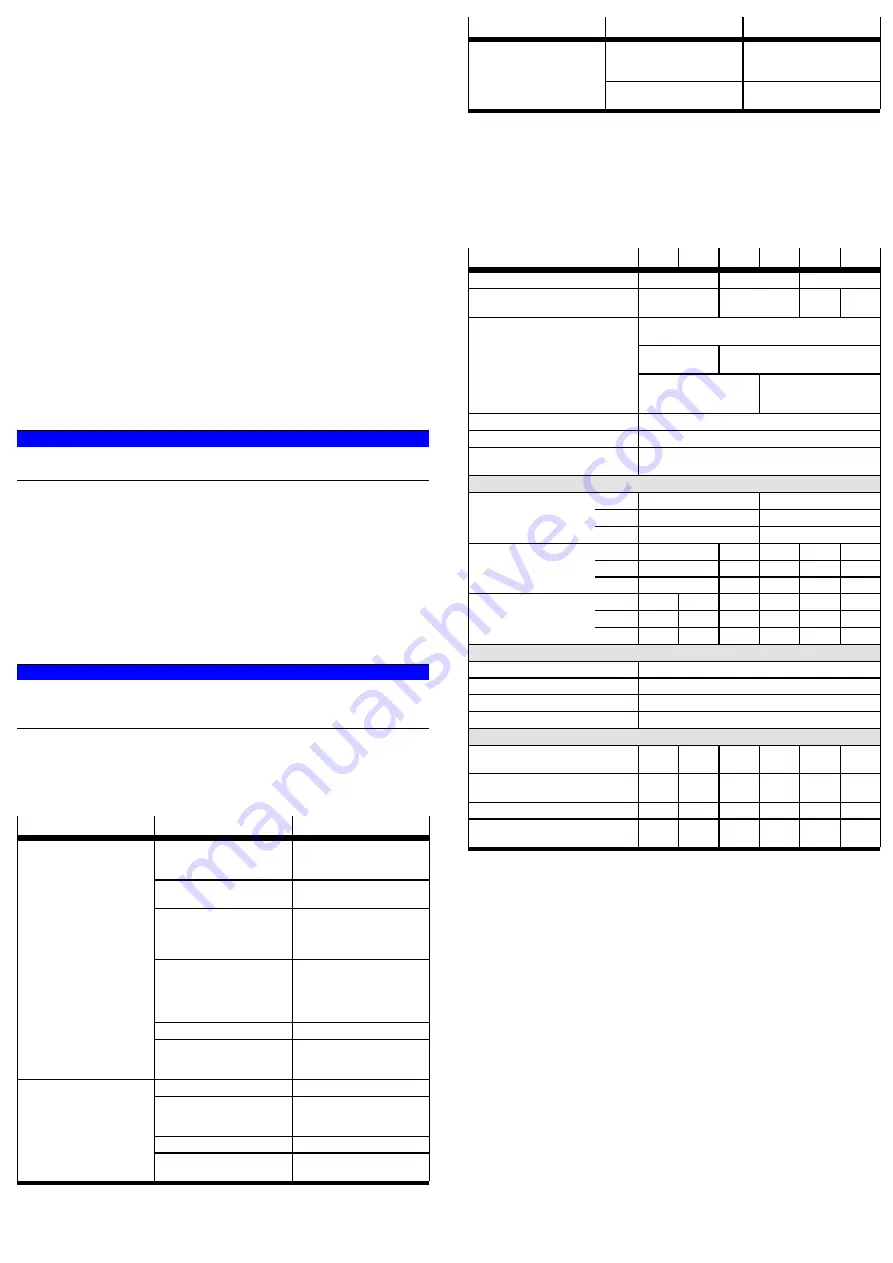
To prevent the payload from sliding down suddenly in the event of an air supply
failure in a horizontal or sloping mounting position:
•
Use piloted check valves.
To set the speed:
•
Use one-way flow control valves in the following supply ports:
–
For single-acting cylinders: GRLZ (supply air)
–
For double-acting cylinders: GRLA (exhaust air)
The one-way flow control valves are screwed directly into the supply ports. Use of
other accessories with a screw-in depth that is too long will damage the cushion-
ing piston.
For position sensing with proximity sensors:
•
Use proximity sensors with mounting kit.
Avoid external influence caused by magnetic or ferritic parts in the vicinity of
the proximity sensors (spacing
³
10 mm).
6
Installation
6.1
Pneumatic installation
•
Connect hoses to supply ports
3
.
