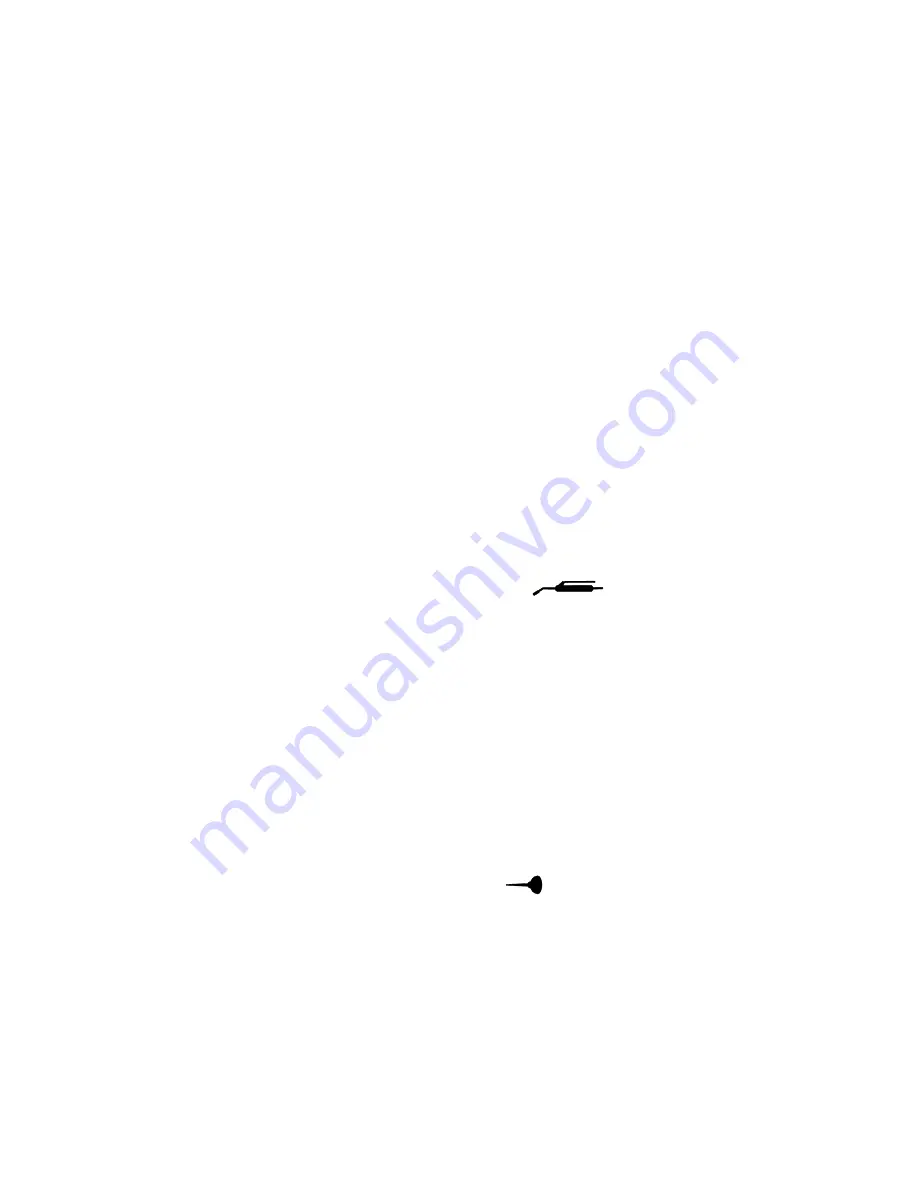
Not for
Reproduction
30
2. Remove the three 1/4” filter guard screws (C) and the
filter guard (B).
3. Clean the area around the filter base and remove the
filter.
4. Apply a film of new oil to the gasket of the new
replacement filter. After the oil has drained, thread the
new filter onto the filter base until the gasket makes
contact, then tighten 3/4 of a turn more.
