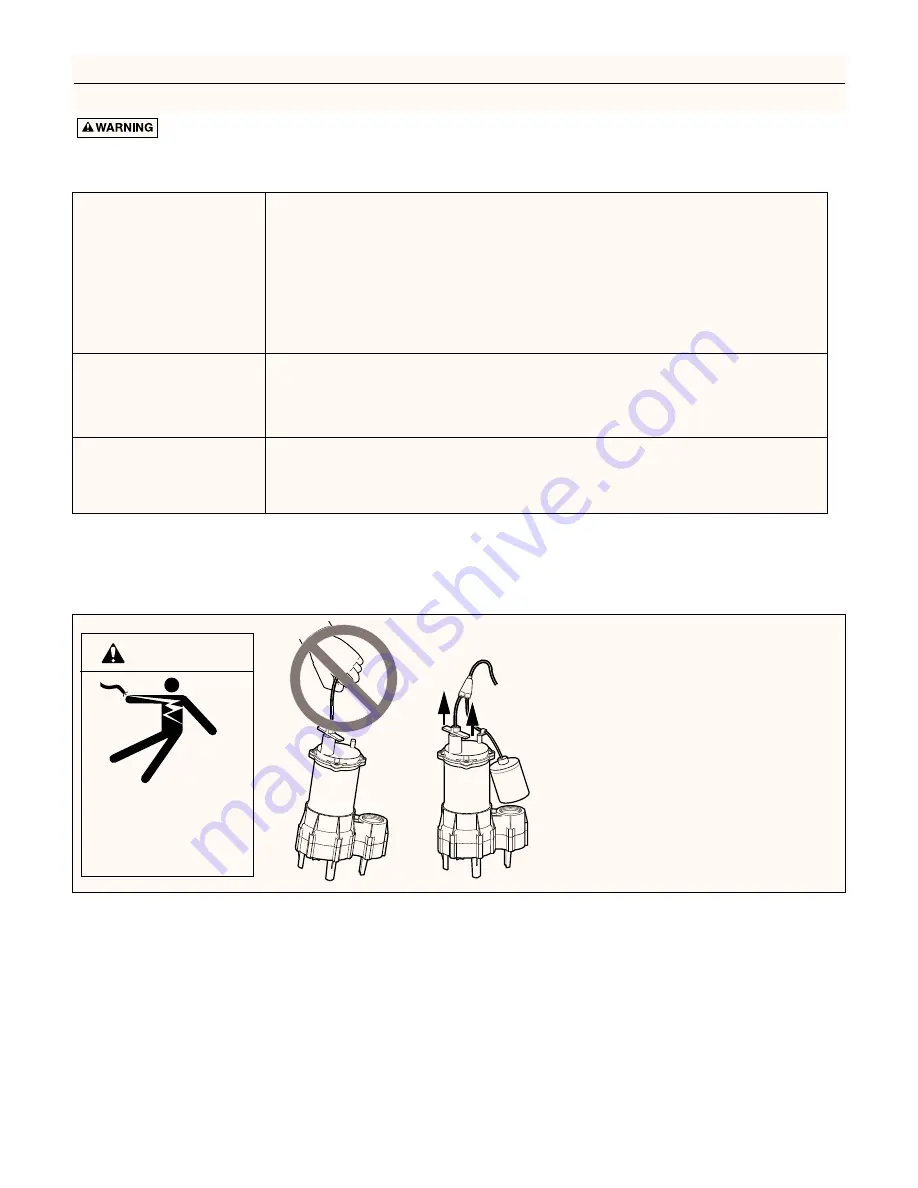
Troubleshooting
5
A. Pump fails to operate:
B. Pump fails to empty sump:
C. Pump will not shut off:
Sudden Starts. If power to pump is on when
thermal overload resets, pump may start without warning. If
you are working on pump, you may get an electrical shock or
impeller may catch fingers or tools. Disconnect power before
servicing pump.
1. Check to be sure that power cord is securely plugged into outlet. Disconnect power to
outlet before handling pump or motor.
2. Check to be sure you have electrical power.
3. Check that liquid fluid level is high enough to activate switch or controller.
4. Check to be sure that 4.7 mm (3/16") vent hole in discharge pipe is not plugged.
5. Check for blockage in pump inlet, impeller, check valve or discharge pipe.
6. Thermal overload may have tripped. Test start pump; if it starts and then stops immedi-
ately, disconnect from power source for 30 minutes to allow motor to cool, then
reconnect to power source. Check for cause of overheating/overloading.
1. Be sure all valves in discharge valve are fully open.
2. Clean out discharge pipe and check valve.
3. Check for blockage in pump inlet or impeller.
4. Pump not sized properly. A higher capacity pump may be required.
1. Check switch or controller automatic floats for proper operation and location.
See installation instructions for switch/controller.
2. If pump is completely inoperative or continues to malfunction, consult your local
serviceman.
1. Attempting to lift or support pump by
power cord can damage cord and
cord connections.
2. Cord may pull apart, exposing bare
wires with possibility of fire or electri-
cal shock.
3. Lifting or supporting pump by power
cord will void warranty.
4. Use T-handle on top of pump for all
lifting/lowering of pump. Disconnect
power to pump before doing any
work on pump or attempting to
remove pump from sump
1476 0195
Risk of electrical shock.
Can burn or kill.
Do not lift pump by
power cord.
WARNING