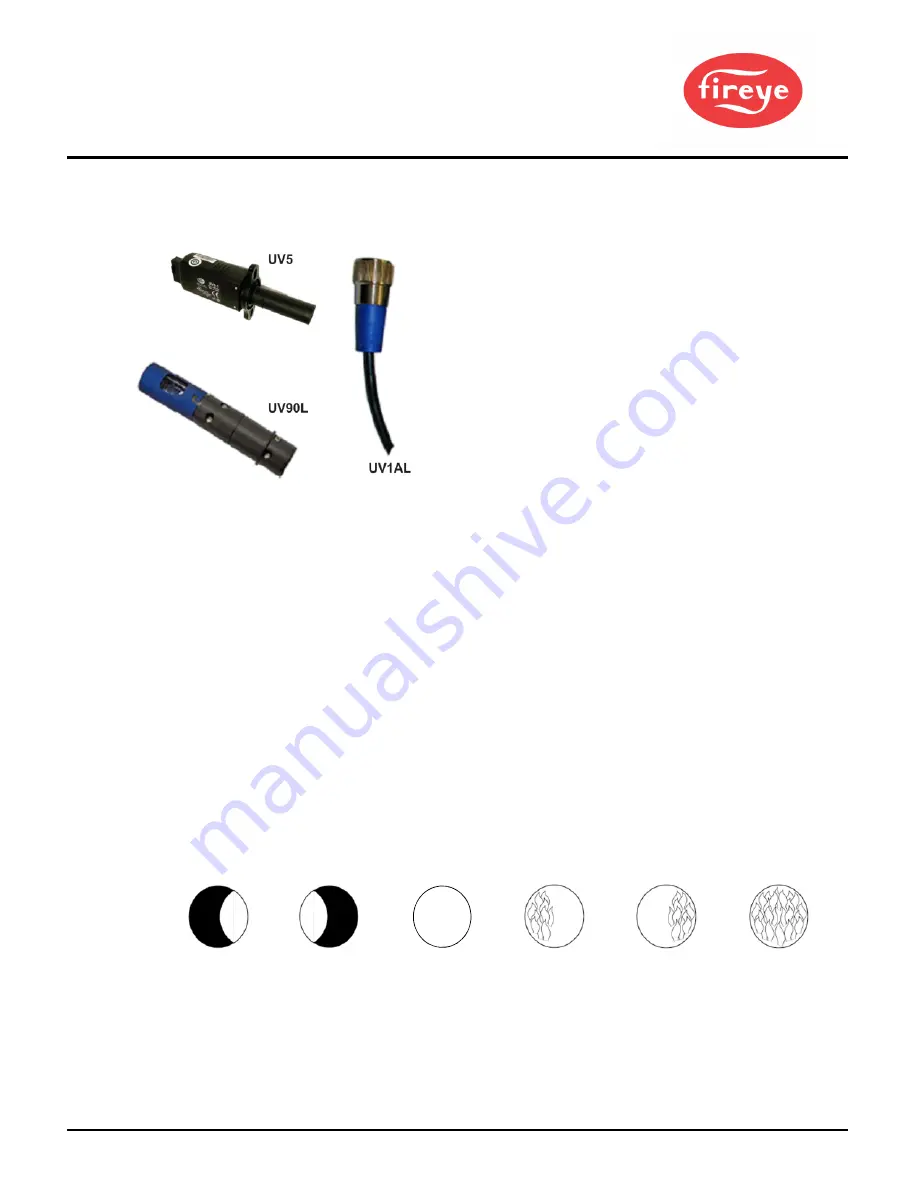
© 2021 Carrier
16
FLAME SCANNERS
INSTALLATION - UV SCANNERS
Where possible, obtain the burner manufacturer’s instructions for mounting the scanner. This infor-
mation is available for most standard burners. The scanner mounting should comply with the follow-
ing general instructions:
1.
Position the UV1AL, UV90L or UV5 scanner within 39 inches (1 meter) of the flame to be
monitored.
2.
Select a scanner location that remains within the ambient temperature limits of the UV scanner.
3.
The UVlAL scanner is designed to seal off the sight pipe up to 1 PSI pressure. Higher furnace
pressures must be sealed off. To seal off positive furnace pressure up to 50 PSI for the UV1AL
scanner, install a quartz window coupling (P/N: 60-1257). Add cooling air to reduce the scanner
sight pipe temperature.
4.
Install the scanner on a standard NPT pipe (UV1AL: ½”) whose position is rigidly fixed. If the
scanner mounting pipe sights through the refractory, do not extend it more than halfway through.
Swivel flanges are available if desired (P/N: 60-302). The sight pipe must permit an unobstructed
view of the pilot and/or main flame, and both pilot and main flames must com- pletely cover the
scanner field of view.
SCANNER MUST HAVE UNOBSTRUCTED
VIEW OF FLAME
NOT THIS
NOT THIS
BUT THIS
FLAME MUST COMPLETELY COVER
SIGHT OPENING
NOT THIS
NOT THIS
BUT THIS
Summary of Contents for 60-2991 Series
Page 14: ... 2021 Carrier 14 ...
Page 15: ... 2021 Carrier 15 ...