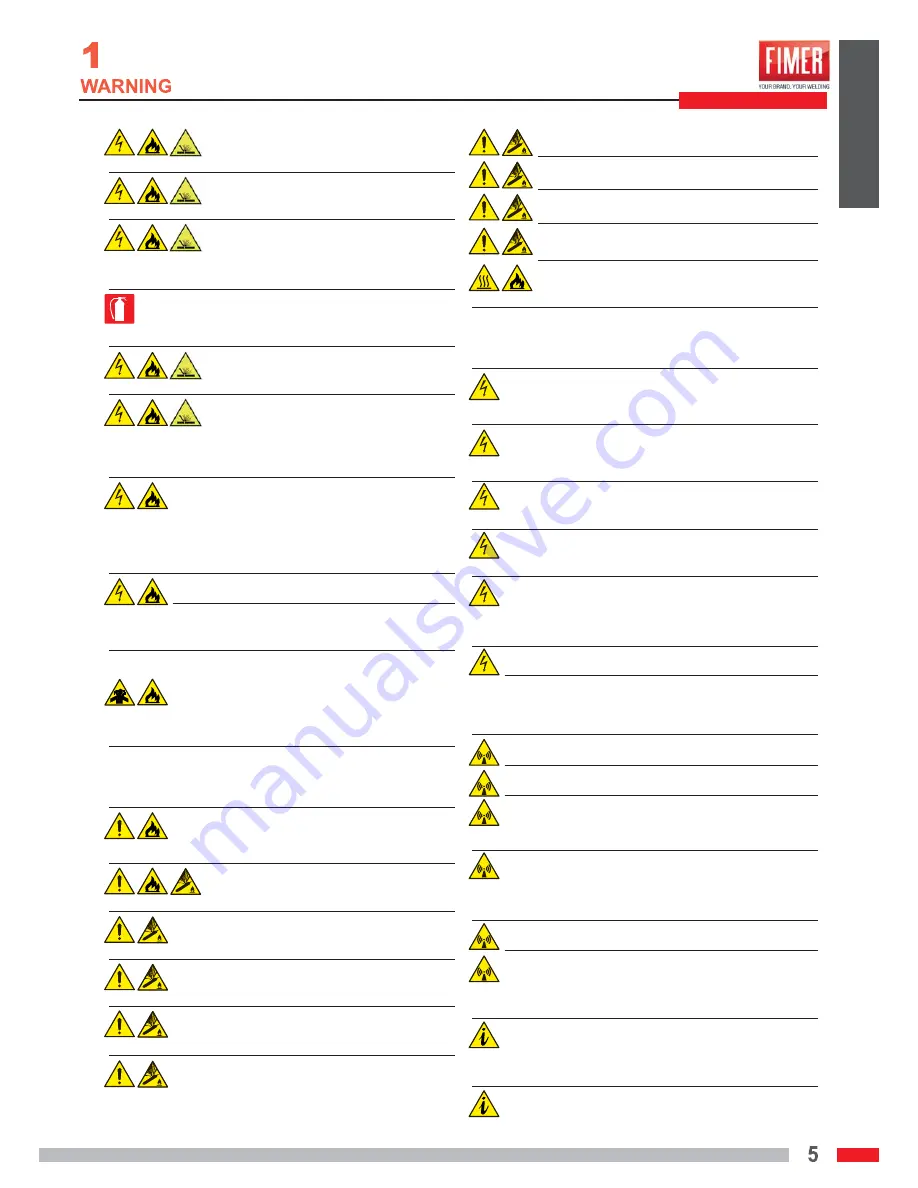
ENGLISH
WORK-AREA FLOORING
The work-area flooring
MUST be fireproof.
WORK-AREA SURFACES
Work benches or
tables used during welding MUST have fire-
proof surfaces.
WALL AND FLOOR PROTECTION
The walls
and flooring surrounding the cut environment
must be shielded using non-flammable materials.
This not only reduces the risk of fire but also avoids damage to
the walls and floors during cut processes.
EXTINGUISHER
Place an approved and appropriately-sized
fire extinguisher in the work environment.Check its working
order regularly (carry out scheduled inspections) and ensure
that all parties involved know how to use one.
CLEAN ENVIRONMENT
Remove all flam-
mable materials away from the work envi-
ronment.
SERIOUS DANGER ! 1
NEVER cut in confined
spaces (e.g. in a container vehicle, a cistern
or a storeroom etc.) where toxic, inflammable
or explosive materials are, or have been, located or stored.
Cisterns, in particular, may still contain toxic, flammable or explosive
gases and vapours years after they have been emptied.
SERIOUS DANGER ! 2
NEVER cut a cistern that
contains (or has stored) toxic, inflammable or
explosive materials. They could still contain toxic,
flammable or explosive gases and vapours years after they
have been emptied. If you are obliged to weld a cistern, ALWAYS
passivate it by filling it with sand or a similar inert substance
before starting any work.
SERIOUS DANGER! 3
NEVER use the Welder to
melt frozen water pipes.
VENTILATION
VENTILATION
Together with the previous instructions, the following pre-
cautions should be strictly observed
WELDING ENVIRONMENT VENTILATION
Ventilate the cut
environment carefully. Maintain sufficient air-flow
to avoid toxic or explosive gas accumulation. Cut
processes on certain kinds or combinations of metals
can generate toxic fumes. In the event of this hap-
pening, use air-supply respirators. BEFORE cut, read and
understand the welding alloy safety provisions.
PROTECTIVE WELDING GASES
PROTECTIVE WELDING GASES
Together with the previous instructions, the following pre-
cautions should be strictly observed when welding with
protective gases
GAS TYPES
These welders use only inert (non-
flammable) gases for welding arc protection. It is
important that the appropriate type of gas is chosen
for the type of welding being performed.
