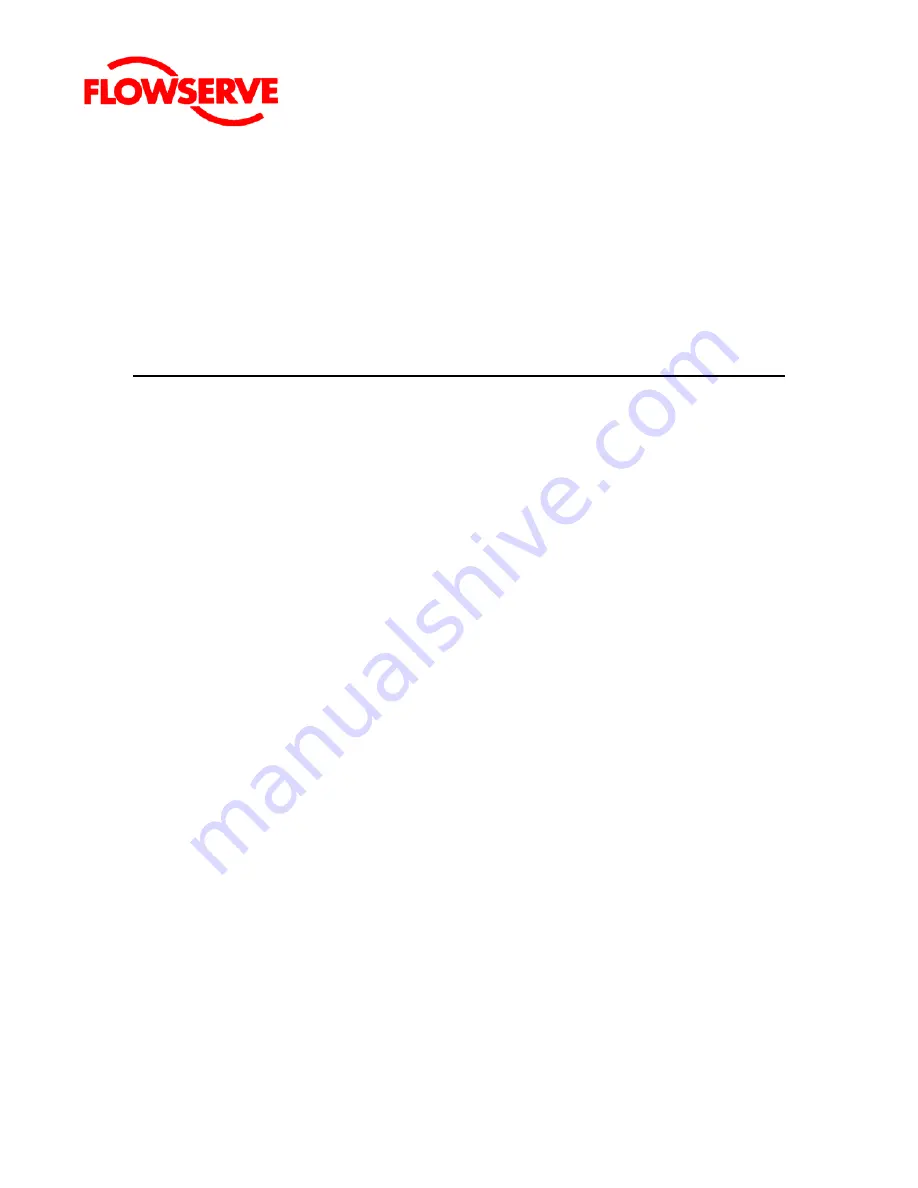
Pump Division
Flowserve Pumps
Flowserve Corporation
Pump Division
www.flowserve.com
3900 Cook Boulevard
Chesapeake, Virginia 23323-1626
Telephone 757-485-8000
Facsimile 757-485-8191
January 27, 2015
Pump Shop Coating Information
Customer: Carter & Verplanck
Tag: SMALL HIGH SERVICE 1&2
Project: West Nassau Regional WTP Order No.: 047-1244763
Service: Finished Water
S/N: 1244763CHP002A/B
P.O No.: 18227
Rev.:
0
PUMP INTERIOR (Casing):
Potapox Series 20
Thickness: 3.0 to 6.0 DFT
PUMP EXTERIOR (includes Baseplate & Guards):
SURFARCE PREPARATION
Near White blast clean, SSPC-SP 3
PRIME COAT
Tnemec Omnithan Series 1
Multiple passes to obtain 2.5 – 3.5 mils DFT
Note: Motors shall have motor vendors standard paint system.