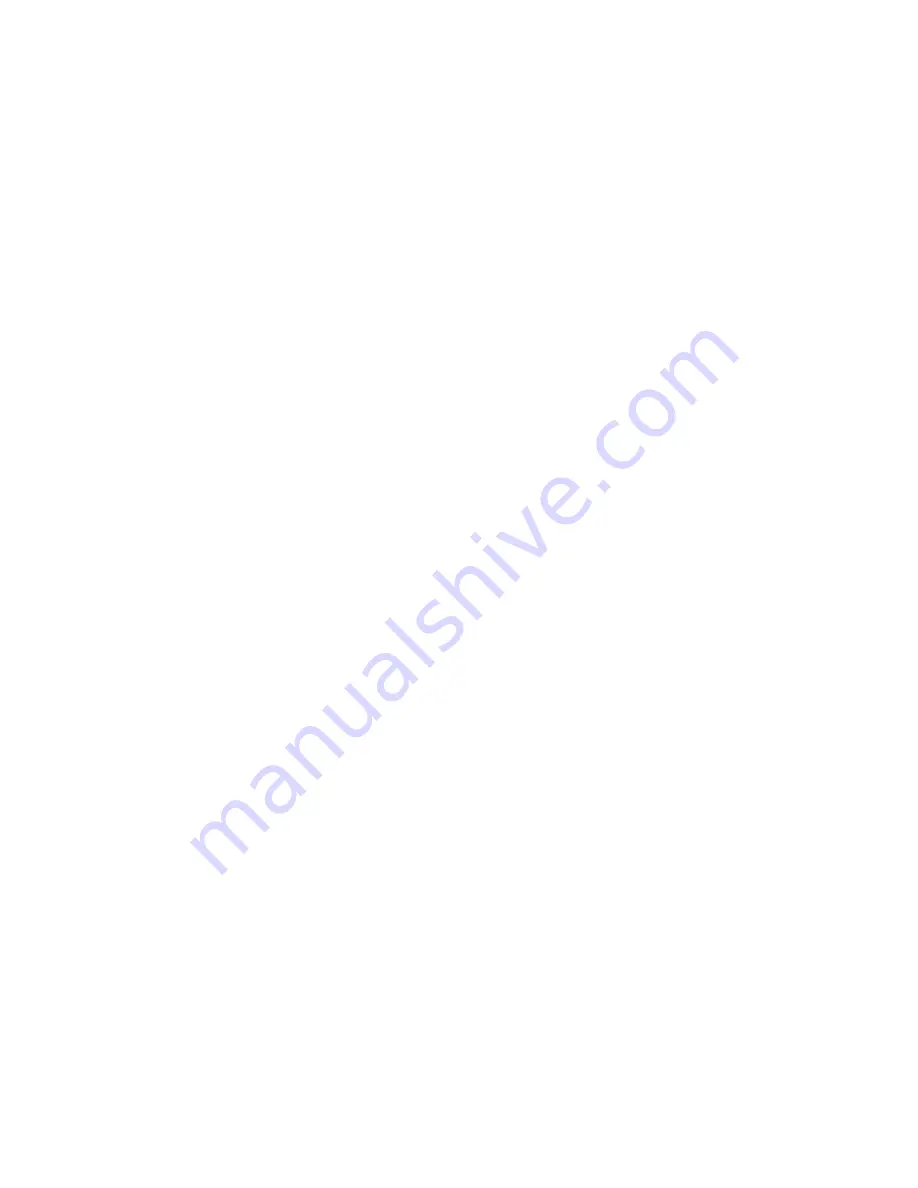
36
the yoke rests against a block of wood placed
between the yoke and the housing.
• With a soft mallet, drive the cross shaft out of
the yoke just far enough to expose the two
woodruff keys (T15).
• Remove the woodruff keys.
• Slide or tap the cross shaft out of the yoke and
housing.
