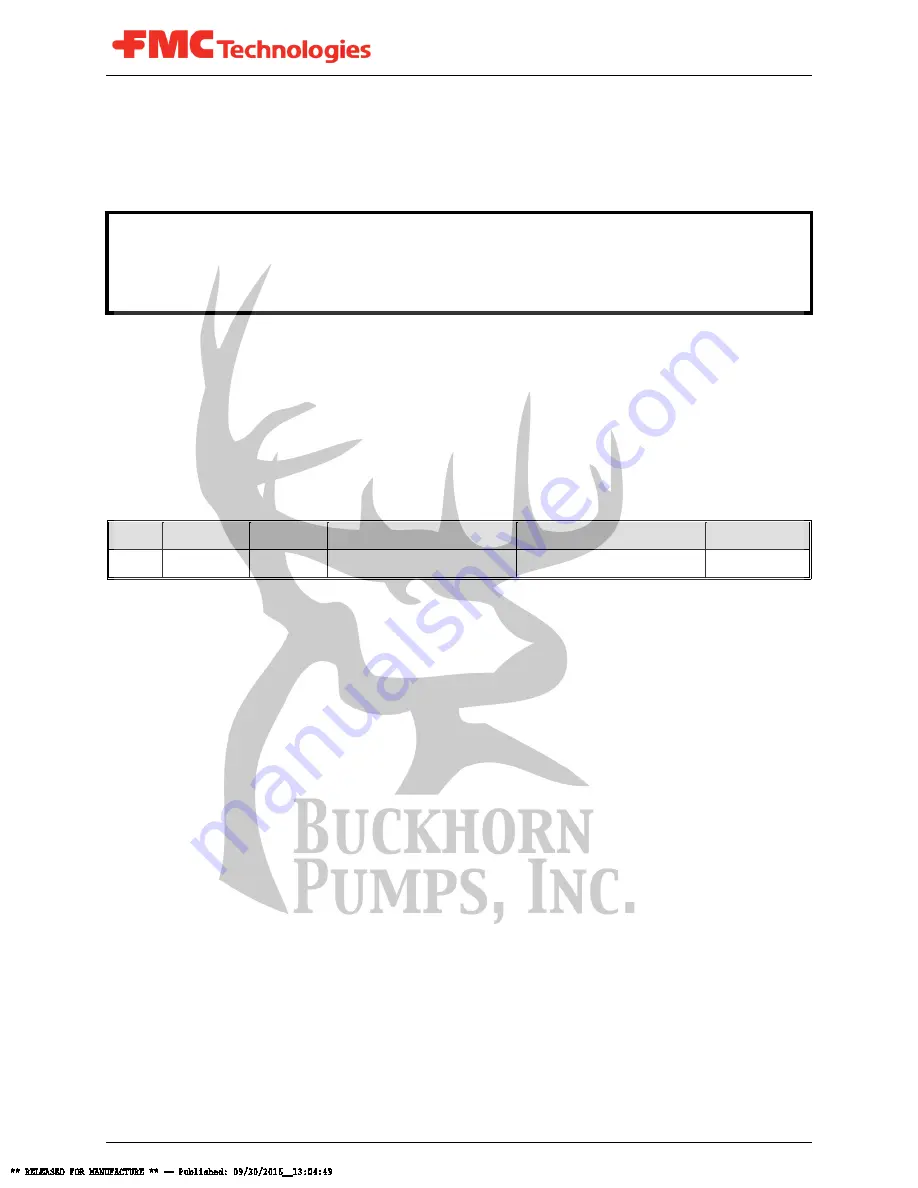
Doc No: OMM50002312
Rev: C Page 1 of 54
Subject to contractual terms and conditions to the contrary, this document and all the information contained herein are the confidential and exclusive
property of FMC Technologies, and may not be reproduced, disclosed, or made public in any manner prior to express written authorization by FMCTI.
OPERATION AND MAINTENANCE MANUAL, W11 TRIPLEX PUMPS
Rev
ECN No.
Date
Reviewed By
Approved By
Status
C
5041126
30-SEP-2016
Rothe, Michael
Kowalski, Christopher
RELEASED
Summary:
This is a manual for FMC W11 triplex piston pumps. These pumps include a pinion drive
for internal gear reduction; they have a stroke length of 2.75 inches, and maximum
continuous duty power ratings ranging from 20 horsepower (15 kilowatts) for the W1118
to 30 horsepower (22 kilowatts) for the W1122. The maximum intermittent duty rating is
24 horsepower (18 kilowatts) for the W1118 to 36 horsepower (27 kilowatts) for the
W1122. Refer to part number