7
Commissioning
7.1
Preparation
•
Pressurise the system slowly. A soft start valve is used for gradual start-up
pressurisation
è
With medium or large payloads or at high speeds:
•
Use sufficiently large arrester fixtures. The product will tolerate the maximum
velocities and payloads without external arrester fixtures
è
7.2
Processing
NOTICE!
Risk of collision due to payloads that project into the setup region of the product.
•
Only turn adjusting screws while the product is stationary.
1. First of all, close the one-way flow control valves on both sides completely,
then unscrew them one complete turn.
2. Pressurise the cylinder simultaneously at both ends.
Ä
The piston rod moves slightly to a point of balance.
3. Exhaust the cylinder at one end.
Ä
The piston rod moves to an end position.
4. Start the test run.
5. If the piston rod strikes hard against the end positions or rebounds, correct
the speed using the one-way flow control valve.
8
Maintenance
8.1
Cleaning
NOTICE!
•
Do not use aggressive cleaning agents.
•
Do not clean the guide elements. Regularly removing the lubricant from the
surface of the piston rod reduces the service life.
•
Clean the product with a soft cloth.
The cylinder is furthermore maintenance-free owing to the lifetime lubrication.
9
Malfunctions
9.1
Fault clearance
Fault description
Cause
Remedy
Lack of lubricant.
Apply lubricant in accordance
with wearing parts sheet
è
One-way flow control valves
restrict the flow of supply air.
Control the exhaust air flow if
possible (not the supply air).
Piston rod is dirty.
–
Clean the cylinder.
–
Provide covering (relubric-
ate after thorough clean-
ing).
Insufficient supply air (stick
slip)
–
Keep the tubing lines
short and select suitable
cross-sections.
–
Select correct pressure.
–
Keep pressure constant.
Pressure is too low.
Connect volume upstream.
Irregular movement of the pis-
ton rod (cylinder jolts).
Guide is not parallel to direction
of stroke.
Use self-aligning rod coupler as
in accessories
è
Cylinder barrel is damaged.
Replace cylinder.
Setting screw for end-position
cushioning is completely
closed.
Loosen setting screw.
Foreign matter in the cylinder.
Filter the compressed air.
Piston does not travel to end
position.
Cylinder travels to an external
end stop.
Readjust the end stop.
Fault description
Cause
Remedy
Temperatures too high or too
low.
Comply with permissible tem-
perature range of the proximity
sensors.
False triggering during position
sensing.
Fault at proximity sensor
è
Instruction manual for prox-
imity sensor
Tab. 2 Fault clearance
10
Disposal
Dispose of the product and packaging at the end of its useful life through environ-
mentally friendly recycling in accordance with applicable regulations.
11
Technical data
DSNU-8 … 25
Size
8
10
12
16
20
25
Pneumatic connection
M5
M5
G1/8
Piston rod thread
M4
M6
M8
M10x
1.25
Elastic cushioning rings/plates, at both ends (P cushion-
ing)
–
Pneumatic cushioning, can be adjus-
ted at both ends (PPV cushioning)
End-position Cushioning
–
Pneumatic cushioning, self-
adjusting at both ends (PPS
cushioning)
Mounting position
Any
Operating medium
Compressed air as per ISO 8573-1:2010 [7:4:4]
Notes on the
operating/pilot medium
Lubricated operation possible (in which case lubricated
operation will always be required)
Operating pressure
DSNU-...
[MPa]
0.15 … 1
0.1 … 1
[bar]
1.5 … 10
1 … 10
[psi]
21 … 145
13.8 … 145
DSNU-...-S10
[MPa]
–
0.05
0.03
0.03
0.03
[bar]
–
0.5
0.3
0.3
0.3
[psi]
–
6.9
4.2
4.2
4.2
DSNU-...-L
[MPa]
0.06
0.06
0.06
0.05
0.05
0.04
[bar]
0.6
0.6
0.6
0.5
0.5
0.4
[psi]
8.3
8.3
8.3
6.9
6.9
5.6
Ambient temperature
DSNU-...
[°C]
–20 … +80
DSNU-...-A1
[°C]
0 … +80
DSNU-...-S6
[°C]
0 … +120
DSNU-...-S10/-L
[°C]
+5 … 80
Theoretical force at 6 bar/0.6
MPa/90 psi, advance
[N]
30
47
68
121
189
295
Theoretical force at 6 bar/0.6
MPa/90 psi, return
[N]
23
40
51
104
158
247
Basic weight
[g]
34.6
37.3
75
89.9
186.8
238
Additional weight per 10 mm
stroke
[g]
2.4
2.7
4
4.6
7.2
11
Tab. 3 Technical data for DSNU-8 to DSNU-25