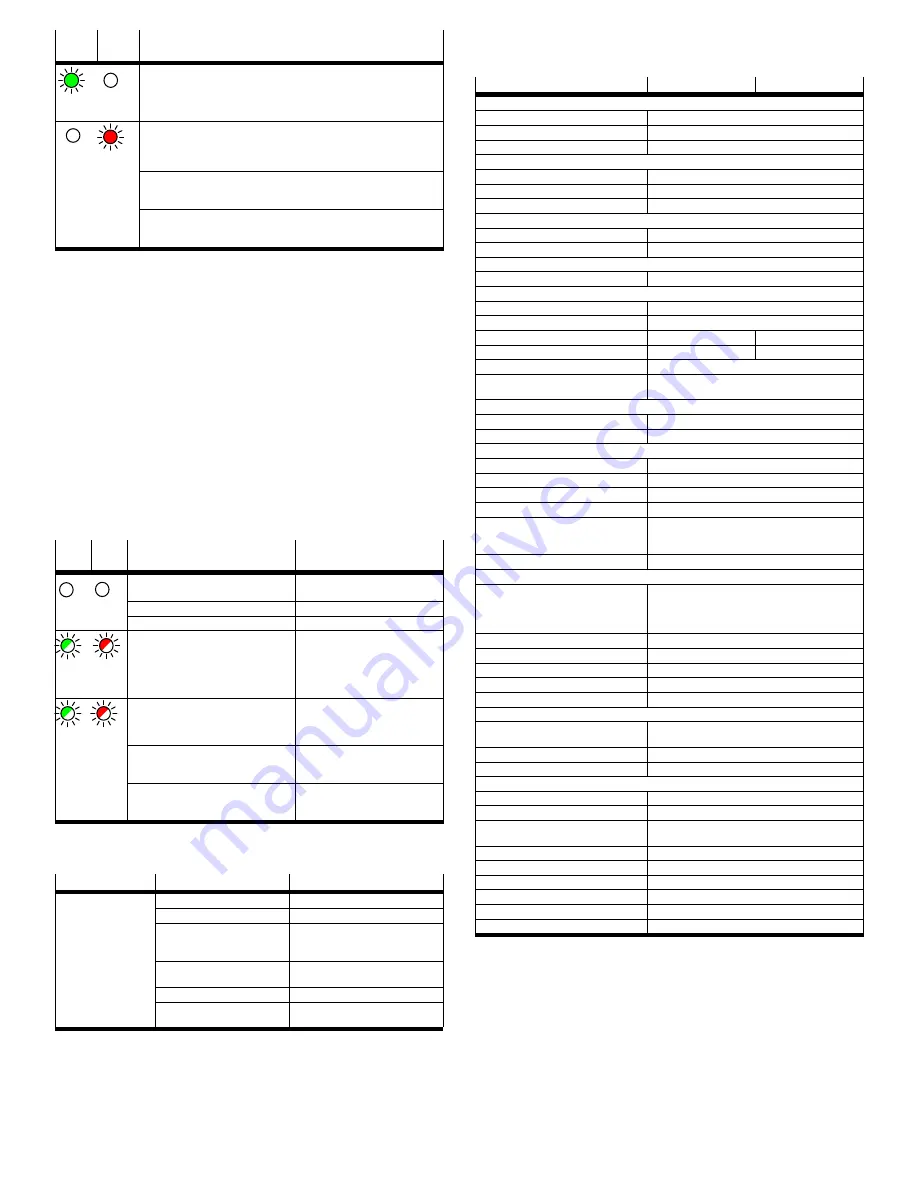
LED displays during operation
LED
Green
LED
Red
Description
Analogue signal >1 V… <10 V:
The piston is inside the measuring range (range B,
è
Fig. 10).
LED Green on,
LED Red off.
Analogue signal 0.5 V:
The piston is outside the measuring range (range A or C,
è
Fig. 10) when
operating voltage is switched on. The SMAT-8M cannot detect the piston's
position.
LED Green off,
LED Red on.
Analogue signal1 V:
The piston has exited the measuring range in the negative direction
1)
(rangeA,
è
Fig. 10). The SMAT-8M can detect the piston's position.
Analogue signal10 V:
The piston has exited the measuring range in the positive direction
2)
(rangeC,
è
Fig. 10). The SMAT-8M can detect the piston's position.
1)
The output voltage falls in the negative direction. The piston moves away from the piston rod.
2)
The output voltage rises in the positive direction. The piston moves towards the piston rod.
Fig. 11
7
Maintenance and care
Cleaning the outside of the SMAT-8M
1. Switch off the operating voltage.
2. Clean the outside of the SMAT-8M with a soft cloth.
Permissible cleaning agents are soapy water (max. +60 °C) and all non-abrasive
agents.