UNIDENTIFIED GAS CYLINDERS
NEVER
use unidentified gas cylinders.
PRESSURE REGULATOR 1
NEVER connect the
cylinder directly to the Welder. Always use a pressure
regulator.
PRESSURE REGULATOR 2
Check the regulator
is performing its function properly. Read the regulator
instructions carefully.
PRESSURE REGULATOR 3
Never lubricate any
part of the regulator.
PRESSURE REGULATOR 4
All regulators are
designed for a specific type of gas. Check the
regulator is appropriate for the protective gas to
be used.
DAMAGED GAS CYLINDERS
NEVER use damaged
or faulty cylinders.
CYLINDER RELOCATION
NEVER lift a gas cylinder
by holding the regulator.
GAS CYLINDERS
Do not expose gas cylinders to
excessive heat sources, sparks, hot slag or flames.
GAS HOSE 1
Check the gas hose is not damaged.
GAS HOSE 2
Always keep the gas hose well away
from the work area.
ELECTRIC SHOCK
ELECTRIC SHOCK
Together with the previous instructions, the following pre-
cautions should be strictly observed to reduce the risk of
electric shock
ELECTRIC SHOCK INJURY
DO NOT touch a person
suffering from electric shock if he/she is still in contact
with the cables. Switch the mains power source off imme-
diately THEN provide assistance.
CABLE CONTACT
Do not tamper with power cables if
the mains power is still switched on. Do not touch the
welding circuitry. Welding circuitry is usually low voltage,
however, as a precaution, do not touch the welder electrodes.
CABLE AND PLUG PRECAUTIONS
Check the power
supply cable, plug and wall-socket regularly. This is particularly
important if the equipment is relocated often.
REPAIRS
Never attempt to repair the Welder yourself. The
result would not only cause warranty cancellation but also
high danger risks.
MAINTENANCE PRECAUTIONS
Always check that the
electric power supply has been disconnected before per-
forming any of the maintenance operations listed in this
manual ( e.g. before replacing any of the following: worn elec-
trodes, welding wires, the wire feeder etc.)
Never point the welding gun or the electrode towards yourself
or others.
ELECTROMAGNETIC COMPATIBILITY
ELECTROMAGNETIC COMPATIBILITY
Check no power supply cables, telephone cables or other
electrical items (e.g. computer cables, control lines etc.)
are in the vicinity of the cut.
Check there are no telephones, televisions, computers or
other transmission devices close to the Welder.
Make sure that people with pace-makers are not in the
immediate vicinity of the Welder.
Do not use the Welder in hospitals or medical environments
(including veterinary surgeries). Make especially sure there
is no electrical medical equipment being used close to where
welding is being done.
Should the Welder interfere with other apparatus, take the
following precautionary measures:
1. Check the Welder’s side panels are securely fastened.
2. Shorten the power supply cables.
3. Place EMC filters between the Welder and the power source.
EMC compatibility : CISPR 11, Group 2, Class A.
This Class A equipment is not intended for use in residential
locations where the electrical power is provided by the public
low-voltage supply system. There may be potential difficulties
in ensuring electromagnetic compatibility in those locations, due to
conducted as well as radiated disturbances.
This equipment does not comply with IEC 61000-3-12. If it is
connected to a public low voltage system, it is the responsability
of the installer or user of the equipment to ensure, by consultation
with the distribution network operator if necessary, that the equipment
may be connected.
This equipment is suitable for using in industrial environmentswith
mains power protected by residual current operated circuit-
breaker (time delay), Type B and tripping current of >200 mA
Summary of Contents for 5T5.555.452
Page 1: ...910 100 539GB REV01 Ed 2016_05_03 KRONOS 500 dual pulse INSTRUCTION MANUAL ...
Page 5: ...ENGLISH ...
Page 6: ...KRONOS 500 dual pulse 5T5 555 452 ...
Page 10: ...1 2 5 8 7 6 10 11 13 15 17 18 3 9 12 16 14 4 ...
Page 11: ...ENGLISH 25 26 27 30 19 21 20 22 23 24 28 29 ...
Page 12: ...1 2 3 4 5 6 7 8 9 10 20 19 18 17 16 15 14 13 12 SD 11 a b a b b a b b a b ...
Page 13: ...ENGLISH DSF DUAL PULSE PULSE a b c d a b d c b a d b a 2a function ...
Page 14: ...a b b a a b c ...
Page 15: ...ENGLISH ...
Page 16: ......
Page 17: ...ENGLISH A B C D E F G H ...
Page 19: ...ENGLISH ...
Page 20: ......
Page 21: ...ENGLISH ...
Page 22: ......
Page 23: ...ENGLISH ...
Page 24: ...Torch Trigger Torch Trigger T T a b DSF ...
Page 25: ...ENGLISH ...
Page 26: ...DSF b b ...
Page 27: ...ENGLISH ...
Page 28: ......
Page 29: ...ENGLISH ...
Page 30: ......
Page 31: ...ENGLISH Torch Trigger Torch Trigger a b Torch Trigger T T T T Torch Trigger a b ...
Page 32: ......
Page 34: ......
Page 35: ...ENGLISH ...
Page 36: ......
Page 37: ...ENGLISH ...
Page 39: ...ENGLISH ...
Page 40: ......
Page 41: ...ENGLISH ...
Page 42: ......
Page 43: ...ENGLISH ...
Page 44: ......
Page 45: ...ENGLISH ...
Page 46: ......
Page 47: ...ENGLISH ...
Page 48: ......
Page 51: ...ENGLISH ...