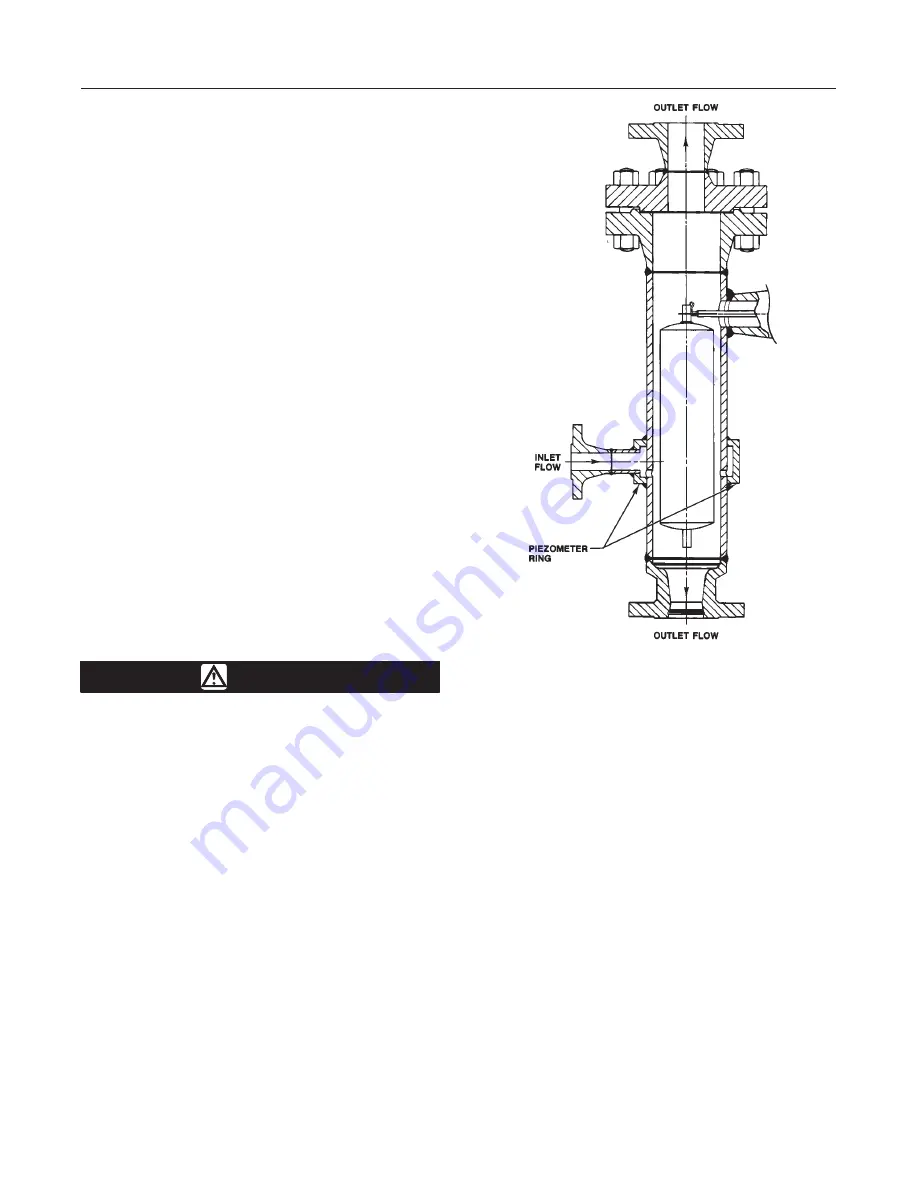
2502 Series
8
expands and contracts the same amount as the mea-
sured liquid to nullify signal changes that would be
caused by temperature changes.
This type of displacer is shipped in a separate carton
but crated with the rest of the assembly. See the ap-
propriate sensor manual for filling instructions.
Piezometer Ring
A piezometer ring (figure 10) is used when it is desir-
able to measure the specific gravity of a liquid in a
flowing line, and when the liquid velocity exceeds two
feet/minute (10 mm/second) past the displacer in the
cage. The piezometer ring reduces the velocity effects
caused by liquid passing through the displacer cage.
To install this type of sensor, connect a line to the
cage inlet and outlet piping at each end of the cage.
Use hand valves to balance the liquid flow through the
cage and keep the displacer cage filled. It is advisable
to provide a rotameter or sight flow gauge for measur-
ing velocity through the cage. If the flow rates are
properly balanced, the transmitter output will show
little change when flow through the cage is shut off. If
the flow rate through the cage is too high the turbu-
lence may cause an erratic output pressure signal.
Readjust hand valves to stabilize the output pressure
signal.
Regulator Supply Pressure
WARNING
Do not overpressurize any system com-
ponent. Personal injury or property
damage may occur due to sudden pres-
sure release or explosion. To avoid
damage, provide suitable pressure-re-
lieving or pressure limiting devices if
supply pressure can exceed the maxi-
mum supply pressure listed in table 1.
Personal injury or property danage may
occur from an uncontrolled process if
the supply medium is not clean, dry, oil-
free, or non-corrosive gas. Industry in-
strument air quality standards describe
acceptable dirt, oil, and moisture con-
tent. Due to the variability in nature of
the problems these influences can have
on pneumatic equipment, Fisher Con-
trols has no technical basis to recom-
mend the level of filtration equipment
required to prevent performance degra-
dation of pneumatic equipment. A filter
or filter regulator capable of removing
Figure 10. Piezometer-Ring Cage for Flow Line Mounting
A1317-1/IL
particles 40 microns in diameter will suf-
fice for most applications. Use of suit-
able filtration equipment and the estab-
lishment of a maintenance cycle to
monitor its operation is recommended.
Standard 2502 Series controllers come complete with
supply and output pressure gauges and an integrally
mounted Type 67FR regulator to reduce supply pres-
sure from a maximum of 250 psig (17.3 bar) to the 20
or 35 psig (1.4 or 2.4 bar) required. This regulator has
built-in relief and a standard 40-micron to remove par-
ticles from the supply source.
The output pressure connection is on the back of the
controller case (figure 3). Pipe the supply pressure to
the in connection of the regulator mounted to the case
back. Provide a clean, dry, and noncorrosive air or gas
supply to the controller as follows:
After pressure connections have been made, turn on
the supply pressure and check all connections for
leaks.