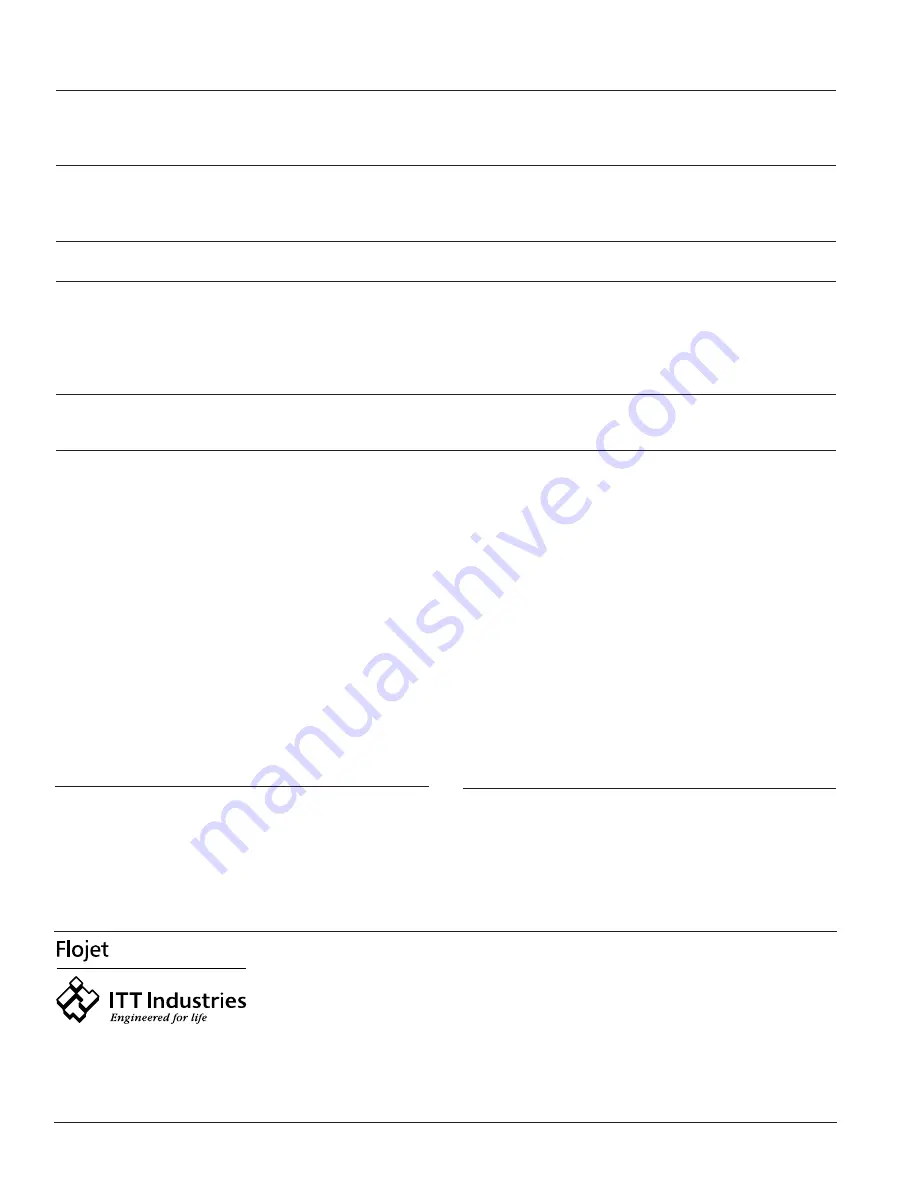
© Copyright 2003, ITT Industries
Printed in U.S.A.
All Rights Reserved
Form: 81000-363
02/03
WARRANTY
FLOJET warrants this product to be free of defects in material and/or
workmanship for a period of one year after purchase by the customer
from FLOJET. During this one year warranty period, FLOJET will at its
option, at no charge to the customer, repair or replace this product if
found defective, with a new or reconditioned product, but not to
include costs of removal or installation. No product will be accepted
for return without a return material authorization number. All return
goods must be shipped with transportation charges prepaid. This is
only a summary of our Limited Warranty. For a copy of our complete
warranty, please request Form No. 100-101.
RETURN PROCEDURE
Prior to returning any product to FLOJET, call customer service for an
authorization number. This number must be written on the outside
of the shipping package. Place a note inside the package with an
explanation regarding the reason for return as well as the
authorization number. Include your name, address and phone number.
TROUBLESHOOTING CHART
Symptom
Possible Cause(s)
Corrective Action
Pump will Pump will not start (stalls)
1. Inadequate air supply (20 PSI Min.)
1. Increase air inlet pressure
2. Contaminated air supply
2. An air dryer might be required
3. Ruptured diaphragm (2)
3. Replace diaphragm (2)
4. Check spool valve for wear
4. Replace spool valve if necessary
Pump runs, but no fluid
1. A leak or break in the product
1. Replace product line
inlet line
2. A leak or break in the product
2. Replace product line
discharge line
Pump leaks through exhaust port
1. Leak at upper exhaust port o-ring
1. Replace exhaust port
2. Inadequate slide lubrication
2. Replace with spool valve kit
Flow rate is low
1. Tubing or hose is damaged or
1. Clean or replace
blocked
2. Check viscosity of medium
2. Reduce viscosity of medium,
being pumped
increase hose diameter or contact
factory for recommendation
3. Check valves not seated correctly (1) 3. Reinstall check valves (1)
Pump leaks
1. Ruptured or worn out diaphragm (2) 1. Replace diaphragm (2)
2. Pump housing screws not torqued
2. Torque screws to 20 in lb
adequately
UNITED KINGDOM
Flojet, Unit 1, Avant Business Centre
Denbigh West Industrial Estate
Milton Keynes, Bucks, England MK1 1DL
Tel: 44 1908 370088
Fax: 44 1908 373731
CANADA
Fluid Products Canada
55 Royal Road
Guelph, Ontario N1H 1T1
Tel: (519) 821-1900
Fax: (519) 821-2569
JAPAN
NHK Jabsco Company Ltd.
3-21-10, Shin-Yokohama
Kohoku-Ku, Yokohama, 222
Tel: 045-475-8906
Fax: 045-475-8908
U.S.A.
Flojet
20 Icon
Foothill Ranch, CA 92610-3000
Tel: (949) 859-4945
Fax: (949) 859-1153
GERMANY
Jabsco GmbH
Oststrasse 28
22844 Norderstedt
Tel: +49-40-53 53 73-0
Fax: +49-40-53 53 73-11