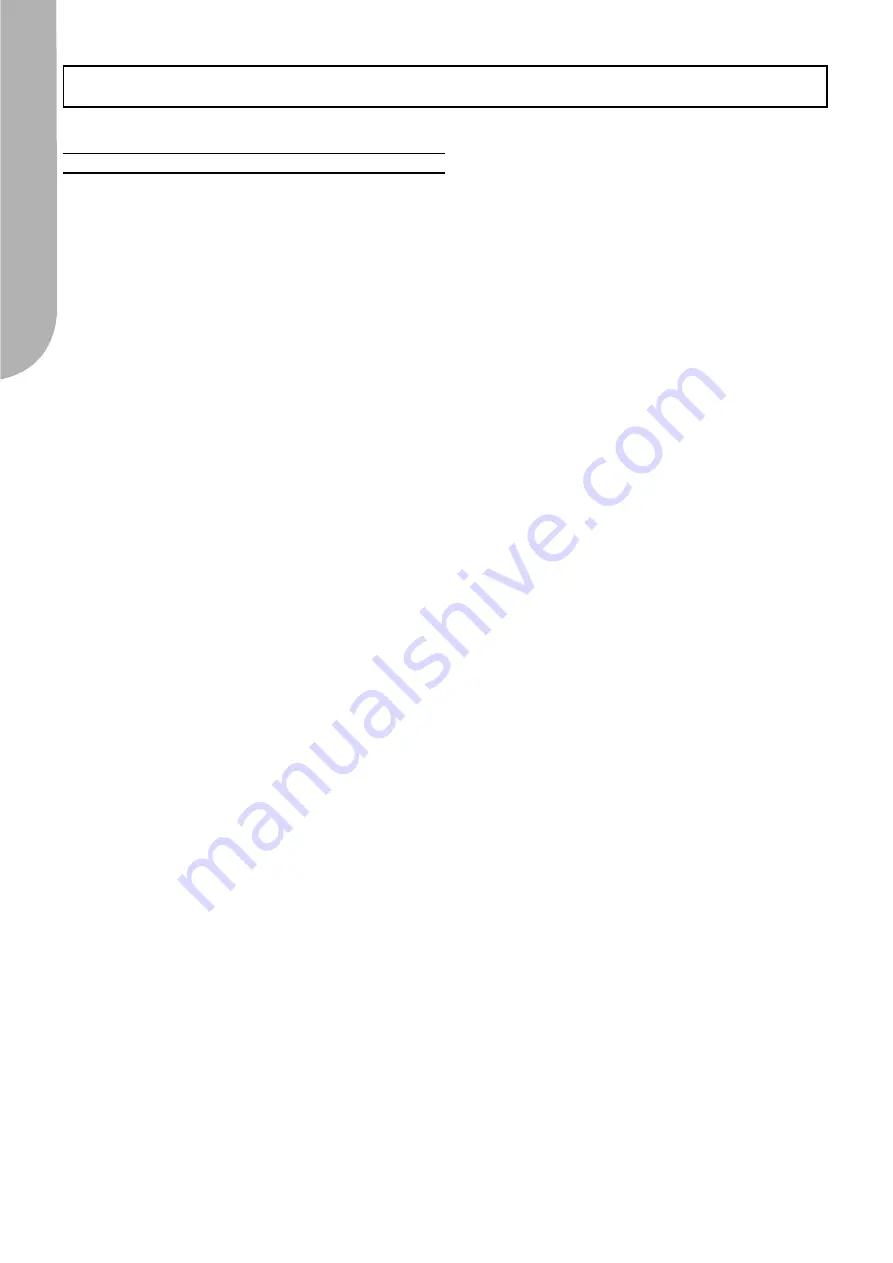
22
ENGLISH
ENGLISH
WET CONNECTIONS
General rules
Comply with the local safety laws in order to plan the hydraulic circuit in the correct way. A mesh filter (
holes Ø
≥≥
500 µm
) must
be installed on the inlet to the plate type exchanger for versions of the units without the Storage and Pumping Module, so as to
keep out any impurities. Failure to do this will void the warranty..
The following indications are merely suggestions about how to install the unit correctly.
Standard supply.
-
Standard supply includes a differential pressure switch situated between the plate type exchanger’s water inlet and outlet to
prevent faults caused by freezing in the absence of water. The activation setting is for a
∆∆
p of 80 mbar ±5
, while resetting
occurs with a
∆∆
p of 105 mbar ±5
.
General suggestions for the hydraulic circuit
-
Pipes must be sized with the least possible number of curves to minimize the water pressure drop. They must also be ade-
quately supported to prevent the exchanger (basic unit) or tank (unit used in conjunction with the Storage and Pumping Module)
connections from being excessively stressed.
-
Install on-off valves near components that need servicing so that they can be isolated when maintenance work is required and
allow replacements to be made without the system having to be emptied.
-
Before isolating the pipes and filling the system, first check to make sure that there are no leaks anywhere in the system.
-
Insulate the refrigerated water pipes to prevent condensation from forming along their length. Make sure that the material used
is the steam barrier type. Failing this, cover the insulation with an appropriate protection. Also make sure that the air venting
valve is accessible through the insulation.
-
Also remember to install or at least prepare for the installation of instruments for reading the pressure and temperature values
in the hydraulic circuit, both on the inlet and outlet sides of the unit. These instruments will allow the operation of the system
to be monitored.
Installation without Pumping and Storage Module
-
The circuit must be kept pressurized by using a surge chamber in combination with a safety valve and pressure reducer. A fil-
ling unit, that automatically charges and maintains the required pressure below a certain value, can be used to fill the system.
Install manual or automatic valves in the highest point of the circuit, to eliminate the air from this latter.
-
Instal a gauze filter (
hole Ø
≤≤
500 µm
) to retain foreign bodies.
-
If vibration dampers are fitted under the unit, it is also advisable to use flexible couplings that eliminate vibrations before and
after the water circulation pump and near the actual unit itself.
- If the system comprises a unit + Storage and Pumping Module and vibration dampers are fitted under the unit, it is also advi-
sable to use flexible couplings that eliminate vibrations before and after the water circulation pump and near the actual unit
itself.
Installation with Pumping and Storage Module
-
Install a cock on the outlet of the Storage and Pumping Module so as to regulate the water that flows to the system.