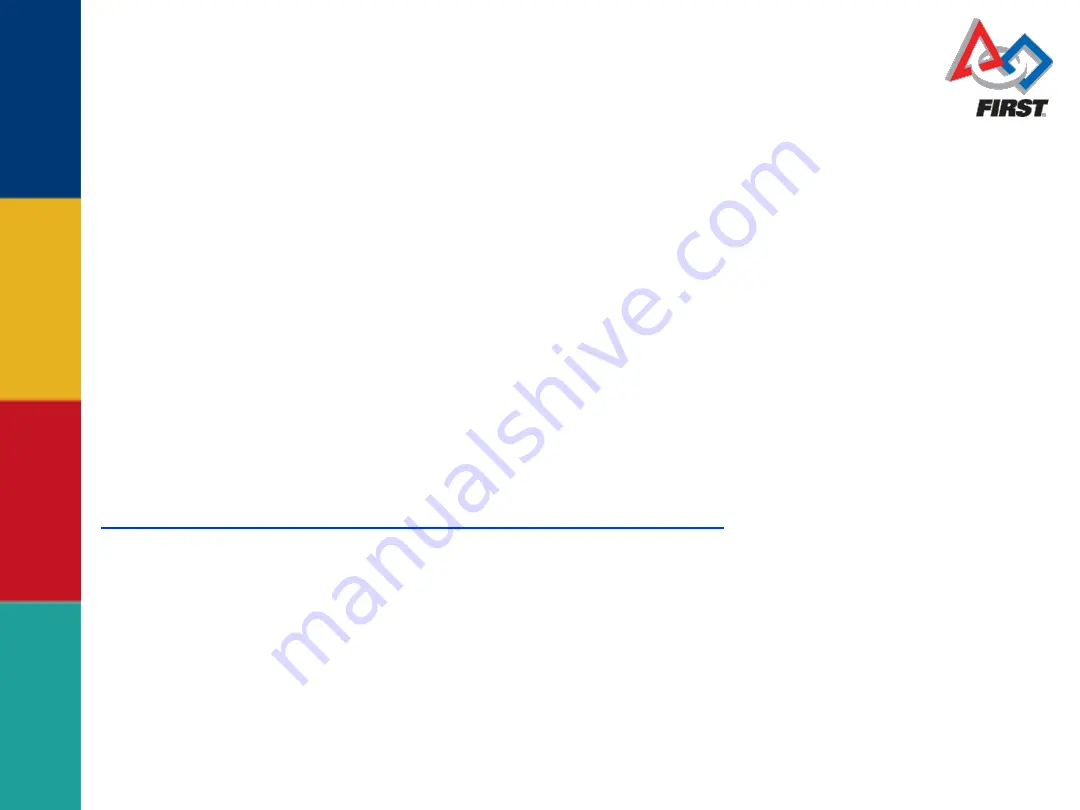
IMPORTANT NOTE!
IMPORTANT NOTE: The K9 bot was designed to be a compact, easily transportable
robot. It was originally used for testing and training in the early phases of the new
platform rollout. While the K9 bot is a convenient mechanism for teaching how to use
the new platform, it is
NOT a competition-ready bot
.
The K9 bot is built with parts that are
NOT included with the 2015-2016 standard
Tetrix FTC Kit of Parts
. The K9 bot also uses legacy NXT-compatible sensors, which
might be difficult to obtain if you don’t already own these older sensors.
An alternative (and recommended) training manual is available on the Team
Resources page of the FTC Website:
http://www.usfirst.org/roboticsprograms/ftc/team-resources
Under the
Build Resources
category there are links to a
PushBot Build Guide
. The
PushBot Build Guide
contains instructions on how to build and program a
competition-ready robot that only uses components that are included in the standard
FTC Kit of Parts.
Summary of Contents for K9 Bot
Page 1: ......
Page 4: ...1x 1x A ach one LEGO hard point connector to the 166 mm C channel...
Page 5: ...1x 2x Connect the LEGO 9 hole straight beam to the hard point connecter with the two pegs...
Page 6: ...1x Bolt the servo mount to the 166 mm C channel...
Page 7: ...Assemble the baring package by connecJng it to the servo mount 1x...
Page 8: ...Bolt a servo on to the servo mount 1x...
Page 9: ...2x A ach two 288mm C channels to the 166mm C channel...
Page 10: ...1x A second 166mm C channel is added to the 288mm C channels...
Page 11: ...The motor mounts are connected to the bo om of the 288mm C channels 2x...
Page 14: ...1x A ach a 166mm C channel to the two 288mm C channels...
Page 15: ...1x A ach another 166mm C channel to the 288mm C channels...
Page 16: ...Use the two rounded L brackets when a aching the plate to the 166mm C channels 2x 1x...
Page 17: ...Repeat last step to the other side of the robot 1x 2x...
Page 19: ...A ach the motor cable and secure it with a zip Je 1x...
Page 20: ...Repeat the last two steps to the other side of the robot 1x 1x...
Page 21: ...Read direcJons with encoders if you would like to install encoders onto your robot 2x OPTIONAL...
Page 22: ...Mount the servo horn to the pivot bracket 1x 1x...
Page 24: ...Insert the 88mm tube into the tube clamp and secure it using a bolt 1x...
Page 25: ...1x 1x 1x A ach the servo mount to the tube clamp with the rounded L bracket between them...
Page 26: ...Insert the 88mm tube into the other tube clamp and secure it with a bolt...
Page 27: ...1x Assemble the bearing package by connecJng it to the servo mount...
Page 28: ...1x A ach the servo to the servo mount...
Page 29: ...Mount the servo horn to the pivot bracket 1x 1x...
Page 31: ...1x A ach the at bracket to the pivot bracket...
Page 32: ...1x Mount a pivot bracket to the rounded L bracket...
Page 33: ...2x Connect two rounded L brackets to the pivot bracket to complete the gripper...
Page 36: ...2x Use the set screws to lock the motor hubs onto the leQ and right motor shaQs...
Page 37: ...1x Use zip Jes to secure the ba ery to the 144mm L bracket...
Page 39: ...Mount the Modern RoboJcs USB servo controller to the leQ side of the robot...
Page 40: ...Mount the Modern RoboJcs USB motor controller to the right hand side of the robot...
Page 47: ...1x Using the pan head screws a ach the 144 mm L beam to the two rounded L brackets 2x...
Page 52: ...1x A ach the LEGO IR seeker to the two stand o s...
Page 56: ...Secure the robot controller to the two 144mm L brackets I used hook and loop...
Page 57: ...Run the mini USB to micro USB OTG cable from the power module to the robot controller...
Page 69: ...4x 3x 2x 2x 3x 1x 2x 1x 2x 2x 2x 2x...
Page 70: ...2x 2x 2x 2x 2x 2x 2x 2x 2x 1x 1x 8x...
Page 71: ...3x 4x 12x 2x 6x 2x 1x 2x 1x 1x 2x...
Page 72: ...1x 1x 1x 1x 2x 1x 1x...
Page 74: ......