5. Reinstall the filter guard with the three 1/4” filter guard
screws.
6. Locate the port plug (D) on your transmission.
• If your unit has hydraulic hoses that connect to the
side of the transmission then the port is located
on the top of the transmission. See Figure 28 for a
reference to the port location.
• If your unit has hydraulic hoses that connect to the
top of the transmissions then the port is located on
the side of the transmission. See Figure 29 for a
reference to the port location.
7. Using a hex bit swivel socket or a modified allen wrench
remove the top port plug from the transmissions.
8. Remove the transmission oil tank cap and fill with oil
until oil appears at the bottom of the transmission’s port
(approximately 2 qts (1,89 L).
9. Reinstall the port plug and tighten to 15 ft lbs (20,38 Nm).
10. Continue to add oil to the transmission oil expansion tank
until the oil level reaches the “FULL COLD” mark. Put the
transmission oil tank cap back on and hand tighten.
11. Repeat this process for the other side of the machine.
12. Perform the
Purging the Air from the Hydraulic
System
procedure.
Purging the Air from the Hydraulic
System
Due to the effects air has on efficiency in hydraulic drive
systems, it is critical that it be purged from the system.
These purge procedures should be implemented any time a
hydraulic system has been opened to facilitate maintenance
or any additional oil has been added to the system.
The resulting symptoms of air in the hydraulic system may be:
• Noisy operation.
• Lack of power or drive after short term operation.
• High operation temperature and excessive expansion of
oil.
Before starting, make sure the transaxles/transmissions are
at the proper oil levels. If it is not, fill to the specifications
outlined in the
Check / Fill Transmission Oil Level
procedure.
Purging Air from the Hydraulic System:
1. Chock the front wheels to prevent the unit from rolling.
Raise the rear of the unit so that the unit's rear tires do
not contact the ground. Position jack stands under the
rear bumper of the unit to secure it.
2. Open the transaxle’s bypass valves (see
Pushing the
Unit by Hand
for the location and function of the bypass
valves), start the engine, release the parking brake, and
slowly move the unit’s ground speed control levers in both
forward and reverse directions (5 to 6 times), as air is
purged from the unit, the oil level will drop.
3. Stop the engine and engage the parking brake.
4. Close the transaxle’s bypass valves, start the engine,
release the parking brake, and slowly move the unit’s
ground speed control levers in both forward and reverse
directions (5 to 6 times), as air is purged from the unit, the
oil level will drop.
5. Stop the engine. Remove the jack stands from
underneath the unit.
6. Repeat the process detailed above but with the unit's
drive wheels on the ground. The procedure should be
performed in an area free of any objects or bystanders.
It may be necessary to repeat the process detailed above
until all the air is completely purged from the system. When
the transaxles/transmissions operate at normal noise levels
and move smoothly forward and reverse at normal speeds,
then the transaxles/transmissions are considered purged.
Lubrication
Lubricate the unit at the location shown in the following
figures as well as the lubrication points listed below.
Grease:
• front caster wheel axles and yokes
• transmission cradle pivots
• deck lift pivot blocks
• mower deck spindles
Use grease fittings when present. Disassemble parts to apply
grease to moving parts when grease fittings are not installed.
Not all greases are compatible. Your product is manufactured
using Heavy Duty Lithium Complex EP, NLGI grade 2 grease
(p/n 5109902X1). It is recommended that you service your
product with similar grease. 5109902X1 is available through
your normal part source. Using non-compatible grease could
damage or cause premature parts failures.
Oil:
• ground speed control lever pivots & linkages
• parking brake shaft pivots
• seat plate pivots
• deck lift pivot points
• discharge chute hinge
Generally, all moving metal parts should be oiled where
contact is made with other parts. Keep oil and grease off belts
and pulleys. Remember to wipe fittings and surfaces clean
both before and after lubrication.