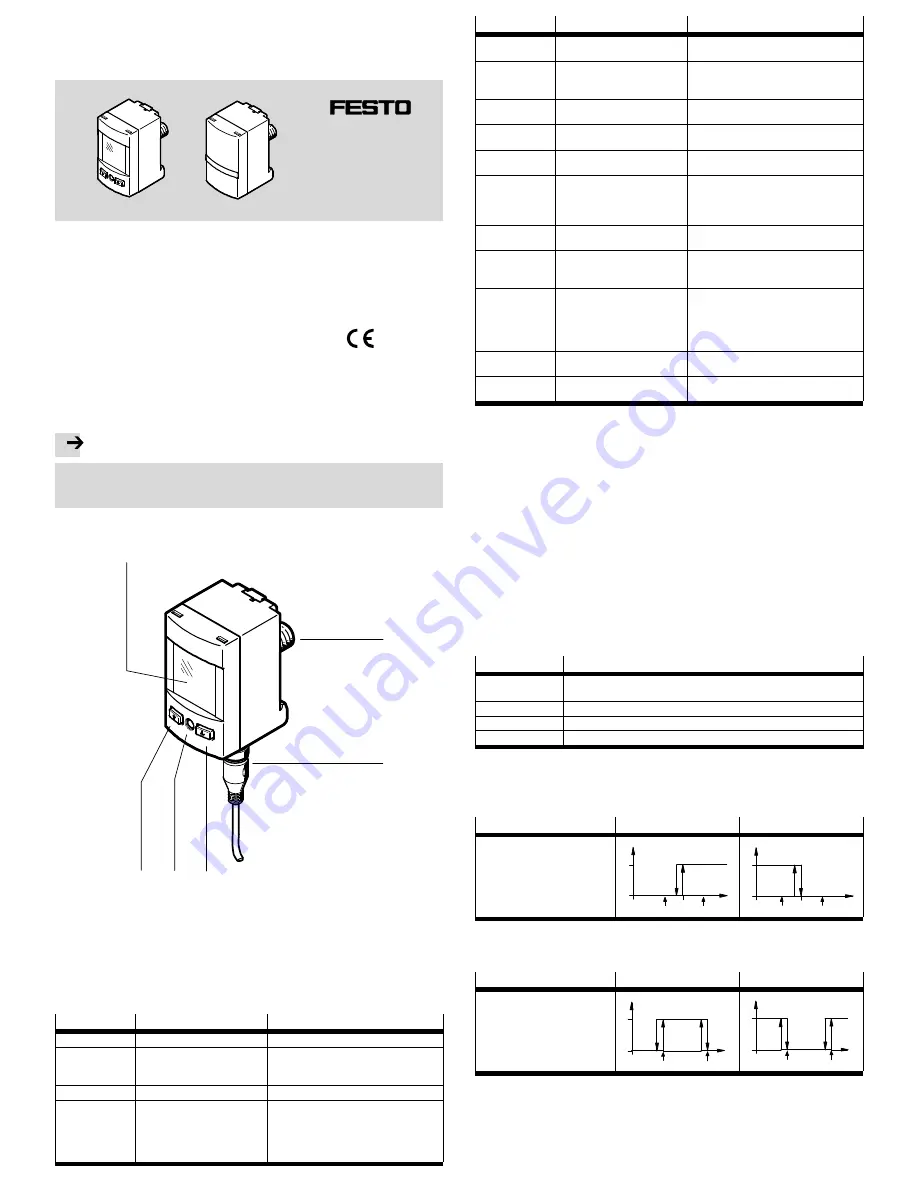
Pressure sensor SPAU
Festo AG & Co. KG
Postfach
73726 Esslingen
Germany
+49 711 347-0
www.festo.com
Operating instructions
8001199
1410NH
[8041211]
Original: de
Pressure sensor SPAU
English
. . . . . . . . . . . . . . . . . . . . . . . . . . . . . . . . . . . . . . . . . .
1
Product description
The operating instructions describe the entire function range. The function range is
limited, depending on the product variant.
