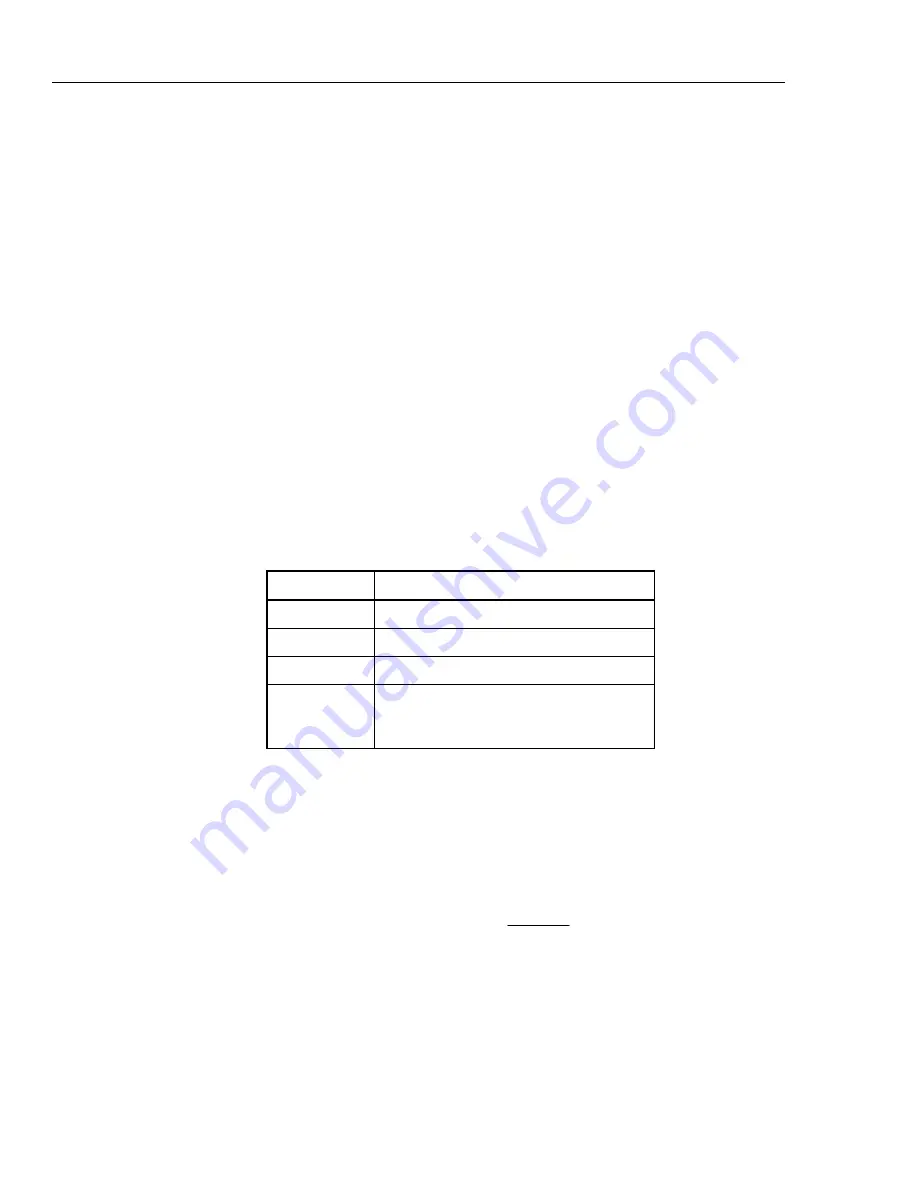
P3000 Series
Users Manual
1-2
Compressed Gas
Use of compressed gas can create an environment of propelled foreign matter. Pressure
system safety precautions apply to all ranges of pressure. Care must be taken during
testing to ensure that all connections are properly and tightly made prior to applying
pressure. Personnel must wear eye protection to prevent injury.
Heavy Weights
Lifting and movement of heavy weights can create an environment of strain and impact
hazards. Care must be taken during testing to ensure that weight masses are lifted in a
manner that avoids over-reaching or twisting, and that the masses are not dropped.
Personnel must wear reinforced safety shoes to prevent injury.
Personal Protective Equipment
Wear eye protection and reinforced safety shoes approved for the materials and tools
being used.
Symbols Used in this Manual
In this manual, a
Warning
identifies conditions and actions that pose a hazard to the user.
A
Caution
identifies conditions and actions that may damage the Pneumatic Deadweight
Tester.
Symbols used on the Pneumatic Deadweight Tester and in this manual are explained in
Table 1-1.
Table 1-1. Symbols
Symbol Description
B
AC (Alternating Current)
J
Earth Ground
W
Important Information: refer to manual
~
Do not dispose of this product as unsorted
municipal waste. Go to Fluke’s website for
recycling information.
Operating Principle
Deadweight Testers are the primary standard for pressure measurement. Utilizing the
well-proven Piston-Gauge system, consisting of a vertically mounted, precision lapped
Piston and Cylinder assembly, accurately calibrated weight masses (Force) are loaded on
the piston (Area), which rises freely within its cylinder. These weights balance the
upward force created by the pressure within the system.
AREA
FORCE
PRESSURE
=
Each weight is marked with the tester serial number, and the pressure measured when
placed on a correctly spinning and floating piston. The total pressure measured is the
summation of the weights plus the piston weight carrier assembly.
Summary of Contents for 4184297
Page 6: ...P3000 Series Users Manual iv...
Page 8: ...P3000 Series Users Manual vi...
Page 16: ...P3000 Series Users Manual...
Page 22: ...P3000 Series Users Manual 2 6...
Page 26: ...P3000 Series Users Manual 3 4...
Page 28: ...P3000 Series Users Manual 4 2...
Page 46: ...P3000 Series Users Manual 7 2...