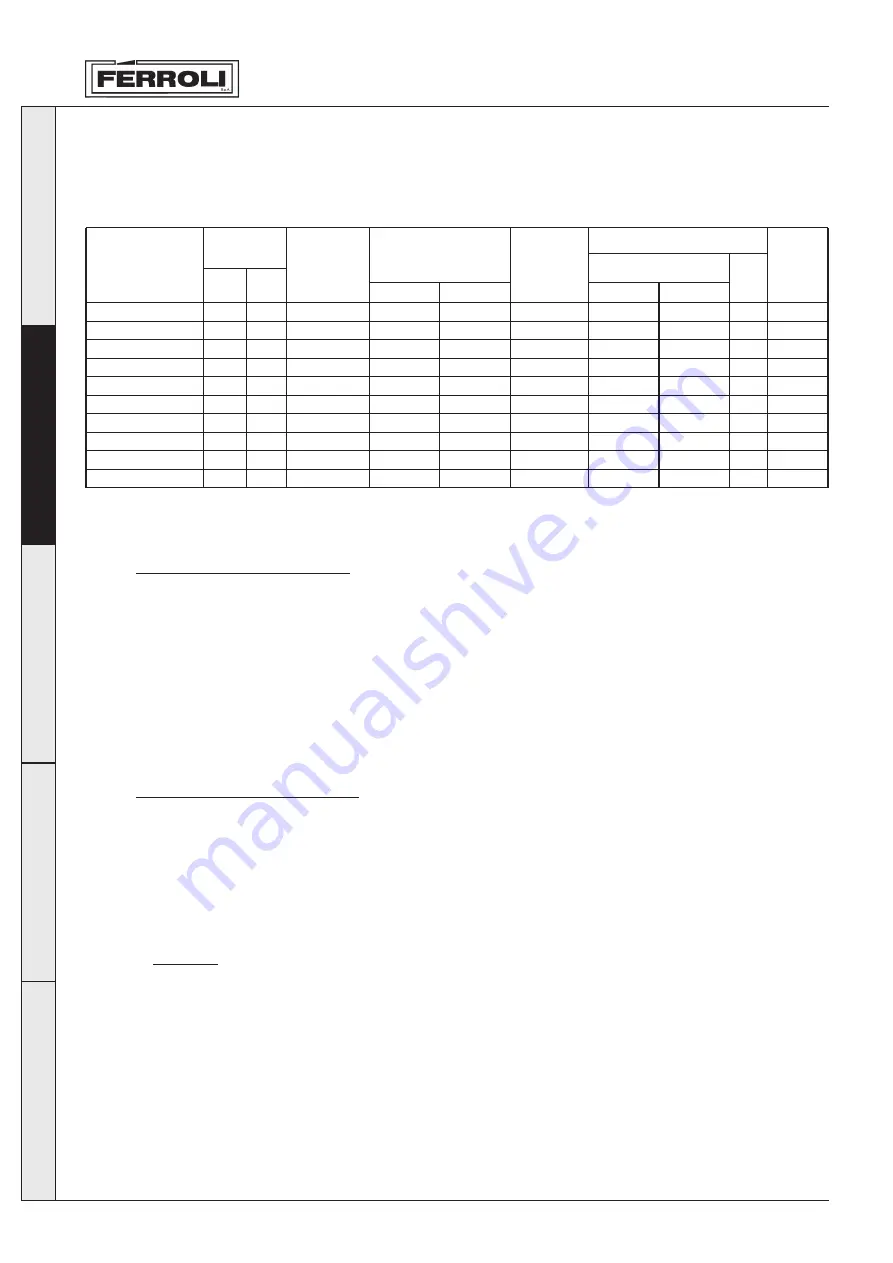
32
SUN G50 - G70
Italiano
English
Français
Deutsch
Español
Adjusting pump pressure
The pressure of the pump is factory-set to 12 bars, for optimum operation, and normally should not be
modified. Nonetheless, if under specific circumstances a different pressure needs to be set, once having
attached the pressure gauge and ignited the burner, use the adjustment screws “6” indicated in fig. 4.
In any case, it is recommended to keep within the range 10 - 14 bars.
3.2 Commissioning
Checks to be performed on first ignition, and after all maintenance operations that involve the
disconnection of the appliance from systems or intervention on the safety devices or parts of the burner:
Before igniting the burner
• Check that the burner is correctly fastened to the boiler, and the preliminary adjustments described
previously have been performed.
• Make sure that boiler and the system have been filled with water or diathermic oil, that the valves in
the water circuit are open and that the flue gas exhaust pipe is free and correctly sized.
• Check that the boiler door is closed, so that the flame only propagates inside the combustion chamber.
• Fit the pressure gauge and the vacuometer to the pump (removed before operation).
• Open the gate valves in the oil pipes, making sure that there is fuel in the tank and that the return pipe
is not blocked.
Attention: Blockages may cause the pump seal device to break.
To perform a preliminary adjustment of head and air damper during installation (before commissioning
and consequently calibrating the appliance using instruments), use the graph below:
Nozzles
Heat
output
Model
GN4.10
GN4.11
GN4.12
GN4.13
GN4.14
Prextherm N 400
Prextherm N 500
Prextherm 550
Prextherm 620
Prextherm 800
4,5
5
6
7
8,5
5,5
7,5
7
8,5
10,5
1st stage
Pump
pressure
12
14
13
12
12
12
11
12
12
12
bar
Burner
G50
G50
G50
G70
G70
G50
G50
G70
G70
G70
Servomotor
air
12
°
13
°
14
°
8
°
10
°
14
°
16
°
8
°
10
°
15
°
1st stage
10
17
20
10
15
20
25
10
15
25
2nd stage
15
°
15
°
20
°
15
°
15
°
15
°
15
°
15
°
15
°
20
°
EV
388
452
516
600
695
435
541
598
674
870
Max
kW
min
kW
229
266
309
352
416
279
345
359
404
522
3
3,5
4
5
5,5
3,5
4,5
5
5,5
7
2nd stage
L (mm)
27
24
22
22
22
23
22
22
22
22