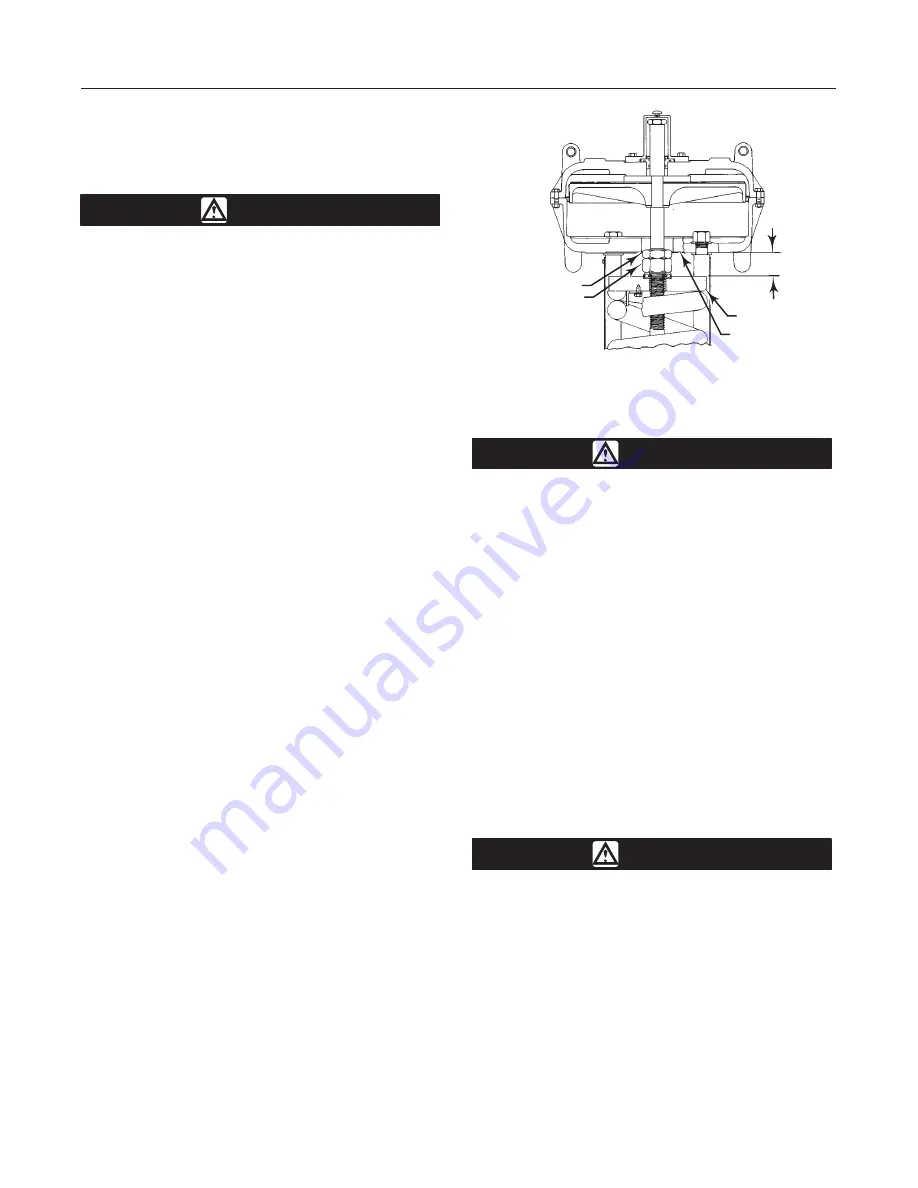
Type 657 Sizes 80 & 100
4
1. Back the stem locknuts away from the stem con-
nector, and slightly loosen the stem connector cap
screws.
CAUTION
Do not use wrenches or other tools di-
rectly on the valve stem. Damage to the
stem surface and subsequent damage
to the valve packing may result.
2. Tighten the locknuts together, using a wrench, then
screw the valve stem either into the stem connector to
lengthen travel or out of the stem connector to shorten
travel.
3. Cycle the actuator to check the travel. If actual
travel is not equal to the specified travel, adjust and
check travel until correct. Tighten the stem connector
cap screws when correct travel is obtained.
4. Raise the travel indicator disk by threading the
stem locknuts against the stem connector.
Spring
Make spring adjustments when the loading pressure
range applied to achieve specified travel is not equal
to the pressure range stamped on the actuator name-
plate (figure 3). Refer to the Bench Set pressure range
on the nameplate when the valve contains no pressure
and the packing is loosely inserted in the bonnet. Re-
fer to the Max. Allow. Supply on the nameplate when
the valve is controlling the specified pressure drop and
the packing is tightened to stop leaks around the stem.
Monitor loading pressure carefully when making ad-
justments. Do not exceed the pressure specifications
of either the loading regulator or the actuator casings.
Each actuator spring has a fixed pressure span.
Changing the spring compression shifts the span up or
down to make valve travel coincide with the loading
pressure range.
Size 80
Remove cover band (key 60, figure 5), insert a rod of
approximately 1/2-inch (12.7 mm) diameter into a hole
in the adjusting screw (key 12, figure 5), and rotate the
adjusting screw with the rod. Rotating the screw from
left to right will increase the loading pressure required
to start actuator stem travel; opposite rotation will de-
crease the pressure required to start travel.
Figure 4. Dimension B for Spring Adjustment
LOWER DIAPHRAGM
CASING
SPRING SEAT
JAM NUT
ADJUSTING NUT
A0950-1 / IL
B
Size 100
CAUTION
The actuator must be in the vertical
position when adjusting spring to avoid
damage to thrust bearing (key 35, figure
6) and to properly position spacers re-
quired for adjustment.
Remove the shroud plate (key 107, figure 6), and loos-
en the jam nut (key 115, figure 6).
For small spring forces, adjustments can be made by
rotating the adjusting nut (key 114, figure 6). Clock-
wise rotation (when viewed from diaphragm casings)
of the adjusting nut will increase the loading pressure
required to start actuator stem travel, and counter-
clockwise rotation will decrease the pressure required
to start travel. Tighten the jam nut when adjustment is
complete.
For high spring forces, it is necessary to use spacers
between the lower diaphragm casing and the spring
seat to isolate spring force from the adjusting nut.
WARNING
To avoid personal injury from the com-
pressed actuator spring snapping back
to its original length, make and use the
spacers by following the instructions in
the steps below.
1. It is recommended that three spacers be made of
3-inch schedule 80 pipe cut to the appropriate length
specified in step 2. If other than the recommended
material is to be used, be certain that the spacers are
capable of withstanding the spring force involved. The
spacers must be of equal length with ends cut squarely.