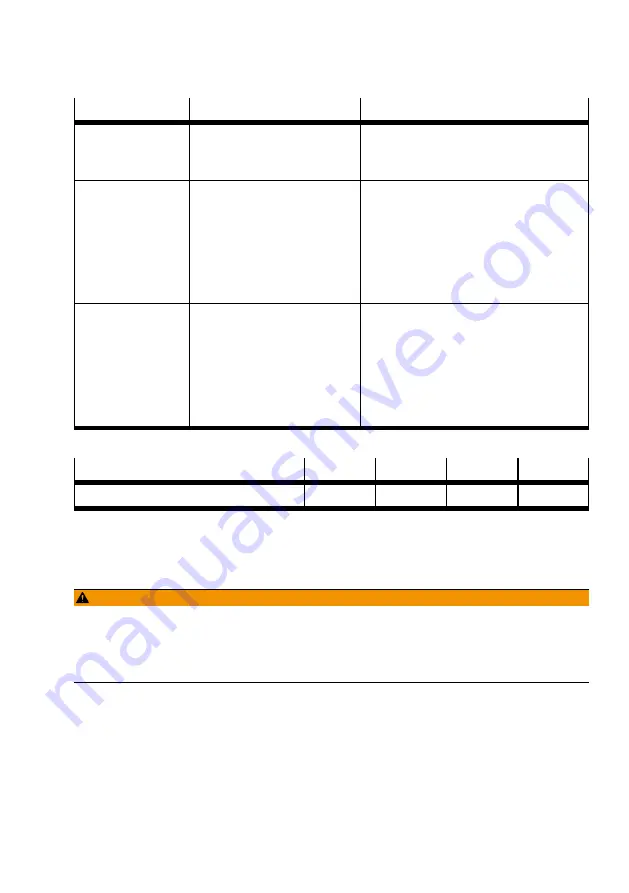
Procedure
Purpose
Note
1. Control travel
Determining the approach direc-
tion of the motor
Even with identical control, motors of the
same design can turn in opposite directions
due to different wiring.
2. Homing
Comparison of real situation to
the image of the controller
Homing takes place:
–
towards the reference switch
–
towards the motor-side end stop. Com-
ply with maximum impact energy
è
Observe additional information
è
Operat-
ing instructions of the drive system.
3. Test run
Checking the overall behaviour
Check the following requirements:
–
The slide moves through the intended
positioning cycle completely.
–
Slide stops as soon as a limit switch is
reached.
After a successful test run, the axis is ready
for operation.
Tab. 2
Size
32
45
60
80
Max. impact energy
1)
[10
-3
J]
0.25
0.5
1.0
2.0
1) max. Speed of homing for all sizes: 0.01 m/s
Tab. 3
9
Service
WARNING!
Unexpected movement of components.
Injury due to impacts or crushing.
•
Before working on the product, switch off the control and secure it to prevent it from being
switched back on accidentally.
Checking wear
•
Regularly check the reversing backlash of the slide for spindle nut wear. The wear on the ball
screw will lead to increased noise in the long term and eventually cause the ball screw drive to
block or the spindle nut to break. The maximum permissible reversing backlash is 0.2 mm.
Checking the cover strip
•
Check the cover strip after every 2000 km of operating distance.
Waves on the cover strip are a sign of wear on the belt reversal device.
Service
11
Festo — ELGC-BS-KF — 2018-08c