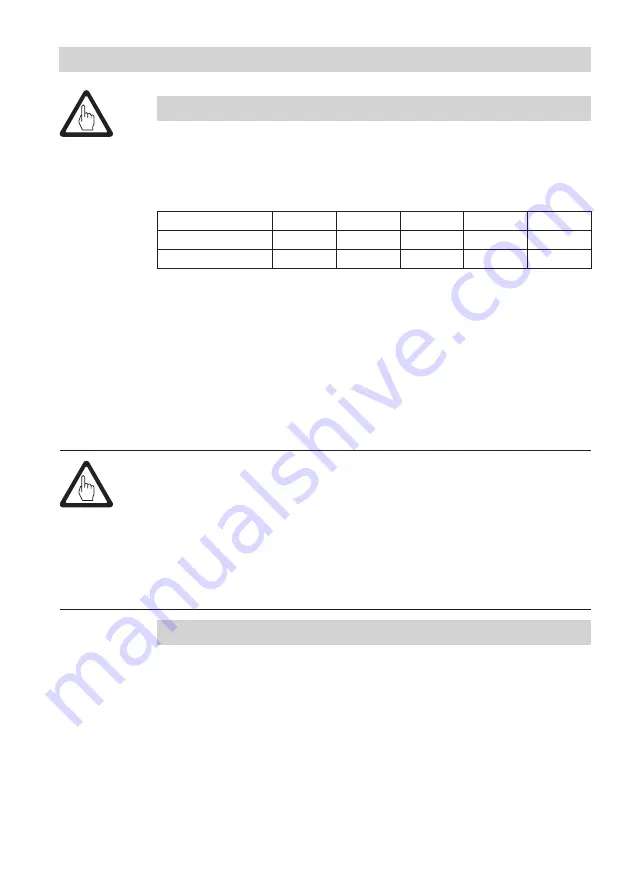
Attention
As the valve can be damaged by applying excessive forces, it is not allowed to use
additional levers to move the handwheels of nominal valve sizes up to and including
DN 5.
On all nominal sizes greater than DN 5, suitable additional levers may be used up to the
following torque limits:
DN
50
00
50
00
50
M
t
[Nm]
0
00
00
00
00
Hex. head WAF
6
46
46
46
46
The above values do not apply in the event of foreign matter or fluid deposits in the seat/
disc interface.
Note that additional levers must not be used in the immediate vicinity of the position
indicator.
Shut-off valves are normally used in such a way that they are either fully open or fully
closed.
For intermediate positions, variants with throttling disc should be fitted, unless throttling
discs are installed as a standard feature.
Performing throttling operations without a throttling disc may result in an excessive noise
level, excessive wear or even destruction of the valve by cavitation.
Functional test
The following functions must be checked:
Check the shut-off function of the installed valve prior to commissioning / start-up by
opening and closing it several times.
The bonnet/cover bolting shall be checked for tightness after the first loading or heating
up of the valves.
If required, the bonnet bolting must be gradually re-tightened cross-wise and evenly in a
clock-wise direction.
Attention
Before tightening the bonnet bolting open the valve by approximately two full turns of the
handwheel to avoid stress or distortion.
Re-tightening the bonnet/cover bolting is particularly important for valves installed in heat
transfer systems.
Commissioning
- continued -