Note
You can find detailed specifications for the product, the device description file
(IODD) with a description of the IO-Link parameters and the declaration of
conformity at:
è
www.festo.com.
1.1 Overview
Display variant without front panel mounting
1)
1
2
3
4
5
6
1
Display
2
Pneumatic port
3
Electrical connection
4
B key
5
Edit button
6
A key
1)
Representation of other variants can deviate
from this.
Fig. 1
1.2 Characteristics
Characteristic
Code
Specification
Type
SPAU
Pressure sensor
Pressure
measuring range
-B2, -B11, -P025, -P05, -P1, -P2,
-P6, -P10, -P12, -P16, -V025,
-V05, -V1
è
Technical data
Supply port
R
Relative pressure
Type of mounting
-T
-H
-W
-A
-F
Threaded mounting
H-rail mounting
Wall mounting
Mounting bracket
Front panel mounting
Characteristic
Code
Specification
Pneumatic port
-G18, -R18, N18, -R14, -M5, -M7
-Q4,-Q6,-T532
Thread G
x
, R
x
, NPT
x
, R
¼
, M5, M7
Plug connector
4mm, 6mm,
Â
Thread type
M
F
None
Male thread
Female thread
Outlet direction
D
Rear
Underneath
Display
-L
None
LCD, backlit
Electrical output 1
-PNLK
-LK
Switching output PNP / NPN / IO-Link
IO-Link
Electrical output 2
-PNVBA
-V
-B
-A
PNP / NPN / 0…10 V / 1…5 V / 4…20 mA
0…10 V
1…5 V
4…20 mA
Electrical
connection
-M8
-M12
M8 plug
Plug M12, A-coded
Electrical outlet
direction
D
U
Rear
Underneath
On top
Electrical
accessories
+2.5A
+2.5S
+5A
+5S
None
Angled socket, 2.5 m cable
Straight socket, 2.5 m cable
Angled socket, 5 m cable
Straight socket, 5 m cable
Protective
devices
G
None
Safety guard
Certificate
T
None
Test report
Fig. 2
2
Function and application
The pressure sensor SPAU is intended for monitoring pressure in the piping.
The
sensor converts pneumatic pressure values (relative pressure) into electrical sig
nals, which can be used for control or regulating functions.
Measurements are
carried out using a piezoresistive sensor element with a following electronic evalu
ation unit. Interfacing to the higher-level system is provided by 1 or 2 switching
outputs, an analogue output and/or an IO-Link interface.
The switching outputs can be configured for monitoring of a threshold value, a
pressure range or a differential pressure. For each output, PNP or NPN and nor
mally open (NO) or normally closed (NC) can optionally be set. Via the IO-Link inter
face, process values can be read out and parameters changed and transmitted to
additional devices.
2.1 Operating statuses
Operating status Function
RUN mode
– Initial status after switching on the operating voltage
– Display of the current measured value
SHOW mode
– Display of the current settings
EDIT mode
– Setting or modification of parameters
TEACH mode
– Acceptance of the current measured value to determine switching points
Fig. 3
2.2 Switching functions
Threshold value comparator for monitoring of a pressure threshold
Function
NO (normally open)
NC (normally closed)
Switching function:
– 1 Switching point (SP)
TEACH mode:
– 2 teach-in points (TP1, TP2)
– SP = ½ (TP1+TP2)
TP1 TP2
HY
1
0
Out
p
SP
TP1 TP2
SP
HY
1
0
Out
p
Fig. 4
Window comparator for monitoring of a pressure range
Function
NO (normally open)
NC (normally closed)
Switching function:
– 2 Switching points (SP.Lo, SP.Hi)
TEACH mode
1)
:
– 2 teach-in points (TP1, TP2)
– TP1 = SP.Lo, TP2 = SP.Hi
HY HY
TP1=SP.Lo TP2=SP.Hi
1
0
Out
p
HY HY
TP1=SP.Lo TP2=SP.Hi
1
0
Out
p
1)
SP.Lo = smaller pressure/vacuum value, SP.Hi = larger pressure/vacuum value, dependent on the
Teach sequence
Fig. 5