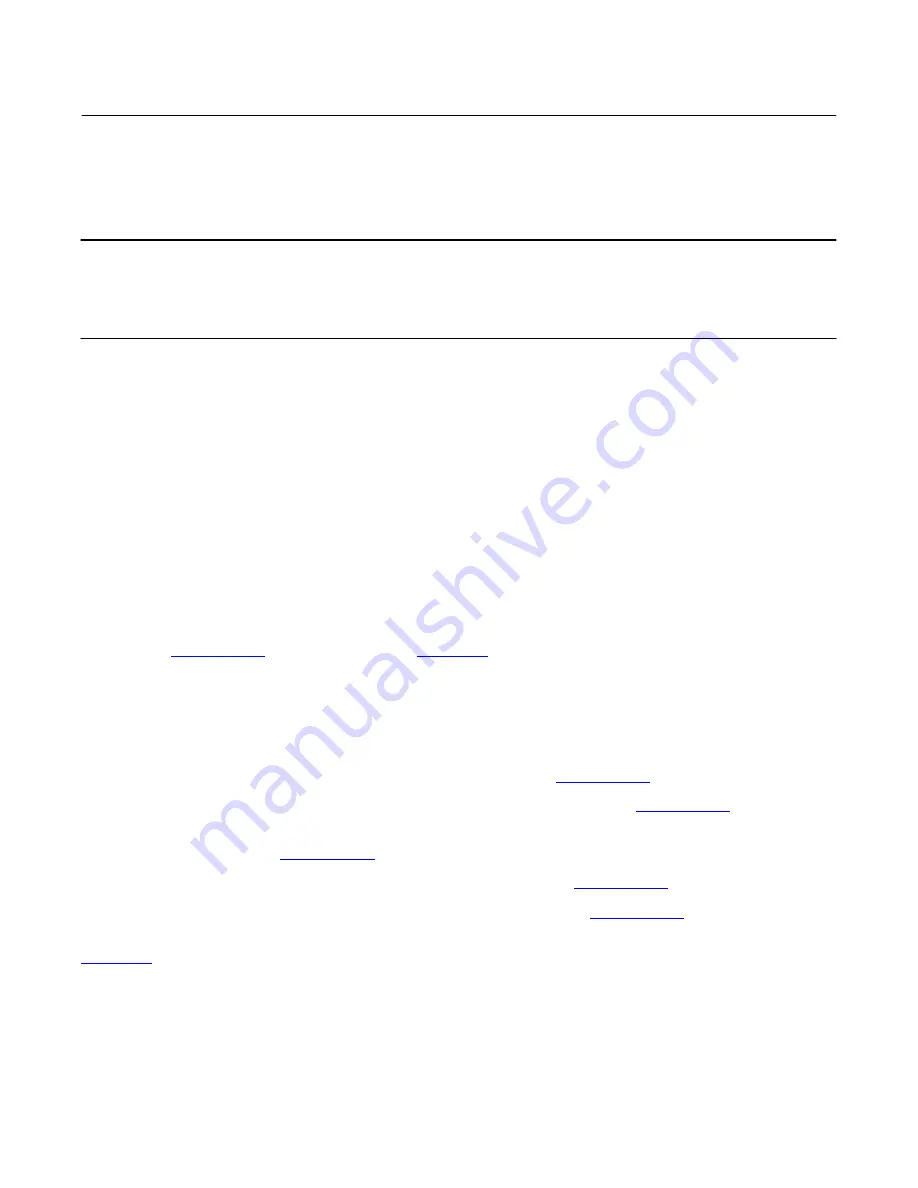
Instruction Manual
D200099X012
249 Caged Sensors
April 2017
12
4. Follow the proper procedure to remove the torque tube assembly (key 9).
5. Remove the bearing bolts (key 5), displacer rod assembly, and driver bearing.
6. Determine the new mounting orientation.
Note
Be sure that the driver bearing will be installed so that its knife edge is pointing up when the torque tube arm is mounted in the
desired orientation (figure 7). Since changing the mounting position of the torque tube arm by 180
will change controller or
transmitter action from direct to reverse or vice versa, the controller/transmitter action must be reversed from what it was before
the mounting method was changed.
7. Install the driver bearing, displacer rod assembly, and bearing bolts (key 5) into the torque tube arm. Install a new
arm gasket. Install the torque tube arm in the desired mounting position on the cage head and secure it with the
proper bolting (keys 19 and 20).
8. Install the torque tube assembly. Install the displacer.
9. If necessary, clean the cage following the procedure in this manual. Install the cage head and controller/transmitter.
Properly calibrate the controller/transmitter following the procedures given in the controller/transmitter
instruction manual.
Simulation of Process Conditions for Calibration of Fisher Level
Controllers and Transmitters
Contact your Emerson sales office or Local Business Partner for information on obtaining the Supplement to 249
Sensor Instruction Manuals—Simulation of Process Conditions for Calibration of Fisher Level Controllers and
Transmitters (
D103066X012
), or visit our website at
Fisher.com
.
Related Documents
This section lists other documents containing information related to the 249 level sensor. These documents include:
Bulletin 34.2:2500—2500‐249 Pneumatic Controllers and Transmitters (
D200037X012
)
Bulletin 34.2:249—Fisher 249 Sensor, Level Controller, and Transmitter Dimensions (
D200039X012
)
Simulation of Process Conditions for Calibration of Fisher Level Controllers and Transmitters— Supplement to 249
Sensor Instruction Manuals (
D103066X012
)
Bolt Torque Information— Supplement to 249 Sensor Instruction Manuals (
D103220X012
)
Torque Tube Identification— Supplement to 249 Sensor Instruction Manuals (
D103283X012
)
All documents are available from your Emerson sales office or Local Business Partner. Also visit our website at
Fisher.com
.
Parts Ordering
Whenever corresponding with your Emerson sales office or Local Business Partner about this equipment, always
mention the sensor serial number. Each sensor is assigned a serial number which is stamped on a nameplate (key 54,