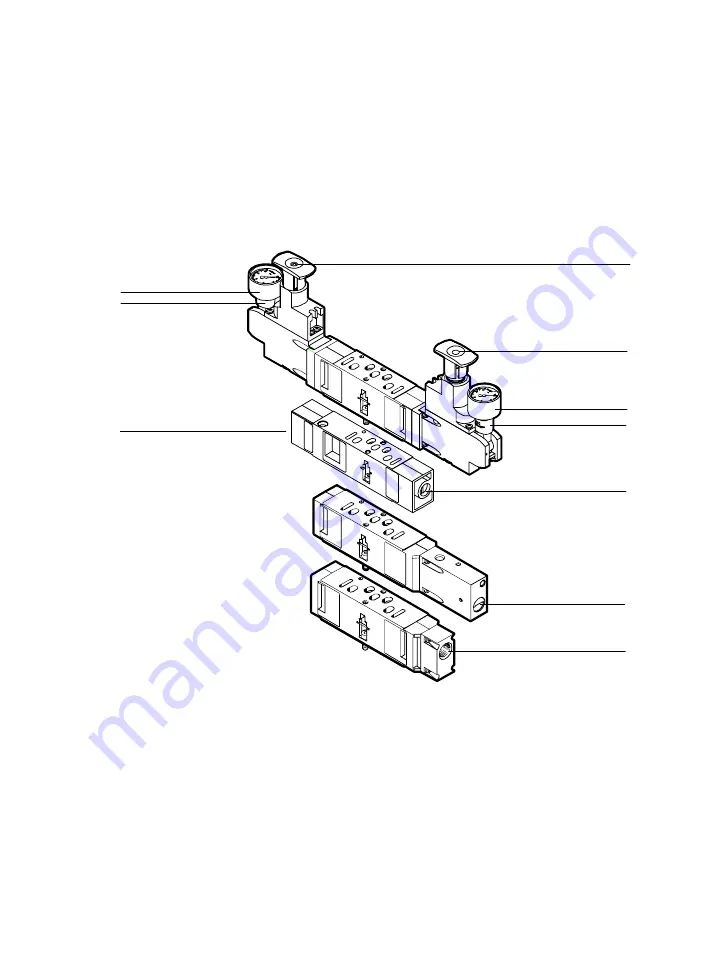
1.
Ov
e
rv
iew
of
c
om
p
o
n
e
nt
s
1
−
19
F
es
t
o
P
.B
E−
V
T
IA
−EN
e
n
1003a
On t
he
c
om
p
o
n
e
nt
s
fo
r v
e
rt
i
c
al
s
t
a
ck
i
ng y
o
u
will
fi
nd t
he
fol
lowi
ng c
o
nn
e
ct
io
n
a
nd c
o
ntr
ol
eleme
nt
s
:
Pr
ess
ur
e
r
e
gu
la
t
o
r p
la
t
e
F
low
c
o
ntr
ol
p
la
t
e
Ve
rt
i
c
al
pr
ess
ur
e
sh
ut−
off
p
la
t
e
Ve
rt
i
c
al
pr
ess
ur
e
s
upp
l
y
p
la
t
e
4
4
5
6
1
2
2
3
1
3
1
P
o
rt
fo
r pr
ess
ur
e
g
a
ug
e
(c
a
n b
e
swi
v
elle
d
90
°)
2
Pr
ess
ur
e
g
a
ug
e
(
o
pt
io
n
al
)
3
A
dju
s
t
i
ng kn
o
b
wi
t
h
f
r
ee
−
wheeli
ng
a
nd
s
n
a
p−
i
n
lo
ck
i
ng
4
A
dju
s
t
i
ng
s
cr
ew
fo
r c
o
ntr
olle
d
flow
5
Op
e
r
a
t
i
ng pr
ess
ur
e
p
l
ug
s
cr
ew
fo
r
o
n
e
v
al
v
e
p
osi
t
io
n
6
Supp
l
y p
o
rt
1
(
i
nd
i
v
i
du
al
o
p
e
r
a
t
i
ng
pr
ess
ur
e
fo
r
o
n
e
v
al
v
e
p
osi
t
io
n)
F
i
g
.
1
/6:
Co
ntr
ol
a
nd c
o
nn
e
ct
io
n
eleme
nt
s
of
t
he
c
om
p
o
n
e
nt
s
fo
r v
e
rt
i
c
al
s
t
a
ck
i
ng
T
he
v
al
v
e
ma
n
ifol
d
wi
t
h
v
al
v
es
wi
t
h
c
ommo
n c
o
nn
e
ct
o
r
s
c
o
n
sis
t
of
t
he
followi
ng
ele
ctr
i
c
al
c
om
p
o
n
e
nt
s
:
Summary of Contents for VTIA Series
Page 2: ......
Page 4: ...Contents and general safety instructions II Festo P BE VTIA EN en 1003a...
Page 8: ...Contents and general safety instructions VI Festo P BE VTIA EN en 1003a...
Page 14: ...Contents and general safety instructions XII Festo P BE VTIA EN en 1003a...
Page 15: ...Overview of components 1 1 Festo P BE VTIA EN en 1003a Chapter 1...
Page 36: ...1 Overview of components 1 22 Festo P BE VTIA EN en 1003a...
Page 37: ...Mounting 2 1 Festo P BE VTIA EN en 1003a Chapter 2...
Page 49: ...Installation 3 1 Festo P BE VTIA EN en 1003a Chapter 3...
Page 57: ...3 Installation 3 9 Festo P BE VTIA EN en 1003a 1 2 3 Fig 3 2 Disconnecting the tubing...
Page 80: ...3 Installation 3 32 Festo P BE VTIA EN en 1003a...
Page 81: ...Comissioning 4 1 Festo P BE VTIA EN en 1003a Chapter 4...
Page 95: ...Conversion and maintenance 5 1 Festo P BE VTIA EN en 1003a Chapter 5...
Page 114: ...5 Conversion and maintenance 5 20 Festo P BE VTIA EN en 1003a...
Page 115: ...Technical Appendix A 1 Festo P BE VTIA EN en 1003a Appendix A...
Page 131: ...Supplementary overview of components B 1 Festo P BE VTIA EN en 1003a Appendix B...
Page 142: ...B Supplementary overview of components B 12 Festo P BE VTIA EN en 1003a...
Page 143: ...Index C 1 Festo P BE VTIA EN en 1003a Appendix C...
Page 144: ...C Index C 2 Festo P BE VTIA EN en 1003a Contents C Index C 1...