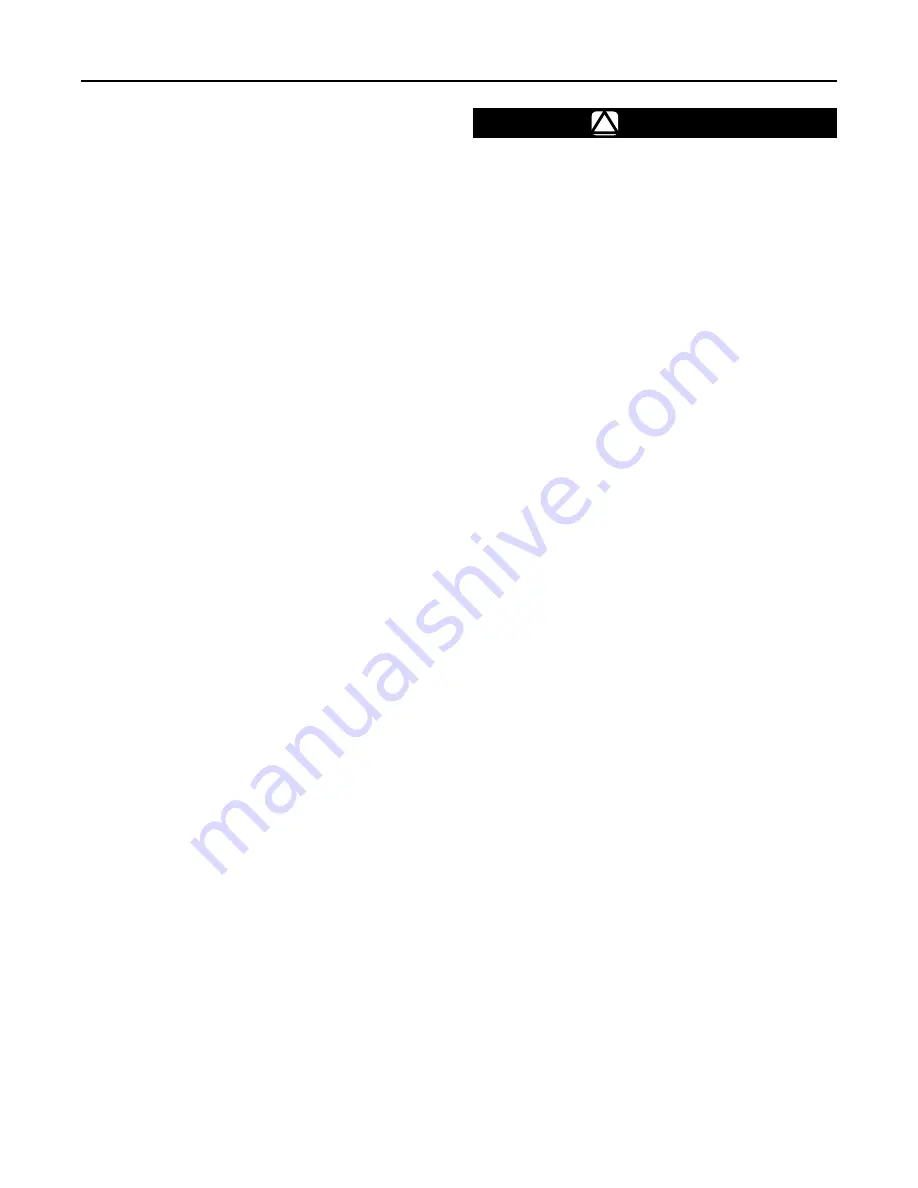
Inspect the vent hole regularly to make sure it is
not plugged. Spring case vent hole orientation
may be changed by rotating the spring case with
respect to the body. A 1/4 NPT spring case vent
may be remotely vented by installing obstruction-
free tubing or piping into the vent. Protect the
remote vent by installing a screened vent cap on
the remote end of the vent pipe.
5. For use in regulator shutdown, install upstream
block and vent valves and downstream block and
vent valves (if required), or provide some other
suitable means of properly venting the regulator
inlet and outlet pressures. Install a pressure gauge
to monitor instruments on startup.
6. Apply a good grade of pipe compound to the
external pipe threads before making connections,
making sure not to get the pipe compound inside
the regulator.
7. Install tubing fitting or piping into the 1/2 NPT
inlet connection on the body (key 1) and into the
1/2 NPT body outlet connection.
8. The two 1/4 NPT outlets can be used for a gauge
or other use. If not used, they must be plugged.
overpressure Protection
The 67D Series regulators have maximum outlet
pressure ratings that are lower than their maximum
inlet pressure ratings. A pressure-relieving or
pressure- limiting device is needed if inlet pressure
can exceed the maximum outlet pressure rating.
Types 67DR, 67DSR, 67DFR and 67DFSR have
a low capacity internal relief valve for minor seat
leakage only. Other overpressure protection must be
provided if the maximum inlet pressure can exceed
the maximum pressure rating of the downstream
equipment or exceeds the maximum outlet pressure
rating of the regulator.
Startup and adjustment
Key numbers are referenced in Figures 3 through 8.
1. With proper installation completed and downstream
equipment properly adjusted, slowly open the
upstream and downstream block valve (when used)
while using pressure gauges to monitor pressure.
WaRning
!
To avoid personal injury, property
damage or equipment damage caused
by bursting of pressure-containing
parts or explosion of accumulated
gas, never adjust the control spring
to produce an outlet pressure higher
than the upper limit of the outlet
pressure range for that particular
spring. if the desired outlet pressure
is not within the range of the control
spring, install a spring of the proper
range according to the diaphragm parts
maintenance procedure.
2. If outlet pressure adjustment is necessary,
monitor outlet pressure with a gauge during the
adjustment procedure. The regulator is adjusted
by loosening the hex nut (key 19), if used, and
turning the adjusting screw or handwheel (key 18)
clockwise to increase or counterclockwise to
decrease the outlet pressure setting. Retighten the
hex nut to maintain the adjustment position.
Shutdown
First, close the nearest upstream block valve and
then close the nearest downstream block valve
(when used). Next, open the downstream vent valve.
Since the regulator remains open in response to the
decreasing downstream pressure, pressure between
the closed block valves will be released through the
open vent valve.
Maintenance
Regulator parts are subject to normal wear and
must be inspected and replaced as necessary. The
frequency of inspection and replacement of parts
depends on the severity of service conditions and
applicable codes and government regulations. Open
the Type 67DF, 67DFR, 67DFS or 67DFSR drain valve
(key 2) regularly to empty accumulated liquid from the
dripwell (key 5).
note
if sufficient clearance exists, the body
(key 1) may remain mounted on other
equipment or in a line or panel during
maintenance unless the entire regulator
will be replaced.
5
67D Series