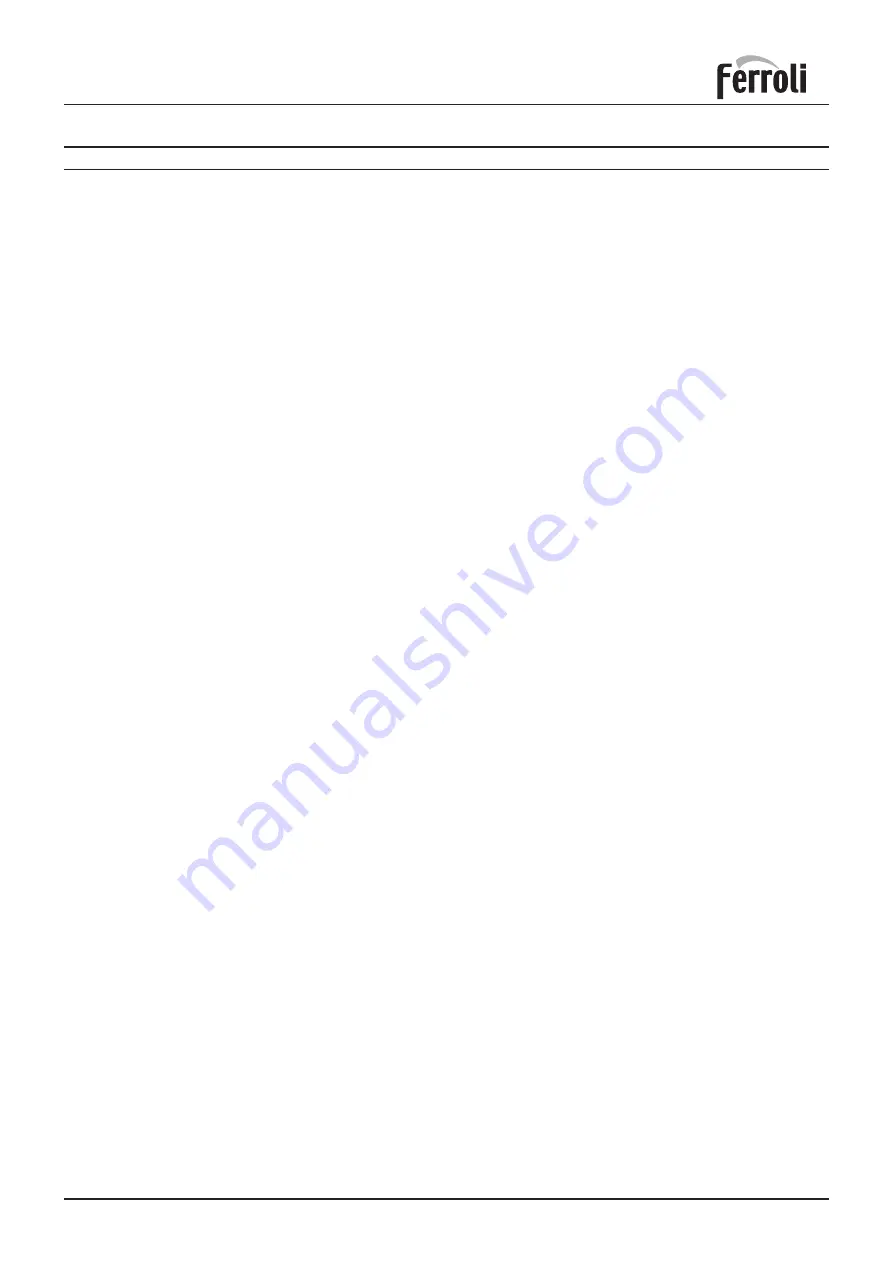
Ferroli F24
9
3. INSTALLATION DETAILS
Gas Safety (Installation & Use) Regulations: 1996
In the interest of safety,
it is the law
that all gas appliances are installed by a competent person in accordance
with the above Regulations, Building Regulations/Building Standards Scotland, Codes of Practice, current I.E.E.
Regulations and the byelaws of the Local Water Undertaking.
Failure to comply with the Regulations may lead to
prosecution; it is your responsibility to ensure that the law is complied with.
N.B.
For Northern Ireland the rules in force apply.
Important
- If the boiler is to be fitted in a timber framed building it should be fitted in accordance with the Institute of
Gas Engineers document IGE/UP/7. If in doubt advice should be sought from the Local Supplier.
Location of Boiler
The installation of the Ferroli F24 must be on a suitable non-combustible load bearing wall which will provide
an adequate fixing for the boiler mounting bracket assembly. The location should be in an area where
the water pipes will not be subjected to frost conditions. In siting the combination boiler the following
limitations
must
be observed:
The combination boiler may be installed in any room or internal space, although particular attention is drawn
to the requirements of the current I.E.E. wiring regulations and in Scotland the electrical provisions of the
building regulations applicable in Scotland, with respect to the installation of the combination boiler in a room
or internal space containing a bath or shower.
Where a room sealed appliance is installed in a room containing a bath or shower any electrical switch
or appliance control utilising mains electricity must be situated so that it cannot be touched by a person
using the bath or shower.
Air Supply
The room or compartment in which the boiler is installed does not require a purpose provided vent when
using the standard concentric flue.
Flue System
The boiler allows the flue outlet to be taken from the rear of the boiler, from either side or vertically.
A standard flue length of 0.75 metres is provided. Alternative lengths of two or three metres can be supplied
(equivalent to wall thicknesses of up to 565, 1815 and 2815mm for rear flues, deduct 91mm plus distance from side
wall for side outlet flues). It is absolutely
essential
,
to ensure that products of combustion discharging from the
terminal cannot re-enter the building, or enter any adjacent building, through ventilations, windows, doors,
natural air infi ltration or forced ventilation/air conditioning
.
Gas Supply
If necessary the local Gas supplier should be consulted, at the installation planning stage, in order to establish
the availability of an adequate supply of gas.
An existing service pipe must
not
be used without prior consultation with the Local Gas supplier.
A gas meter can only be connected by the Local Gas supplier, or by a Local Gas suppliers Contractor.
Installation pipes should be fitted in accordance with BS6891-1988.
Appliance inlet working pressure must be 20mbar MINIMUM, for NG and 37 mbar minimum for LPG.
Pipework from the meter to the combination boiler must be of an adequate size.
The boiler requires 2.73m
3
/h of natural gas, and 2,00 kg/h of LPG.
Do not use pipes of a smaller size than the combination boiler inlet gas connection.
The complete installation must be tested for gas soundness and purged as described in BS6981-1988. All pipework
must be adequately supported. An isolating gas valve is provided and should be fitted on the boiler gas inlet.
Please wait 10 minutes when lighting from cold before checking gas rate.
Gas pressures should be checked after
the boiler has operated for 10 minutes to reach thermal equilibrium.
Water System
Note - the boiler is designed for sealed systems only and must NOT be used on open vented systems.