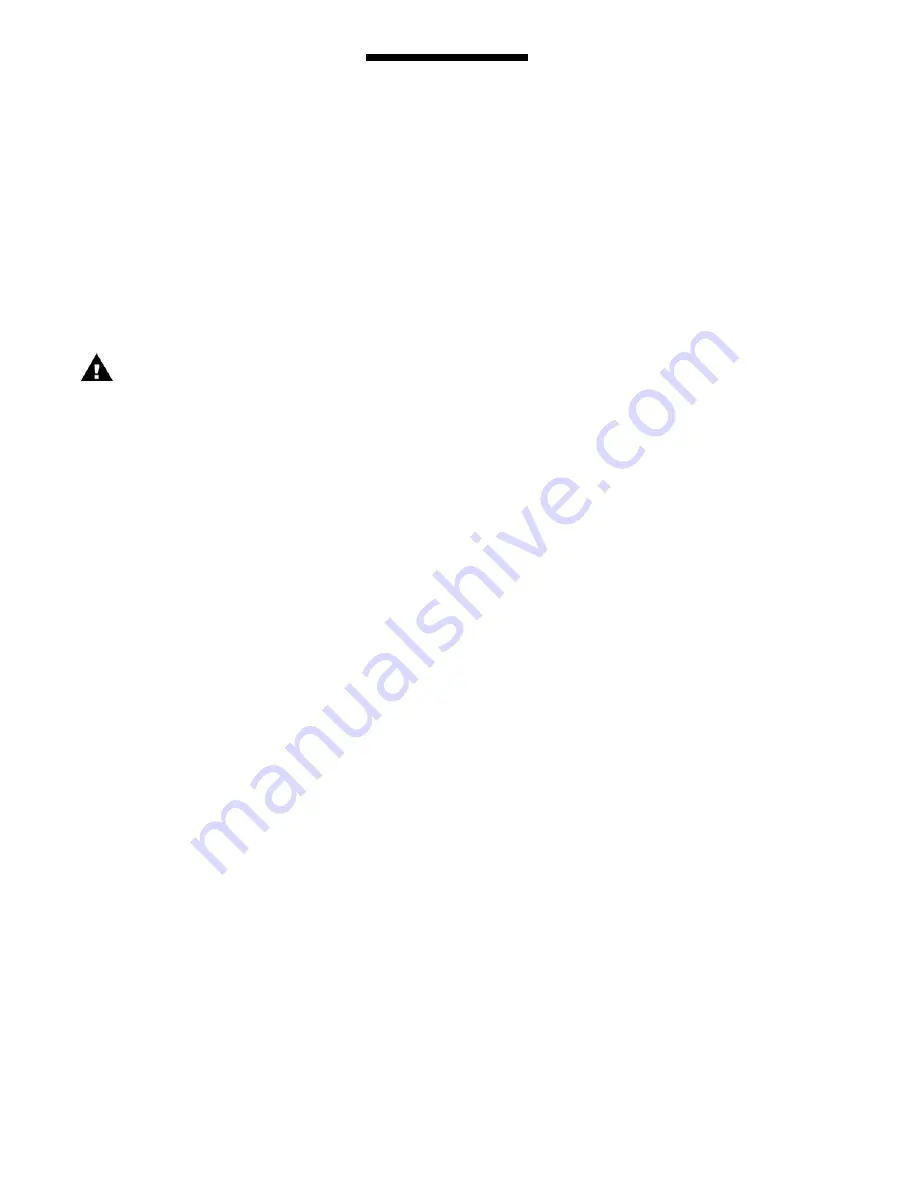
3. Install the rotating faces and cooling collar to the motor
adapter.
a. Carefully slide the housing cover over the impeller’s
shaft. The side of the housing cover with the pressed-
in seal face should be away from the impeller.
b. Separate the rotating head of the seal from the spring.
NOTE: If using a special seal material, it is vital that the
special seal face mates against the housing cover’s station-
ary face.
c. Lubricate the impeller’s shaft, then carefully slide the
rotating face of the seal over the Impeller’s shaft using
a twisting motion. The carbon or special side of the
rotating face should be toward and pressed against
the stationary face of the housing cover.
CAUTION: The carbon or special portion of the seal is
easily damaged. Take care not to apply uneven force or
crack the carbon or special material while installing.
d. Place the seal’s spring into position on top of the
installed rotating face.
e. Relubricate the impeller’s shaft and then carefully slide
the second rotating face of the seal over the Impeller’s
shaft using a twisting motion (the carbon side of the
second rotating face should be facing away from
the other rotating face). This will require some com-
pression of the seal’s spring.
f. Place the cooling collar’s o-ring into position. Slide the
cooling collar onto the Impeller’s shaft, with the
stationary face in the cooling collar pressed against
the second rotating face. Continue to slide the cooling
collar until it mates against the housing cover. Hold
the cooling collar in this position. Take care to align
the water connections so they are accessible.
NOTES:
1) The seal’s spring must be compressed further in
order to mate the cooling collar and housing cover.
2) Take care not to pinch the cooling collar’s o-ring. If
the o-ring is not properly seated, the cooling collar
will leak.
4. Place the pump components onto the motor adapter.
While holding the cooling collar against the housing cover,
install the assembly into the motor adapter. The motor
adapter will hold the cooling collar in place. It will now
be necessary to hold the impeller to keep the seal’s spring
compressed.
5. Carefully place the assembly in position to the motor’s
face.
a. Screw the impeller onto the motor shaft or shaft adapter.
Use a drop of Blue 242 Loctite on the motor shaft or
shaft adapter (item 20) threads. It will be necessary to
hold the motor’s fan with a screwdriver to keep the motor
shaft from turning.
b. Align the motor adapter so that the access hole is
straight up.
c. Bolt the motor adapter to the motor using the hex-head
cap screws and lock-washers.
d. Double check the alignment of the water connection
holes in the cooling collar.
6. Install the impeller housing.
a. Install the housing cover’s o-ring.
b. Place the impeller housing into position and install the
hardware. Tighten the six hex-head cap screws to 90
inch-pounds.
c. Look through the discharge of the pump to verify prop
er spacing between the impeller and the housing cover.
If using a 56C or metric motor adapter, adjust the shaft
adapter if necessary (refer to the “assembly”section of
these instructions).
TROUBLESHOOTING
NO OR INSUFFICIENT FLOW
1. Pump not primed.
2. Closed valve.
3. Viscosity too high.
4. Air leaks in suction piping.
5. Discharge head higher than anticipated.
6. Suction lift too high or insufficient NPSH. Check also for clogged
suction line.
7. Motor wired for wrong rotation.
INSUFFICIENT PRESSURE
1. Air or gasses in liquid.
2. Impeller diameter too small.
3. Discharge head higher than anticipated.
4. Motor wired for wrong rotation.
LOSS OF PRIME
1. Leaking suction line.
2. Foot valve or suction opening not submerged enough.
3. Foot valve too small or leaking.
4. Air or gasses in liquid.
5. Foreign matter in impeller.
EXCESSIVE POWER CONSUMPTION
1. Head lower than rating. Excessive flow.
2. Specific gravity or viscosity of liquid is too high.
EXCESSIVE VIBRATION
1. Loose piping or bolts.
2. Pump cavitating from improper suction or feed.
4