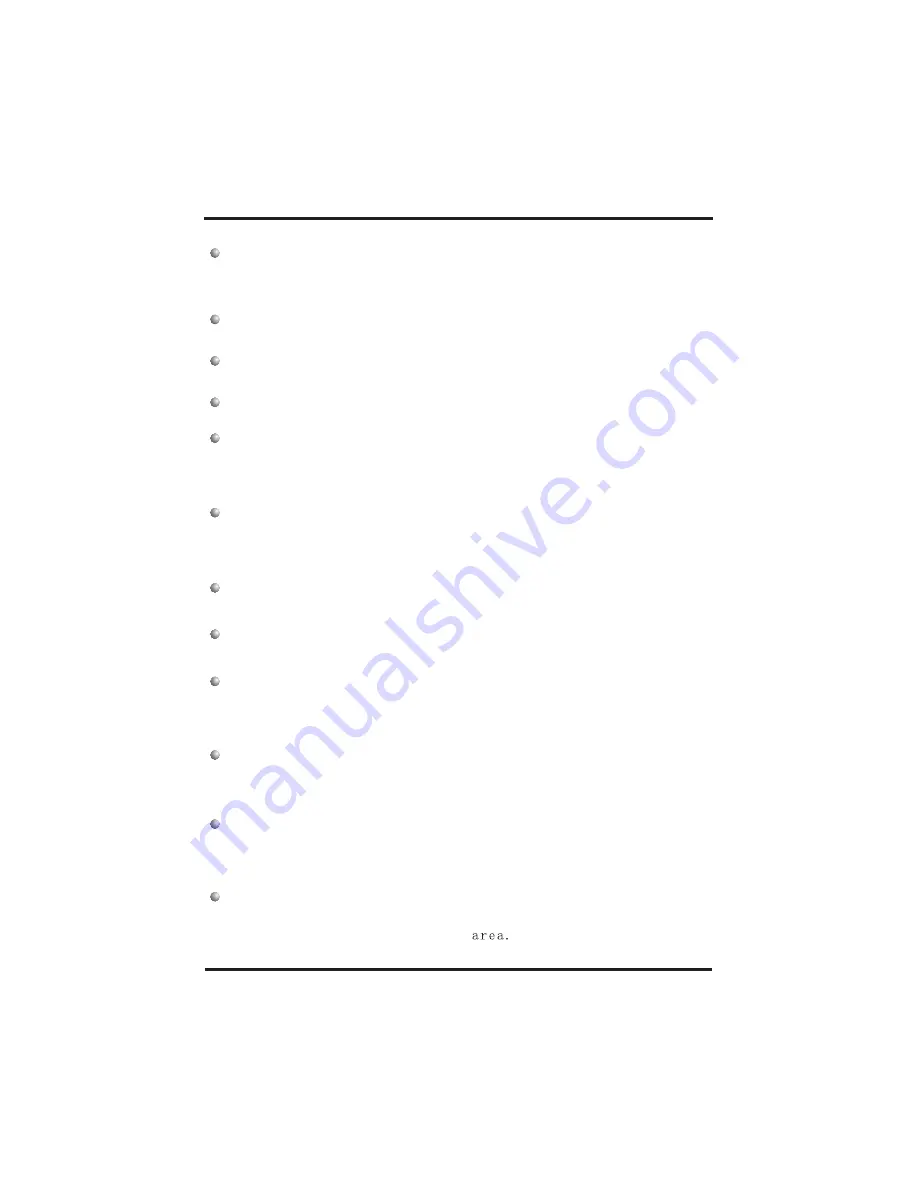
28
Check the water supply device and the release often. You should avoid the condition of no
water or air entering into system, as this will influence unit's performance and reliability.
You should clear the pool/spa filter regularly to avoid damage to the unit as a result of the
dirty of clogged filter.
The area around the unit should be dry, clean and well ventilated. Clean the side heating
exchanger regularly to maintain good heat exchange as conserve energy .
The operation pressure of the refrigerant system should only be serviced by a certified
technician .
Discharge all water in the water pump and water system ,so that freezing of the water in the
pump or water system does not occur. You should discharge the water at the bottom of
water pump if the unit will not be used for an extended period of time. You should check the
unit thoroughly and fill the system with water fully before using it for the first time after a
Check the power supply and cable connection often,.Should the unit begin to operate
abnormally, switch it off and contact the qualified technician.
5. MAINTENANCE AND INSPECTION
Checks to the area
Prior to beginning work on systems containing flammable refrigerants, safety checks are
necessary to ensure that the risk of ignition is minimised. For repair to the refrigerating
system, the following precautions shall be complied with prior to conducting work on the
system. prolonged period of no usage.
Work procedure
Work shall be undertaken under a controlled procedure so as to minimise the risk of a
flammable gas or vapour being present while the work is being performed.
Work procedure
Work shall be undertaken under a controlled procedure so as to minimise the risk of a
flammable gas or vapour being present while the work is being performed.
General work area
All maintenance staff and others working in the local area shall be instructed on the nature
of work being carried out. Work in confined spaces shall be avoided. The area around the
workspace shall be sectioned off. Ensure that the conditions within the area have been
made safe by control of flammable material.
General work area
All maintenance staff and others working in the local area shall be instructed on the nature
of work being carried out. Work in confined spaces shall be avoided. The area around the
workspace shall be sectioned off. Ensure that the conditions within the area have been
made safe by control of flammable material.
Checking for presence of refrigerant
The area shall be checked with an appropriate refrigerant detector prior to and during work,
to ensure the technician is aware of potentially flammable atmospheres. Ensure that the
leak detection equipment being used is suitable for use with flammable refrigerants, i.e.
non-sparking, adequately sealed or intrinsically safe.
Presence of fire extinguisher
If any hot work is to be conducted on the refrigeration equipment or any associated parts,
appropriate fire extinguishing equipment shall be available to hand. Have a dry powder or
CO2 fire extinguisher adjacent to the charging
Summary of Contents for ASTRALPOOL 78566
Page 2: ......
Page 28: ...25 4 OPERATION AND USE Controller interface diagram and definition...
Page 29: ...26 4 OPERATION AND USE Controller interface diagram and definition...
Page 38: ...Note...
Page 39: ......
Page 40: ...Code 83900023...