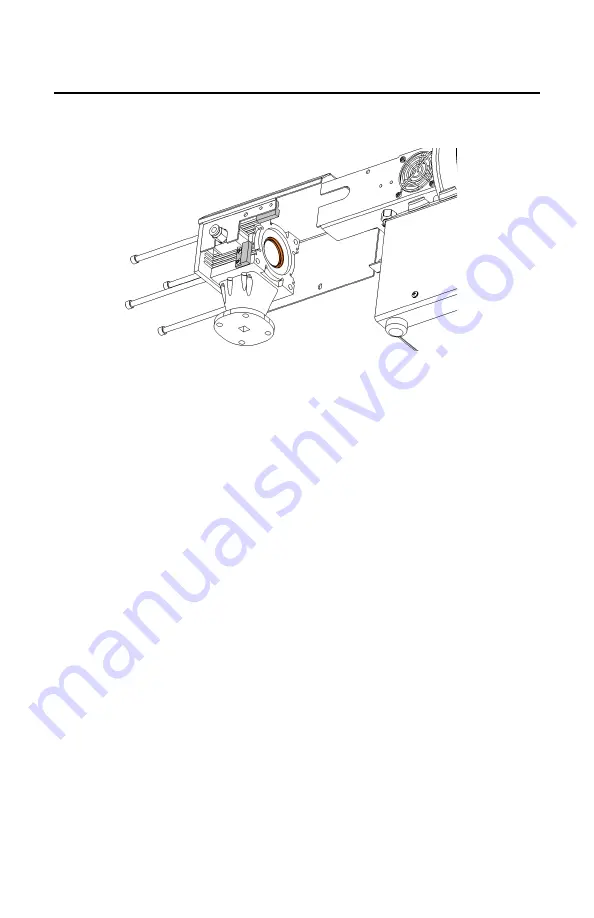
16
Removing the Head Assembly cont.
4. Before reassembling, check the seal for damage and remove any
debris.
5. Reinstall the head assembly (reverse Step 3).
6. Reinstall the Phillips head machine screws (reverse Step 2).
7. Reinstall the (4) long Allen head assembly bolts.
These need very
little torque to secure the head to the motor base. Excessive torque
will put too much pressure on the bearings and can stop the motor
from turning or strip the threads. The leverage afforded by the short
end of the hex tool is plenty for this task. Tighten the bolts in an X
pattern until they are finger tight.
8. Refer to the Blade Adjustment section to ensure proper blade
adjustment before operating.