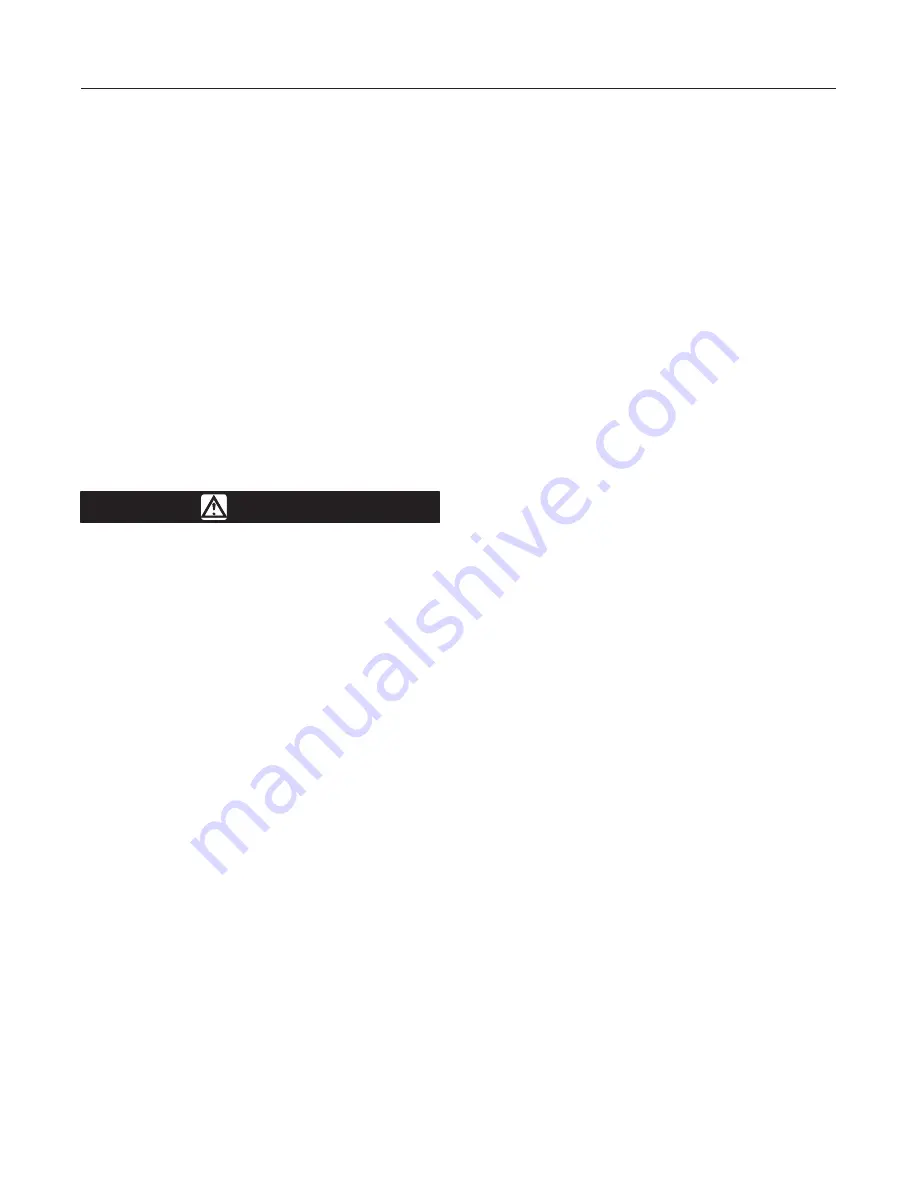
128-PQC
6
pressed against them. Then, push the packing spring
washer (key 6), packing spring (key 7), other packing
spring washer, wiper ring, and packing box washer
(key 4) down on the stem.
8. If installing a packing and trim assembly, remove
the sleeve, cage puller (key 44, if included in the as-
sembly), cage, and spring clip (key 38, if included in
the assembly) from the valve plug.
9. Install the valve plug into the stem.
Note
Rotate the valve plug until the shoulder
on the plug contacts the stem snugly.
Further tightening is not needed.
To replace the cage (if used) or to gain access to the
O-ring (key 12), use the cage puller (key 44) or a wire
hook to remove the cage from the valve body (key 1).
Then, install replacement parts as necessary.
CAUTION
Use care performing the installation in
the next step to avoid damaging the
O-ring.
10. Install the actuator and attached trim parts back
into the valve body (key 1), and secure with the four
nuts (key 14) attached to the lower diaphragm casing
assembly screws. Tighten the nuts to 15 lbf ft. (20
N m).
11. Connect the input signal line to the 1/4-inch NPT
connection of the appropriate diaphragm casing.
Changing Main Spring Range
Key numbers used in this procedure are shown in fig-
ure 8 unless otherwise indicated.
1. Isolate the control valve from the line pressure, re-
lease pressure from both sides of the valve body, and
drain the process media from both sides of the valve.
Also shut-off all pressure lines to the actuator and re-
lease all pressure from the actuator. Use lock-out pro-
cedures to be sure that the above measures stay in
effect while you work on the equipment.
If the valve is equipped with an optional handjack, be
sure the handjack assembly is not restricting the valve
from closing. Rotate the handles or handjack body
(key 48 or 47 in figure 9), if necessary, to allow the
main springs (key 19) to close the valve. Unscrew the
handles or pipe plugs and remove the indicator cover
(key 41 in figure 9). Drive out the groove pin (key 50 in
figure 9) and remove the stem nut and thrust washer
(keys 49 and 51 in figure 9).
2. Disconnect the input signal line, if necessary, and
remove the diaphragm casing nuts (key 14), cap
screws (key 21), and upper diaphragm casing (key
20).
3. With spring-close action, remove the existing main
springs (key 19) and install replacement springs of the
correct quantity and description as listed in table 3.
Make sure that the springs rest in the spring plate
holes and will not ride on the upper diaphragm casing
vent boss.
Note
Do not loosen the stem nut (key 14).
Disturbing its position in the following
step may keep the valve either from
shutting off or from opening completely
at the correct input signal pressure,
thus requiring complete reassembly of
the stem and diaphragm assembly.
4. With spring-open action, remove the locknut
(key 46), flat washer (key 15), diaphragm (key 16),
diaphragm plate (key 17), spring plate (key 18), and
main springs (key 19). Install replacement springs of
the correct quantity and description as listed in table 3.
Re-install the removed parts (keys 18, 17, 16, 15,
and 46) so that the lower ends of the main springs rest
over the weld stud heads of the lower diaphragm cas-
ing and the spring plate holes fit over the upper ends
of the springs. Tighten the locknut (key 46) to 12 lbf ft
(20 N m).
5. Install the upper diaphragm casing cap screws and
casing nuts. To avoid crushing the diaphragm, tighten
the cap screws and nuts evenly in a crisscross pattern
to 15 lbf ft (20 N m).
6. Connect the input signal line to the 1/4-inch NPT
connection of the upper diaphragm casing.
7. If an optional handjack is used, reinstall the hand-
jack parts. Be sure to secure the stem nut (key 49 in
figure 9) with the groove pin (key 50 in figure 9).
Reversing Action or Replacing Actuator
Parts
Key numbers used in this procedure are shown in fig-
ure 8 unless otherwise indicated.
1. Isolate the control valve from the line pressure, re-
lease pressure from both sides of the valve body, and
drain the process media from both sides of the valve.
Also shut-off all pressure lines to the actuator and re-
lease all pressure from the actuator. Use lock-out pro-
cedures to be sure that the above measures stay in
effect while you work on the equipment.