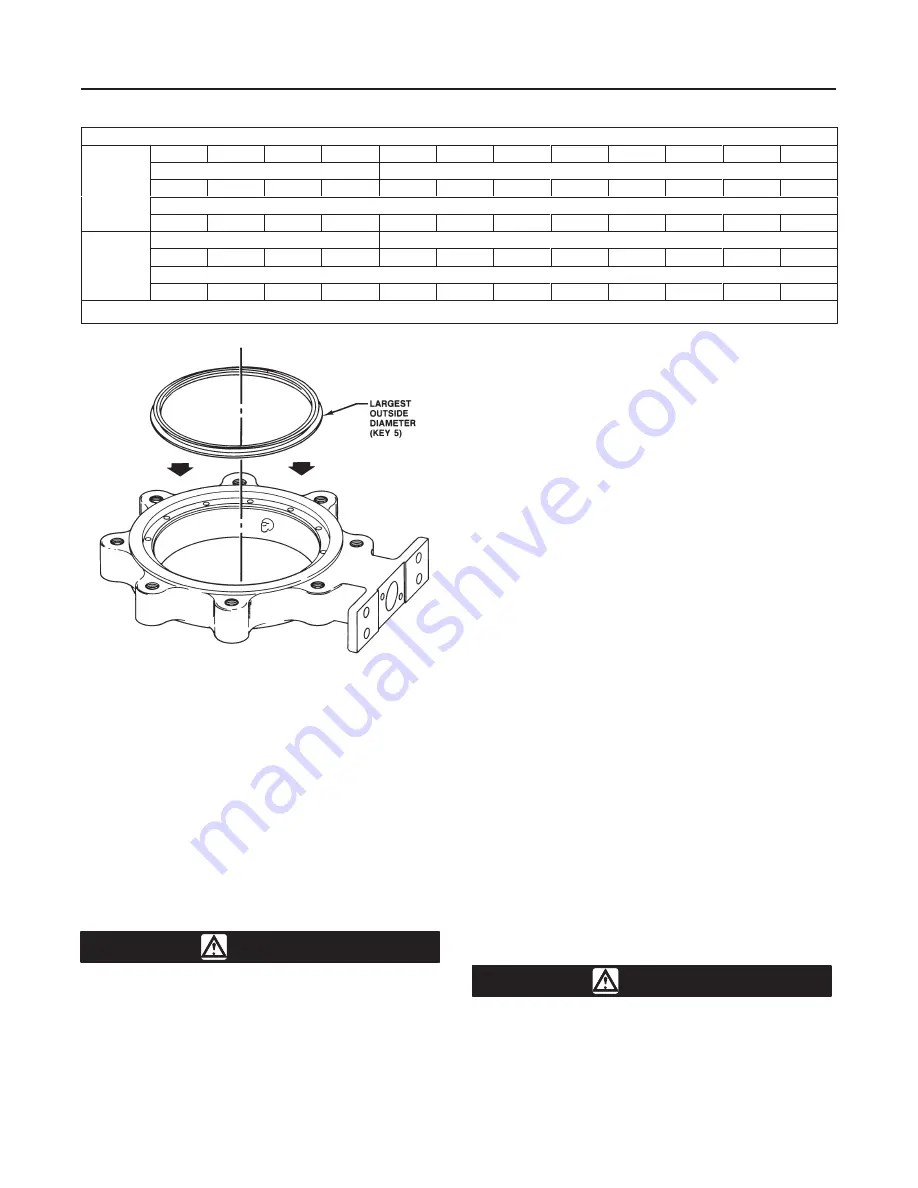
Model A31A
11
Table 6. Torque Values for Fasteners
FASTENER NOMINAL SIZE
#10
1/4
5/16
3/8
7/16
1/2
9/16
5/8
3/4
7/8
1
1-1/8
Retaining
Pounds-inch
Pounds-Foot
Retaining
Ring
41
100
220
400
53
83
119
166
296
480
720
1000
Ring
Screws
Newton
S
meters
4.6
11
25
45
72
112
161
225
401
651
976
1356
G
Pounds-inch
Pounds-Foot
Gasket
Retaining
35
81
167
295
39
59
86
119
210
330
480
617
Retaining
Bolts
Newton
S
meters
Bolts
4.0
9.2
19
33
53
80
117
161
286
447
651
837
Nore: These values are based upon standard materials, S66286/Inconel screws and ASTM A193GRB6 bolts. For other special fasterer materials, please contact your Fisher Controls
sales office or sales representative.
Figure 8. Typical Seal Installation
A5251-1*/IL
Removing the Valve
1. Disconnect any operating lines providing air pres-
sure, electric power, or a control signal to the actuator.
Be sure the actuator cannot suddenly open the valve.
Vent the power actuator loading pressure.
2. Use bypass valves or completely shut off the pro-
cess to isolate the valve from process pressure. Re-
lieve process pressure on both sides of the valve.
Drain the process media from either side of the valve.
CAUTION
Damage to the valve disk can occur if
the disk is not closed when the valve is
being removed from the pipeline. If nec-
essary, stroke the actuator to place the
disk in the closed position while remov-
ing the valve from the pipeline.
3. Loosen the flange bolting that holds the valve.
Make sure the valve cannot slip or twist while loosen-
ing and removing the bolting.
4. Before removing the valve from the pipeline, make
sure the valve disk is closed. Removing the valve with
the disk open could cause damage to the disk, piping,
or pipe flanges.
5. After removing the valve from the pipeline, move
the valve to an appropriate work area. Always support
the valve properly.
6. When valve maintenance is complete, refer to the
Installation procedures in this manual.
Seal Maintenance
Note
For larger valves, it is possible to re-
place the seal (key 5) while the actuator
is mounted to the valve and can be ac-
complished by cycling the valve to 90
degrees open.
Key numbers in this procedure are shown in figure 9
unless otherwise indicated.
1. After removing the valve from the pipeline, remove
the manual or power actuator. Manually rotate the up-
per shaft (key 3) counterclockwise until the disk has
moved a full 180 degrees away from the closed posi-
tion.
WARNING
Avoid personal injury or property dam-
age caused by the impact of a falling or
tipping of a large valve. Support large
valves during maintenance.