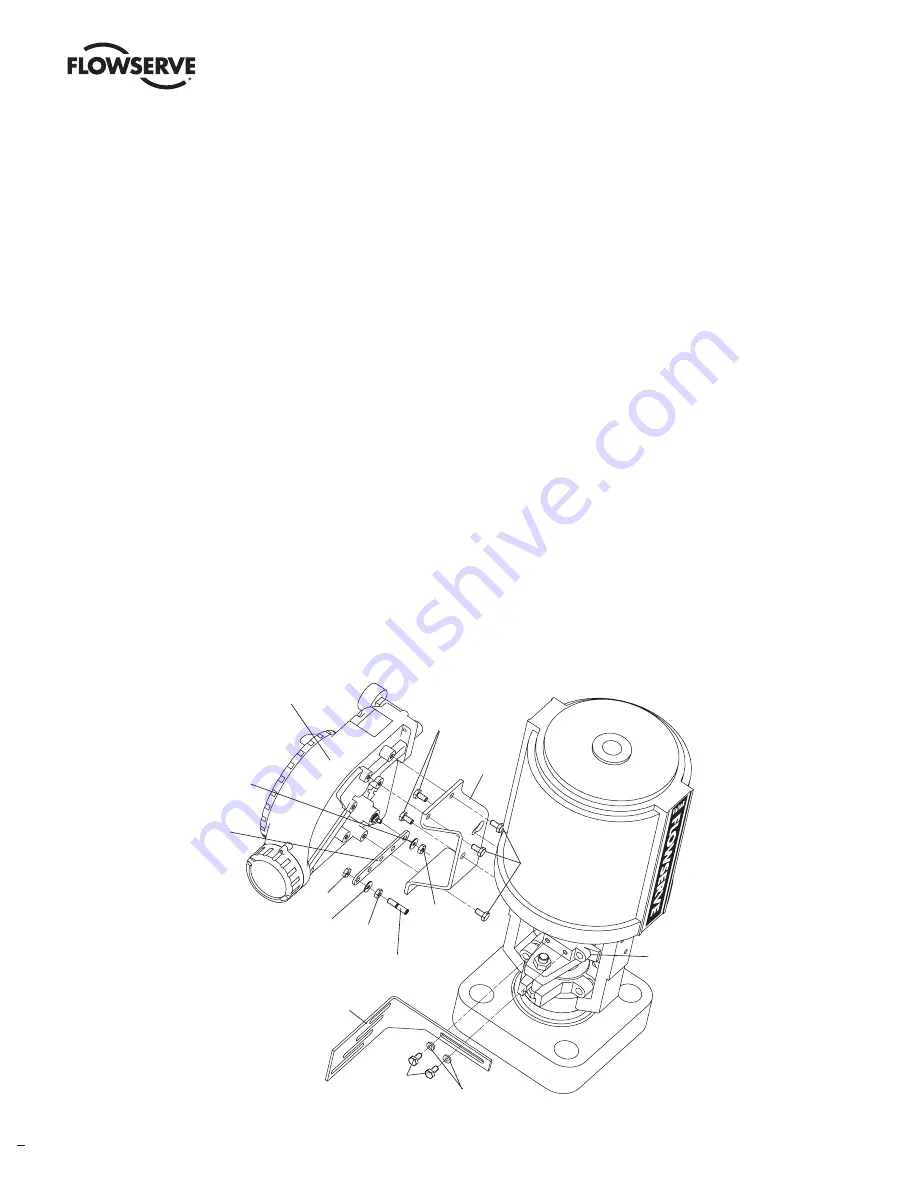
Logix 3400MD Digital Positioner FCD LGENIM3404-00 – 9/09
8
Figure 3: Linear Mark One Control Valve Mounting
Logix 3400
MD
Positioner
Positioner
Bolts
Nut
Lock Washer
Nut
Follower Pin
Take-off Arm
Bolts
Stem Clamp
Bracket
Bolts
Bracket
Locknut
Washer
Follower
Arm
Nut
Metal Washers
4.2 Positioner Operation
The Logix 3400MD
positioner is an electric feedback instrument.
Figure 1 shows a Logix 3400MD
positioner installed on a double-
acting linear actuator for air-to-open action.
The Logix 3400MD
receives power from the two-wire, FF input signal.
This positioner utilizes FF communications for the command signal.
The command source can be accessed with the Rosemount 375
communicator or other host software.
0% is always defined as the valve closed position and 100% is always
defined as the valve open position. During stroke calibration, the
signals corresponding to 0% and 100% are defined.
The input signal in percent passes through a characterization/
limits modifier block. The positioner no longer uses CAMs or other
mechanical means to characterize the output of the positioner. This
function is done in software, which allows for in-the-field customer
adjustment. The positioner has four basic modes:
Linear, Equal Percent
(=%), Quick Open (QO)
and
Custom
characterization. In
Linear
mode,
the input signal is passed straight through to the control algorithm in a
1:1 transfer. In
Equal Percent (=%)
mode, the input signal is mapped to
a standard 30:1 rangeability =% curve. In
Quick Open
the input signal is
mapped to an industry standard quick-open curve. If
Custom
charac-
terization is enabled, the input signal is mapped to either a default =%
output curve or a custom, user-defined 21-point output curve. The
custom user-defined 21-point output curve is defined using a handheld
or the Host configuration tool software. In addition, two user-defined
features,
Soft Limits
and Final Value Cutoff, may affect the final input
signal. The actual command being used to position the stem, after any
characterization or user limits have been evaluated, is called the
Control
Command
.
The Logix 3400MD
uses a two-stage, stem-positioning algorithm. The
two stages consist of an inner-loop, spool control and an outer-loop,
stem position control. Referring again to Figure 1, a stem position
sensor provides a measurement of the stem movement. The
Control
Command
is compared against the
Stem Position
. If any deviation
exists, the control algorithm sends a signal to the inner-loop control to
move the spool up or down, depending upon the deviation. The inner-
loop then quickly adjusts the spool position. The actuator pressures
change and the stem begins to move. The stem movement reduces the
deviation between
Control Command
and
Stem Position
. This process
continues until the deviation goes to zero.
The inner-loop controls the position of the spool valve by means
of a driver module. The driver module consists of a temperature-
compensated hall effect sensor and a piezo valve pressure modulator.
The piezo valve pressure modulator controls the air pressure under a
diaphragm by means of a piezo beam bender. The piezo beam deflects
in response to an applied voltage from the inner-loop electronics. As
the voltage to the piezo valve increases, the piezo beam bends, closing