8
Disassembly
1. Switch off the operating voltage.
2. Disconnect the connecting cable from the SMAT-8M.
3. Undo the mounting screw on the SMAT-8M.
4. Remove the SMAT-8M from the slot.
9
Troubleshooting
9.1 Diagnostics via LED
LED
Green
LED
Red
Possible cause
Remedy
Faulty power supply.
Ensure the power supply
(
è
Fig. 4).
Both LEDs off.
Faulty connecting cable.
Replace the connecting cable.
Sensor defective.
Replace SMAT-8M.
Internal error.
Contact your local Festo Service or
[email protected].
LEDs flashing
alternately.
No valid signal.
SMAT-8M not initialised.
Initialise SMAT-8M (
è
chapter 5.2).
LEDs flashing at
the same time.
Power failure during initialisation.
Ensure the power supply and
re-initialise the SMAT-8M
(
è
chapter 5.2).
The magnetic field of the piston/gripper
was not detected correctly by the
SMAT-8M.
Initialise SMAT-8M (
è
chapter 5.2).
Fig. 12
9.2 General malfunctions
Malfunction
Possible cause
Remedy
Incorrect or unexpec
ted signals at the ana
logue output.
Unsuitable drive.
Use suitable drives only.
SMAT-8M defective
Replace SMAT-8M.
No power supply or there is a
non-permissible operating
voltage
Switch on power supply / maintain
permitted operating voltage range
Short circuit or overload at the
output
Remedy short circuit / overload.
Faulty connecting cable.
Replace the connecting cable.
Magnetic object in close prox
imity to position transmitter.
Prevent magnetic objects being in
close proximity.
Fig. 13
10
Accessories
Accessories
è
www.festo.com/catalogue/SMAT-8M.
11
technical data
technical data
Cylinder
Grippers
General
Certification
RCM Mark, c UL us - Listed (OL)
CE marking (
è
declaration of conformity)
In accordance with EU EMC Directive
Note on materials
Conforms to RoHS
Input signal/measuring element
Measured variable
Item
Measuring principle
Magnetic
Measuring range
1)
[mm]
≤ 40
Signal processing
Max. travel speed
[m/s]
3
Typical sampling interval
[ms]
2.8
Output, general
Range resolution
2)
[mm]
≤ 0.05
Analogue output
Analogue output
[V]
0 … 10
Sensitivity
1)
[mm/V]
Measuring range/9 V
Linearity error, typ.
1)
[±mm]
1
0.2
Repetition accuracy
[±mm]
0.1
0.025
Capacitive load max. DC
[nF]
100
Min. load resistance
Voltage output
3)
[kΩ]
2
Output, additional data
Protection against short circuit
Yes
Protection against overloading
Yes
Electronic components
Rated operating voltage DC
[V]
24
Operating voltage DC
[V]
15 … 30
Idle current
[mA]
15 (V
oper
= 24 V)
Ready-state delay
[ms]
≤ 300
Signal run time, typ.
1) 4)
[ms]
14 at v < 0.016 m/s
8.5 at 0.016 < v < 0.05 m/s
5.5 at v > 0.05 m/s
Reverse polarity protection
For all electrical connections
Electromechanical components
Cable test conditions
Energy chain 50 000 cycles, bending radius 30 mm
Torsional strength min. 300 000 cycles, ±270°/0.1 m
Bending strength according to Festo standard, test
conditions upon request
Cable length
[m]
0.3
Max. connecting cable length
[m]
30
Electrical connection
Cable with plug, M8x1, rotatable thread, 4-pin
Pin contact materials
Gold-plated brass
Cable sheath materials
TPE-U (PU)
Mechanical components
Type of mounting
Screw-type union, for insertion into slot from above,
max. torque 0.6 Nm
Housing materials
Reinforced PA6
Union nut materials
Nickel-plated brass
Immission/emission
Storage temperature
[°C]
–25 … +75
Ambient temperature
[°C]
–25 … +75
Ambient temperature with flex
ible cable installation
[°C]
–5 … +70
Recovery time
[ms]
< 2.8 as per DIN 60947-5-7
IP protection (as per EN 60529)
IP65/IP68 (IP68 condition: test duration 24 hrs)
Protection class (as per DIN VDE 0106-1)
III
Resistance to shocks (as per EN 60068-2)
Severity level 2
Vibration resistance (as per EN 60068-2)
Severity level 3
Corrosion resistance class CRC
2
1)
Varies depending on the drive used.
2)
Range resolution = working range/921 (e.g. 0.027 mm for 25 mm working range).
3)
Recommended: connect a resistor to the analogue output, typically 10 kΩ.
4)
The signal run time is longer than the scanning interval because of the dynamic filtering. There are three
velocity-dependent filter stages. The examples are valid for a working range of 20 mm.