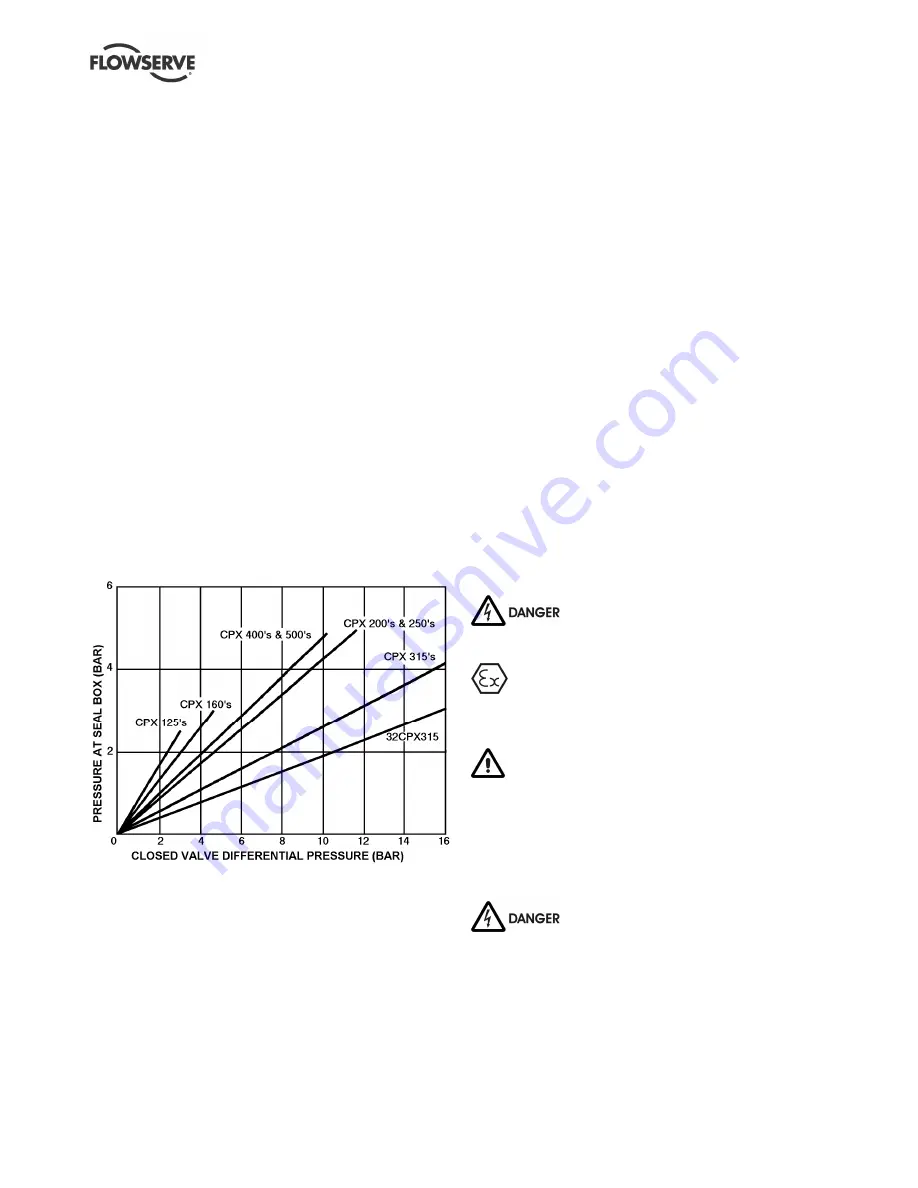
CPX, CPXR, CPXN and CPXP USER INSTRUCTIONS ENGLISH 71569117 02-10
Page 15 of 44
flowserve.com
Flowserve seal connections are designated as follows:
Q
- quench
F
- flush
D
- drain outlet
BI - barrier fluid in (double seals)
BO - barrier fluid out (double seals)
H
- heating jacket
C
- cooling jacket
Covers having an auxiliary quench connection,
require connection to a suitable source of liquid flow,
low pressure steam or static pressure from a header
tank. Recommended pressure is 0.35 bar (5 psi) or
less. Check General arrangement drawing.
Dual seals, both pressurised and unpressurised,
require a barrier liquid between the seals, compatible
with the pumped liquid.
With back-to-back double seals, the barrier liquid
should be at a minimum pressure of 1 bar (14.5 psi)
above the maximum pressure on the pump side of
the inner seal. (See chart.) The barrier liquid
pressure must not exceed limitations of the seal on
the atmospheric side. For toxic service the barrier
liquid supply and discharge must be handled safely
and in line with local legislation.
Notes:
a) Total seal pressure is equal to pressure at seal plus suction
pressure.
b) For pumped liquid viscosities greater than 440 Centistokes
multiply the differential pressure by 1.25 for 125, 160 and 200
size pumps and by 2.0 for larger sizes.
c) Differential pressure in bar equals head in metres multiplied by
specific gravity all divided by 10.19.
d) Ensure to check the seal minimum and maximum pressure
limits are not exceeded and the pressure is agreed with
Flowserve.
Special seals may require modification to auxiliary
piping described above. Consult Flowserve if unsure
of correct method or arrangement.
For pumping hot liquids, to avoid seal damage, it is
recommended that any external flush/cooling supply
be continued after stopping the pump.
4.6.4.3 Pumps fitted with heating/cooling jackets
Connect the heating/cooling pipes from the site
supply. The top connection should be used as the
outlet to ensure complete filling/venting of the
annulus with heating/cooling liquids; steam is usually
in at the top, out at the bottom.
4.6.5 Final checks
Check the tightness of all bolts in the suction and
discharge pipework. Check also the tightness of all
foundation bolts.
4.7 Final shaft alignment check
After connecting piping to the pump, rotate the shaft
several times by hand to ensure there is no binding
and all parts are free. Recheck the coupling
alignment, as previously described, to ensure no pipe
strain. If pipe strain exists, correct piping.
4.8 Electrical connections
Electrical connections must be made
by a qualified Electrician in accordance with relevant
local national and international regulations.
It is important to be aware of the EUROPEAN
DIRECTIVE on potentially explosive areas where
compliance with IEC60079-14 is an additional
requirement for making electrical connections.
It is important to be aware of the EUROPEAN
DIRECTIVE on electromagnetic compatibility when
wiring up and installing equipment on site. Attention
must be paid to ensure that the techniques used during
wiring/installation do not increase electromagnetic
emissions or decrease the electromagnetic immunity of
the equipment, wiring or any connected devices. If in
any doubt contact Flowserve for advice.
The motor must be wired up in
accordance with the motor manufacturer's
instructions (normally supplied within the terminal
box) including any temperature, earth leakage,
current and other protective devices as appropriate.
The identification nameplate should be checked to
ensure the power supply is appropriate.