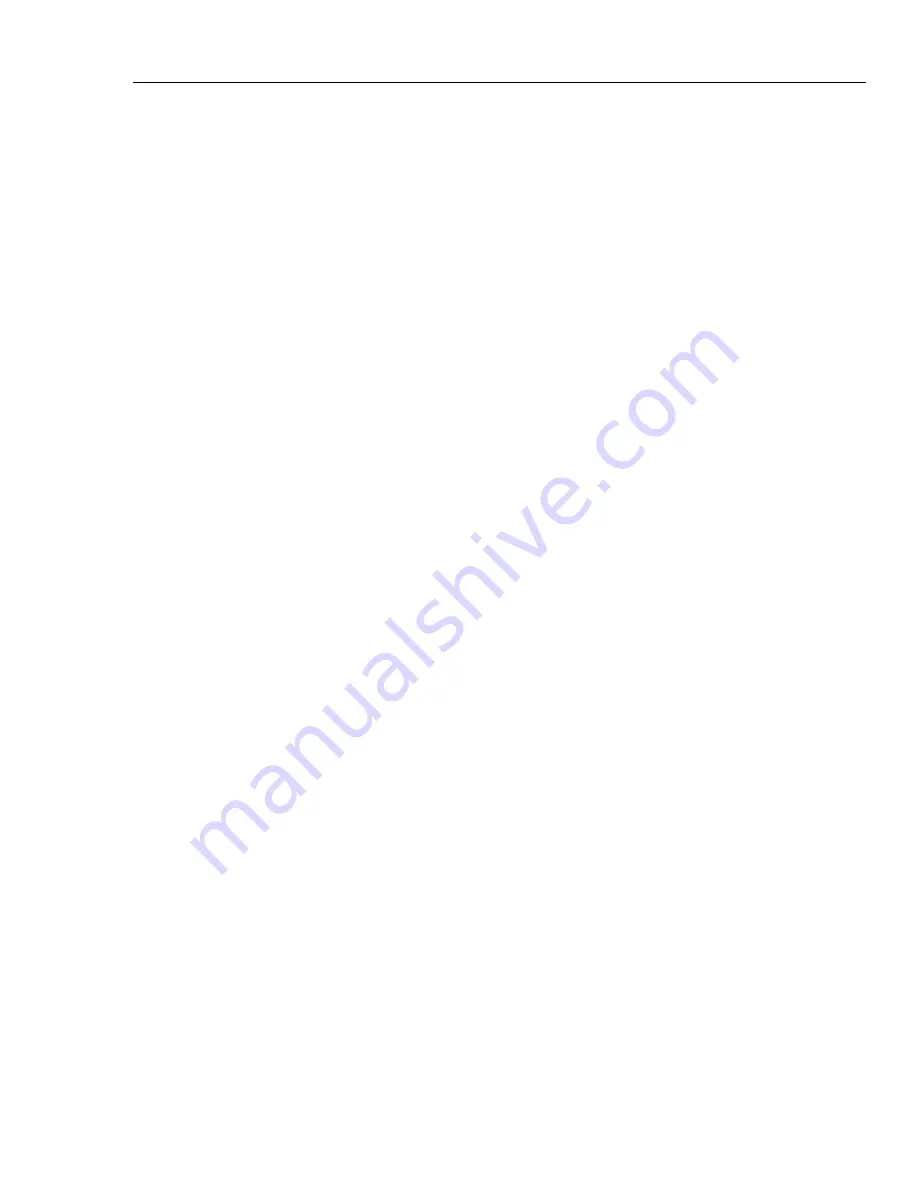
Maintenance
Replacement
4
4-3
W
Caution
Never touch the working surface of a clean piston with bare
fingers — the natural oil in your skin can cause the piston and
cylinder to stick.
5.
Wipe excess fluid from the outside surfaces of the cylinder.
6.
Roll a NEW tissue into a tapered rod of appropriate size. Force the tissue through the
cylinder bore whilst rotating. Ensure that the tissue is a tight fit inside the bore so that
dirt and contamination is removed.
7.
Repeat the above step, using a NEW tissue, but from the opposite end of the cylinder.
8.
Immerse the cylinder in a suitable, clean solvent, then, using NEW tissues, repeat the
cleaning procedure with the tapered tissue rolls.
Replacement
1.
Ensure that the O Ring is clean and undamaged, and that it is fitted correctly in the
top of the PCU Column.
2.
Place cylinder on top of the PCU Column, with the reduced diameter at the top,
secure with Piston Nut A.
3.
Hold the Piston by the larger “head” end, and dip the smaller “working” end into a
container of CLEAN operating fluid. Transfer this to the top of Piston Nut A, and
allow a few drops of the fluid to run through the bearing assembly and through the
bore of the Cylinder. Repeat this 3 or 4 times to ensure a good film of fluid in the
Cylinder.
4.
CAREFULLY introduce the working end of the piston into the Cylinder — ensuring
that it is held VERTICALLY, and push gently through.
W
Caution
Never force the piston into its cylinder or damage will result.
5.
If resistance is felt, introduce more fluid. If resistance continues, re-clean piston,
cylinder or both. If, after repeated cleaning, the piston still will not slide freely within
the cylinder, then permanent damage may have occurred. In which case, the parts
should be returned to the factory for evaluation or replacement.
6.
Screw Piston Nut B onto Nut A to retain the Piston.
7.
Carefully replace Weight Carrier Tube Assembly, ensuring that the central hole in the
top locates correctly on the top of the Piston.
1.800.561.8187
information@ITM.com
Fluke-Direct
.ca