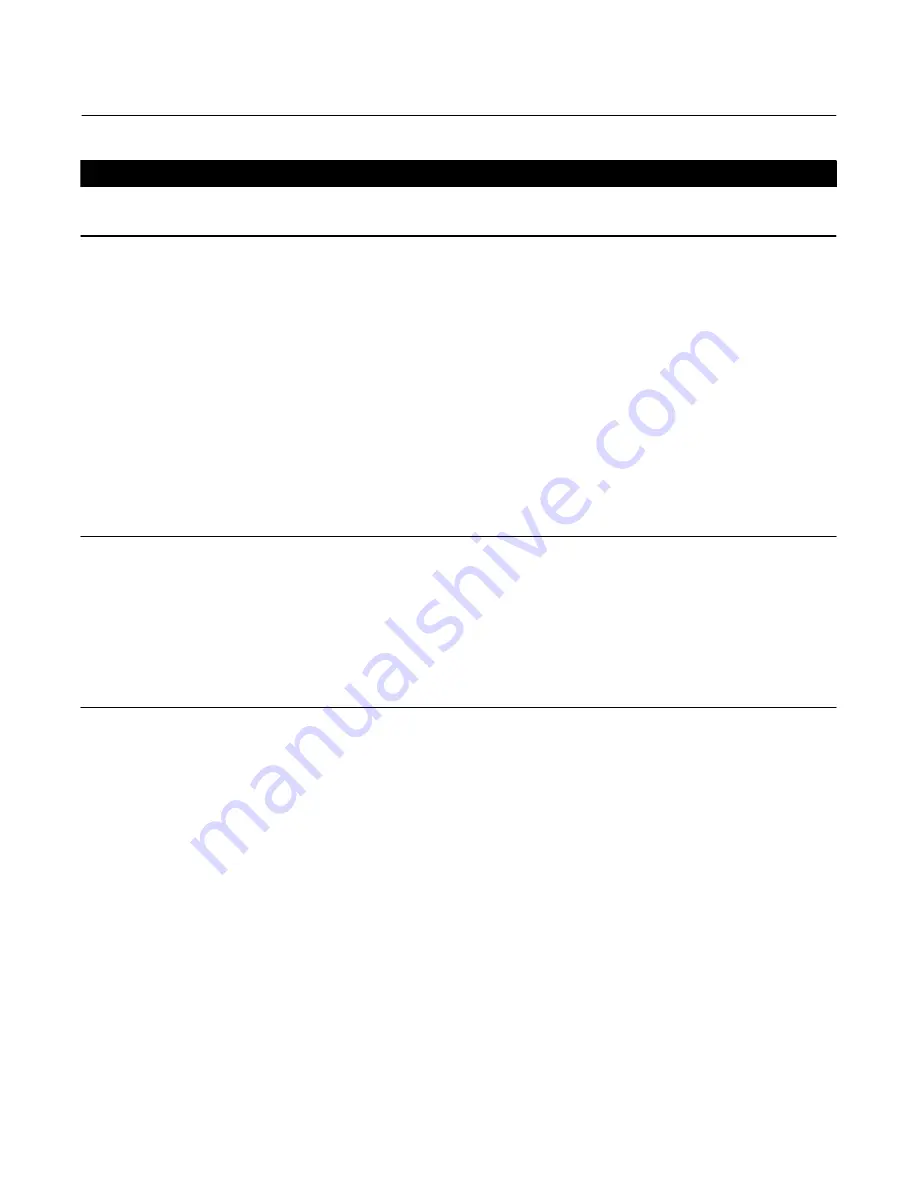
Instruction Manual
D100397X012
ES Valve
July 2017
10
CAUTION
To prevent possible product damage, cover the opening in the valve in the following procedure to prevent foreign material
from getting into the valve body cavity.
7. Remove the bonnet gasket (key 10, figure 13 through 15) and cover the opening in the valve to protect the gasket
surface and prevent foreign material from getting into the valve body cavity.
8. Remove the packing flange nuts, packing flange, upper wiper, and packing follower (keys 5, 3, 12, and 13, figure 8).
Carefully push out all the remaining packing parts from the valve side of the bonnet using a rounded rod or other
tool that will not scratch the packing box wall. Clean the packing box and the metal packing parts.
9. Inspect the valve stem threads and packing box surfaces for any sharp edges which might cut the packing.
Scratches or burrs could cause packing box leakage or damage to the new packing. If the surface condition cannot
be improved by light sanding, replace the damaged parts by following the appropriate steps in the Trim
Maintenance procedure.
10. Remove the covering protecting the valve body cavity and install a new bonnet gasket (key 10, figure 13 through
15), making sure the gasket seating surfaces are clean and smooth. Then slide the bonnet over the stem and onto
the stud bolts (key 15, figure 13, 14, or 15) or onto the valve body cavity if cap screws (not shown) will be used
instead.
Note
Proper performance of the bolting procedures in step 11 compresses the spiral wound gasket (key 12, figure 13 through 15) or
load ring (key 26, figure 14) enough to both load and seal the seat ring gasket (key 13, figure 13, 14, or 15). It also compresses the
outer edge of the bonnet gasket (key 10, figure 13 through 15) enough to seal the body‐to‐bonnet joint.
The proper bolting procedures in step 11 include‐‐but are not limited to‐‐ensuring that bolting threads are clean, and evenly
tightening the cap screws, or the nuts onto the studs, in a crisscross pattern. Because of the boltup characteristics of spiral wound
gaskets, tightening one cap screw or nut may loosen an adjacent cap screw or nut. Repeat the crisscross tightening pattern several
times until each cap screw or nut is tight and the body‐to‐bonnet seal is made. When the operating temperature has been
reached, perform this torquing procedure once again.
11. Install bolting, using proper bolting procedures during tightening so that the body‐to‐bonnet joint will withstand
test pressures and application service conditions. The bolt torques in table 3 may be used as guidelines.
12. Install new packing and the metal packing box parts according to the appropriate arrangement in figure 3, 5, or 7.
For split ring packing, alternate the positions of the splits to avoid creating a leak path. Place a smooth‐edged pipe
over the valve stem and gently tap each soft packing part into the packing box, being sure that air is not trapped
between adjacent soft parts.
13. Slide the packing follower, upper wiper, and packing flange (keys 13, 12, and 3, figure 8) into position. Lubricate
the packing flange studs (key 4, figure 8) and the faces of the packing flange nuts (key 5, figure 8). Install the
packing flange nuts.
14.
For spring‐loaded PTFE V‐ring packing,
tighten the packing flange nuts until the shoulder on the packing follower
(key 13, figure 8) contacts the bonnet.
For ENVIRO‐SEAL or HIGH‐SEAL live‐loaded packing,
refer to the note at the beginning of the Maintenance section.
For graphite packing,
tighten the packing flange nuts to the maximum recommended torque shown in table 4. Then,
loosen the packing flange nuts, and retighten them to the recommended minimum torque shown in table 4.
For other packing types,
tighten the packing flange nuts alternately in small equal increments until one of the nuts
reaches the minimum recommended torque shown in table 4. Then, tighten the remaining flange nuts until the
packing flange is level and at a 90‐degree angle to the valve stem.