INSPECT THE PTO COMPONENTS:
Ball Bearings: Visually examine for indications of
wear, corrosion, or pitting on balls and races. Apply
clean, lightweight engine oil and slowly rotate the
outer race while holding the inner race. The balls must
roll free. Rough or sticking spots must be checked to
be sure they are not particles of dirt. If they are, clean
and check again. If not dirt, replace the bearing.
Bell Housing:
• Check the bearing fit. Bearing races usually are
designed with a sliding or slightly snug fit in the
housing bore. They should not have side move-
ment in the bore. Labyrinth seal bores at the
output end of the bearing housing should be
round, not oval and should be approximately
.020”-.025” (.508mm-.635mm) diameter larger
than the drive shaft.
• If a bearing failure has occurred, be sure the
bearing has not spun in the housing, destroying
the shoulder or bore contacted by the bearing.
• The mounting pilot O.D. and mounting face
must be free of protruding metal, rust corrosion
etc., which would prevent the housing from
locating properly in the flywheel housing bore
or against the bearing house face. An improper
fit causes misalignment. Misalignment is a
major cause of power take-off failure. The
snapring should restrict bearing movement to
.015” (.381 mm) maximum.
• Cross shaft holes should not be worn more than
.015” (.381 mm) out of round. A little wear
does not render the parts unserviceable, but
excessive wear can cause binding of the cross
shaft under load during clutch engagement.
Cross Shaft:
• Be sure the cross shaft moves freely in the bell
housing. Remove rust or corrosion from the
cross shaft and the holes in the bell housing.
Wear on the cross shaft does not become detri-
mental until it inhibits smooth rotation during
clutch engagement (creates a false clutch
engagement pressure reading) or allows mois-
ture, dirt, or other corrosives to enter the hous-
ing. This can be prevented by ample greasing
through the grease fittings to keep the cross
shaft lubed. If the cross shaft is excessively
worn on only one side, it can be reinstalled with
the worn area 180( from its original position.
Most Rockford cross shafts are splined on both
ends and may be reversed in the housing.
• Woodruff key slots must hold the keyways
straight. If the release yoke has been loose on
the cross shaft the keyways may have one side
worn at an angle.
Clutch Release Yoke:
• Keyways must not be worn excessively.
• Replace if width of cradles is over .700” (17.78
mm).
Drive Shaft:
• Pilot bearing journal must not be worn. A new
pilot bearing should have a sliding-but-snug fit
or tight fit. Finn recommends that a new pilot
bearing is installed whenever the PTO assembly
is completely taken apart.
• Threads must not be damaged.
• Keyways must not be worn so as to allow side
movement of keys.
• Clutch taper should not be worn, although a
small amount of wear, if worn evenly 360
˚
around the shaft may be serviceable as long as
the clutch will seat securely and squarely and
the jam nut will tighten against the clutch body.
If too much wear has occurred the clutch will
slide too far onto the taper and the jam nut will
bottom out on the thread or shoulder before it
contacts the clutch body.
DISASSEMBLE THE CLUTCH:
1.
Preparation for disassembly.
• Disengage the clutch.
• Match-mark the clutch body (H1), pressure
plate (H3), and release sleeve (H25).
2.
Remove the release sleeve and bearing sub-
assembly.
• Remove the lever spring (H12).
• Notice the direction of the clevis pins (H31 and
H33) are installed. Upon reassembly of the
clutch they must be installed from the same
side so the head leads the direction of clutch
rotation.
• Remove retainers (H34) and clevis pins (H33)
Summary of Contents for HydroSeeder T170 SSA
Page 2: ...BLANK...
Page 30: ...26...
Page 32: ...28...
Page 36: ...Figure 4 32...
Page 44: ...NOTES 40...
Page 45: ...NOTES 41...
Page 46: ...NOTES 42...
Page 47: ...NOTES 43...
Page 48: ...NOTES 44...
Page 49: ...45 T170 HydroSeeder Parts Manual Model SSA...
Page 79: ...75 LBT170 SSA BLANK...