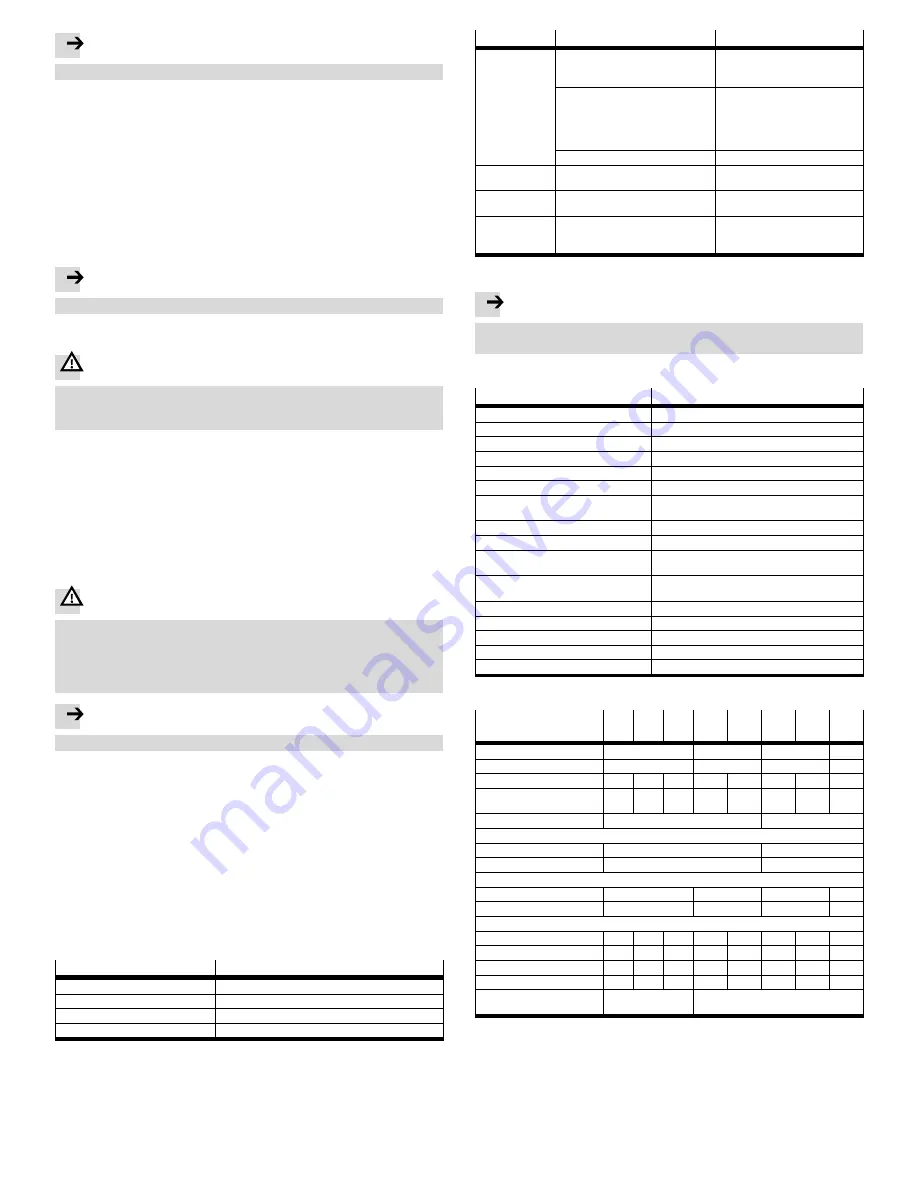
6
Commissioning
Note
Commissioning should only be conducted by qualified personnel.
Requirements
– The valve is fully mounted and connected.
– If incompressible media are used, fill the piping with the medium.
Check operating conditions
Check operating conditions and limit values (
è
Technical data).
Check connection points for tightness.
Check compatibility of the devices in the system for maximum pressure (con
sider pressure peaks). If necessary, adjust the application parameters.
Placing valve in operation
Slowly apply medium pressure to the valve.
è
The valve closes.
Note
If medium pressure is applied suddenly, the valve opens briefly.
7
Operation
Warning
Risk of injury due to hot surface!
The valve can become hot at high media temperature.
Do not touch the valve during operation or immediately afterward.
Observe the operating conditions.
Observe permissible limits.
After longer standstills:
Actuate the valve several times and check for correct function.
