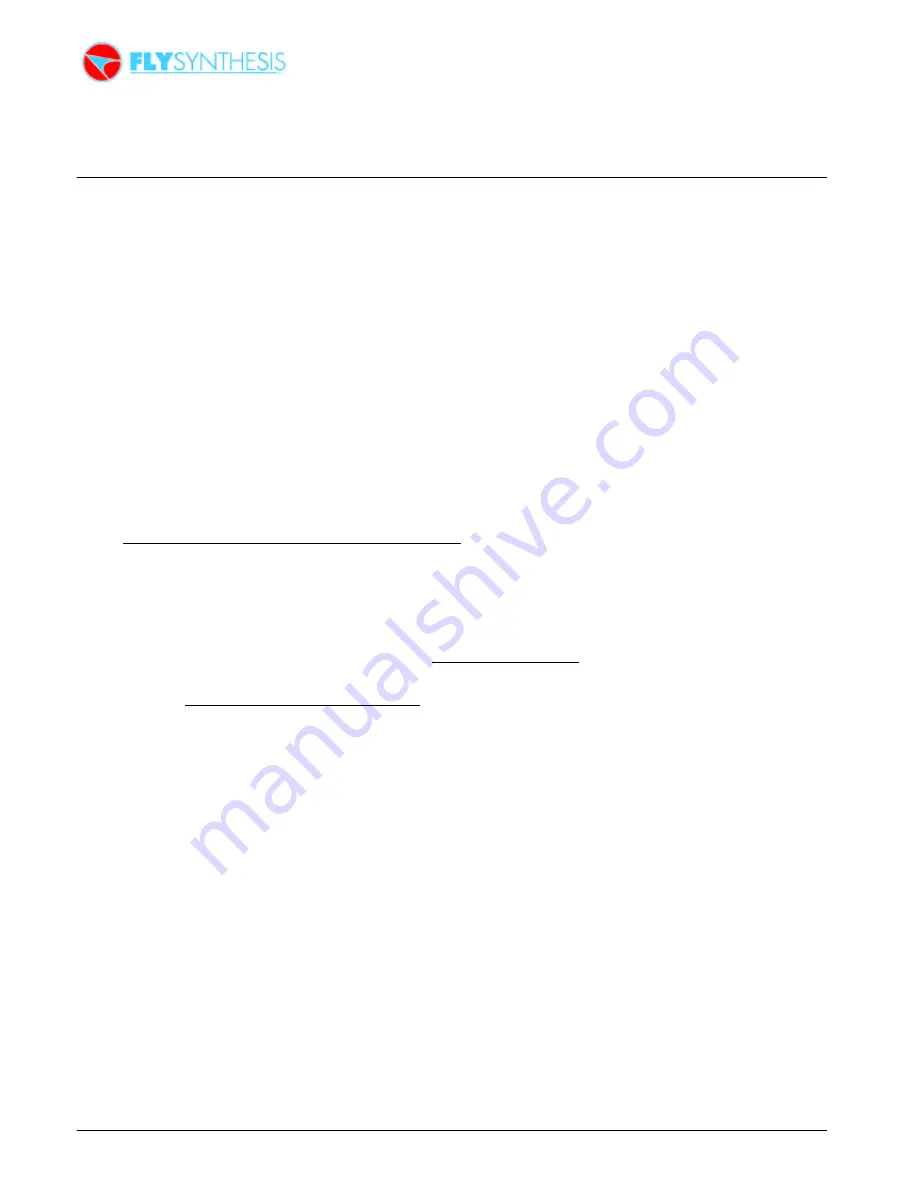
AQ 002 Rev.00 Issued/Verify/Approval M. Garofolo 13/july/02
Identification: MM 002 Rev 01
Page: 13 of 26
Date: 20/april/2005
Issued: M. Fiorindo
Verify: R.Ciotti
Approval: R. Ciotti
Revisions description:
Updated manual
Storch CL, HS, S
Maintenance Manual
(for Rotax 912 UL/S, 914 UL and
Jabiru 2200 version)
1.8 100-HOURS INSPECTION
(1)
Ensure that the ignition key is REMOVED.
(2)
Ref. I.P.C. Fig. 6: replace the 6 ea. Exhaust system-retaining springs (28).
(3)
Ref. I.P.C. Fig. 6: replace the 3 ea. Muffler buffers
(4)
Ref. I.P.C. Fig. 8: replace the fuel filter (7) cartridge.
(5)
Ref. I. P.C. Fig. 6: inspect the carburettor air r filter cartridge (7) for damage and clogging.
Replace if necessary or carefully clean the same.
(6)
If the aircraft normally operates in very dusty environment, an accurate inspection to piston and
cylinders is required.
To accomplish this inspection the cylinders and pistons removal is requested.
Under normal environment conditions this check should be performed during the 150-hours
inspection.
For what above-mentioned the relevant operations are listed in the relative paragraph.
(7)
Remove the fuel pump and clean it inside.
Check the
pump
for general conditions.
For engines equipped with drive reduction gearbox:
(8)
Replace the gearbox, lubrication oil.
The oil replacement is also required after 2 years from last filling. Apply whichever occurs
first.
For relevant procedure, refer to the engine Operator's Manual - last issue.
(9)
Check and adjust the preload of "knuckle -joint" spring washers (applicable to gearboxes type A-B).
The adjustment should be performed by qualified personnel only (see ROTAX Service Bulletin
6UL86/E dated Dec. 1986).
(10)
For ROTAX -582 UL engines only: replace the rotary valve gear 1Librication oil. For relevant
procedure refer to engine Operator's Manual - last issue.
(11)
Ref. I.P.C. Fig. 6: using a 10X magnifying glass Carefully inspect all welding relevant to, engine
housing
(4) and engine mount (11) for cracks.
(12)
Check tightening of self-locking nuts securing the seat belts (I.P.C. Fig.2, items 10 - 14 and Fig. 5
item 11).
(13)
Remove the main landing gear wheels and check the brake linings for wear.
Lubricate the brake operating levers (see paragraph 4.2.10 - LUBRICATION).
(14)
Control handles in the cabin: disconnect all control cables and check for wear and broken wires;
check terminals for security.
Replace cables if necessary.
(15)
Control handles in the cabin: carefully inspect
all
handles for cleanliness, damage, wear (abnormal
play) and security of attachment.
(16)
Support the fuselage and remove the landing gear legs (2 ea.).
Check each leg for linearity.
Distortion allowed: 10 mm MAX (.40 in MAX) measured on one end.
Check if there are flaws with a magnifying glass. If found replace legs.
Clean the housing of legs and legs and put new graphite grease.