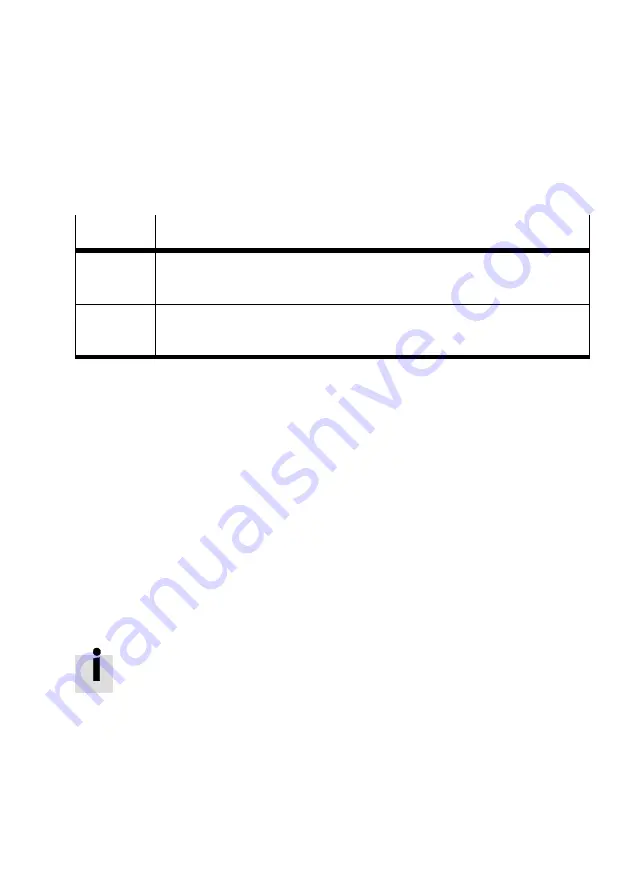
5
Sequence control and I/O data
Festo – GDCP-CMMO-ST-LK-C-HP-EN – 2017-05b – English
29
5
Sequence control and I/O data
5.1
Setpoint specification (FHPP operating modes)
The FHPP operating modes differ as regards their contents and the significance of the cyclic I/O data
and in the functions which can be accessed in the motor controller.
Operating
mode
Description
Record
selection
A specific number of positioning records can be saved in the motor controller. A re
cord contains all the parameters which are specified for a positioning job. The record
number is transferred to the cyclic I/O data as the setpoint or actual value.
Direct
application
The positioning task is transferred directly in the I/O telegram. The most important
setpoint values (position, velocity, torque) are transmitted here. Supplementary
parameters (e.g. acceleration) are defined by the parameterisation.
Tab. 5.1
Overview of FHPP operating modes with motor controller CMMO-ST
5.1.1
Switching the FHPP operating mode
The FHPP operating mode is switched by the CCON control byte (see below) and a feedback signal
returned in the SCON status word. Switching between record selection and direct application is only
permitted in the “ready” status
è
5.1.2
Record selection
Each motor controller has a specific number of records, which contain all the information needed for
one positioning job. The record number that the motor controller is to process at the next start is trans
ferred in the controller’s output data. The motor controller reports the last-executed record number in
the input data of the controller. The positioning job itself does not need to be active.
The motor controller does not support an automatic mode, i.e. no user program. The motor controller
cannot accomplish any significant tasks as stand alone – close coupling to the controller is always ne
cessary. However, it is possible to link various records and execute them one after the other with the
help of a start command. It is also possible to execute record switching before the target position is
reached.
In this way, positioning profiles can be created without the time delays, which arise from
the transfer via the fieldbus and the cycle time of the controller.
5.1.3
Direct application
In the direct application, positioning tasks are formulated directly in the controller’s output data.
The typical application calculates the target setpoint values dynamically. This makes it possible to ad
just the system to different workpiece sizes, for example, without having to re-parametrise the record
list. The positioning data are managed completely in the controller and sent directly to the motor con
troller.
Summary of Contents for CMMO-ST-C5-1-LKP
Page 182: ......