8
Maintenance and care
Every 6 months, check product from the outside for leakage and function.
Clean product regularly. The permissible cleaning agent is soap suds.
9
Disassembly
Warning
Risk of injury from combustion and chemical burns.
The media in the piping system and the valve can be hot and under pressure.
Medium residues can be in the product and escape when open or dismantled.
Allow the valve and piping to cool and depressurize them.
Wear specified protective equipment.
Note
Disassembly of the valve only by qualified specialized personnel.
1. De-pressurise the piping.
2. Allow the valve and pipeline to cool.
3. Empty the piping and valve completely.
– Make sure no one is located in front of the outlet opening.
– Catch discharging media in a suitable container.
4. Disconnect the piping connections and remove the valve.
10
Disposal
Observe the local specifications for environmentally friendly disposal.
Dispose of the product in an environmentally friendly manner. When doing this,
also take residual media into account (potential recycling of hazardous waste).
11
Accessories
Accessories
è
www.festo.com/catalogue
Designation
Type
Fastening bracket
HRM
Plug socket
MSSD-N
Solenoid coils for VZWM-...-F4
MD-2-24VDC-PA, MD-2-110VAC-PA, MD-2-230VAC-PA
Solenoid coils for VZWM-...-F5
MH-2-24VDC-PA, MH-2-110VAC-PA, MH-2-230VAC-PA
Fig. 6
12
Fault clearance
Malfunction
Possible cause
Remedy
Solenoid valve vi
brates or does
not switch
Differential pressure too low
Check application parameters
Increase differential pressure
between input and output.
Flow resistance at the output too low
Check piping cross sections and
line lengths.
If necessary, install flow-redu
cing components on the output
side (elbows, etc.).
Exhaust hole in the output covered
Uncover disassembly hole.
Solenoid valve
does not switch
Valve defective
Replace valve.
Solenoid valve
does not switch
Solenoid coil defective
Check solenoid coil and replace,
if necessary.
Loud switching
noises
High pressure surge
Select larger valve and pipe dia
meter.
Insert bypass valve.
Fig. 7
Note
Adjusting screw
7
may only be adjusted in consultation with Festo professional
personnel.
13
Technical data
General
VZWM
Valve function
2/2, closed monostable
Design
Poppet valve with diaphragm seal, servo controlled
Actuation type
Electrical
Sealing principle
Soft
Type of mounting
In-line installation
Mounting position
Preferably vertical
Medium
Compressed air in accordance with ISO 8573-1:2010
[7:4:4], Inert gases, Water, Neutral liquids
Direction of flow
Non-reversible
Max. viscosity
[mm
2
/s]
22
Temperature of medium gaseous
media
[°C]
–10 …+60
Temperature of medium liquid me
dia
[°C]
+5 …+50
Ambient temperature
[°C]
–10 …+60
Note on materials
Contains materials with PWIS
Materials information for housing
Brass, Stainless steel casting (-R1)
Materials information for seals
NBR
Materials information for armature tube
High-alloy steel
Fig. 8
Characteristics
VZWM-...
G14
N14
G38
N38
G12
N12
G34
N34
G1
N1
G114
N114
G112
N112
G2
N2
Nominal diameter
[mm] 13.5
27.5
40.0
50.0
Nominal diameter (-R1)
[mm] 13.0
25.0
40.0
50.0
Flow factor K
v
[m
3
/h]
1.6
2.0
2.4
8.5
10.7
21.3
27.4
39.0
Standard nominal
flow rate
[l/min]
1400
2100
2400
10000
11700
24000
26400
31000
Differential pressure
[bar]
0.5
0.7
Medium pressure
Gaseous media
[bar]
0.5…6
0.7…10
Liquid media
[bar]
0.5…6
0.7…6
Switching times air
On
[ms]
8
15
26
62
Off
[ms]
10
12
20
21
Switching times liquid media
On
[ms]
100
110
110
400
400
1400
1400
2100
On (-R1)
[ms]
80
110
110
420
300
1400
1400
2100
Off
[ms]
200
210
220
930
930
1900
2000
2800
Off (-R1)
[ms]
210
190
200
950
950
1900
2000
2800
CE marking
1)
No
In accordance with EU pressure equip
ment directive
1)
Declaration of conformity
è
www.festo.com/sp
2)
Switching time adjustable through the regulating screw
Fig. 9