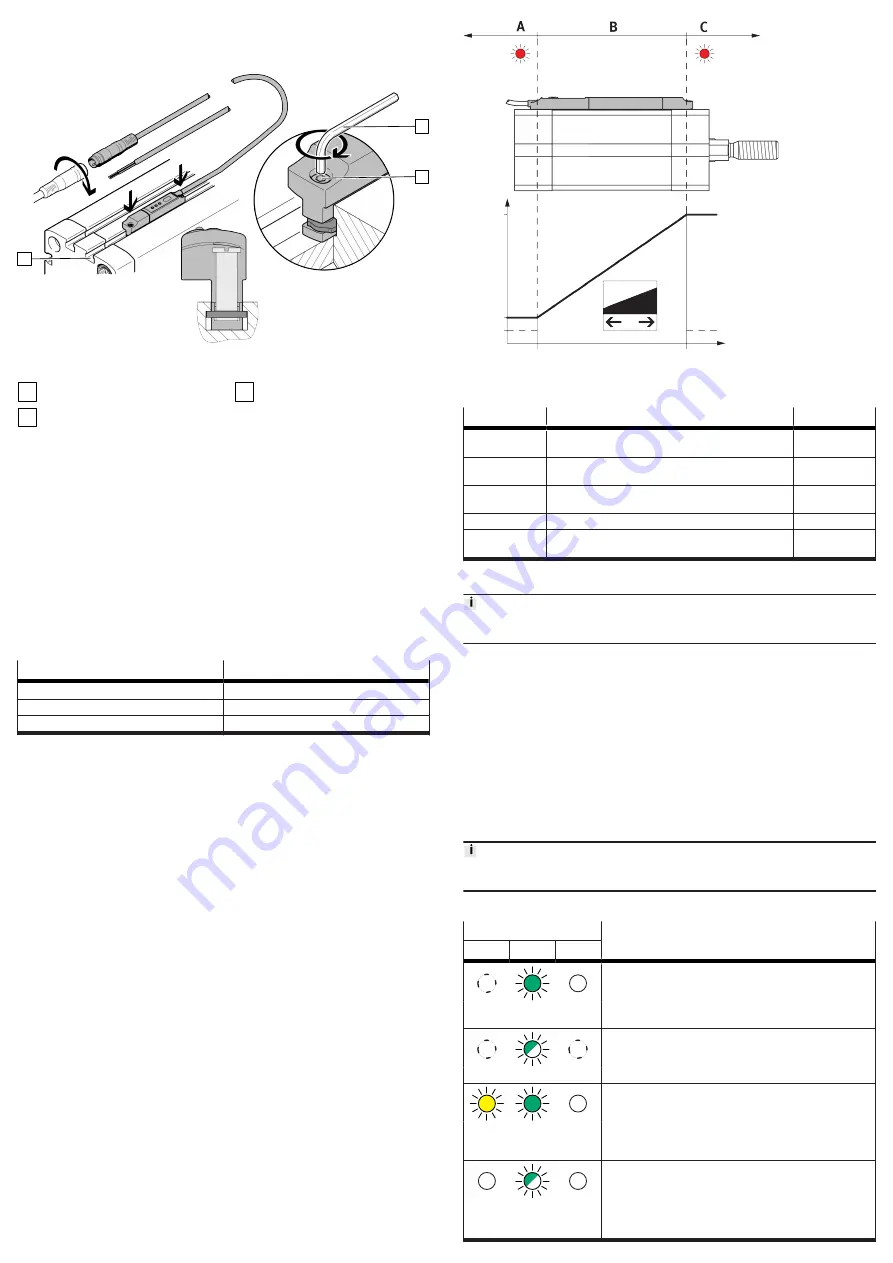
4.
5.2
Mechanical installation
You can mount the MS6-SV-E in any desired position.
1
2
3
Fig. 3: Mechanical installation
1
Hexagon socket spanner
2
Retaining screw
3
T-slot
1. Push the position transmitter into the T-slot of the drive.
2. Move the piston to an end position of the application.
3. Push the position transmitter in the direction of the piston until the red LED
goes out.
Hand-tighten the retaining screw.
–
Max. tightening torque: 0.5 Nm
–
Tool: internal hexagon socket key (size 1.5 mm).
6
Commissioning
6.1
Switch on the position transmitter
•
Switch on the operating voltage.
Ä
The LEDs switch on depending on the position of the piston
LED displays in normal operation.
Ä
The device is ready for operation.
Parameter
Factory setting
Switching function
None
Switching logic
Normally open contact (N/O)
Scaling
Total sensing range
Tab. 3: Factory settings of the position transmitter
6.2
IO-Link Program output
The IO-Link function cannot be set with the operating keys on the device. All set-
tings for set-up, commissioning and parameterisation are made in the higher-level
controller of the IO-Link master.
6.3
Analogue output
The analogue output provides an output signal 4 … 20 mA.
–
The output signal is proportional to the path of the piston stroke in the sensing
range.
0 mm
X mm
20 mA
4 mA
2 mA
Fig. 4: Characteristic curve of the analogue output
X = maximum length of the sensing range
Signal
Description
Range
1)
0 mA
–
IO-Link operation
–
Error, e.g. cable break, parameter error
–
2 mA
–
Piston is outside the sensing range after switching on
the operating voltage
A, C
4 mA
–
The piston has left the sensing range in the direction of
the falling output current
A
>
4 mA …
<
20 mA
–
Piston is within the sensing range
B
20 mA
–
The piston has left the sensing range in the direction of
the rising output current
C
1) Range Fig. 2, range A and C: red LED on
Tab. 4: Output signal of the analogue output
The analogue output is switched off during active IO-Link communication. The
output current is 0 mA.
7
Operation
7.1
Magnetic direction detection and magnetic direction correction
During initial commissioning or after a reset to factory settings, the position
transmitter outputs the signals directly using the currently detected magnetic
direction.
The magnetic direction detection and, with it, the signal curve are corrected
during continuing operation in the following cases:
–
The position transmitter was placed in operation in a position in which it was
not possible to detect a correct magnetic direction, e.g. due to ferromagnetic
materials near the sensor or within the drive or gripper.
–
The position transmitter was rotated 180° in the slot after the magnetic direc-
tion was detected as stable.
Brief error signals may be detected at the sensor output if automatic correction of
the magnetic direction detection is required
7.2
LED displays in normal operation
LED display
Description
Yellow Green
Red
Ready for operation:
–
Analogue output function or switching output operating mode.
–
Piston within the sensing range.
Green LED: on
Red LED: off
Ready for operation:
–
IO-Link operating mode.
Green LED: flashing at 1 Hz
Ready for operation:
–
Switching output switched.
–
Piston in the range of a programmed function.
Yellow LED: on
Green LED: on
Red LED: off
Status indicator:
–
Operating key blocked.
Green LED: flashes 3 s at
3 Hz when the operating key is
pressed